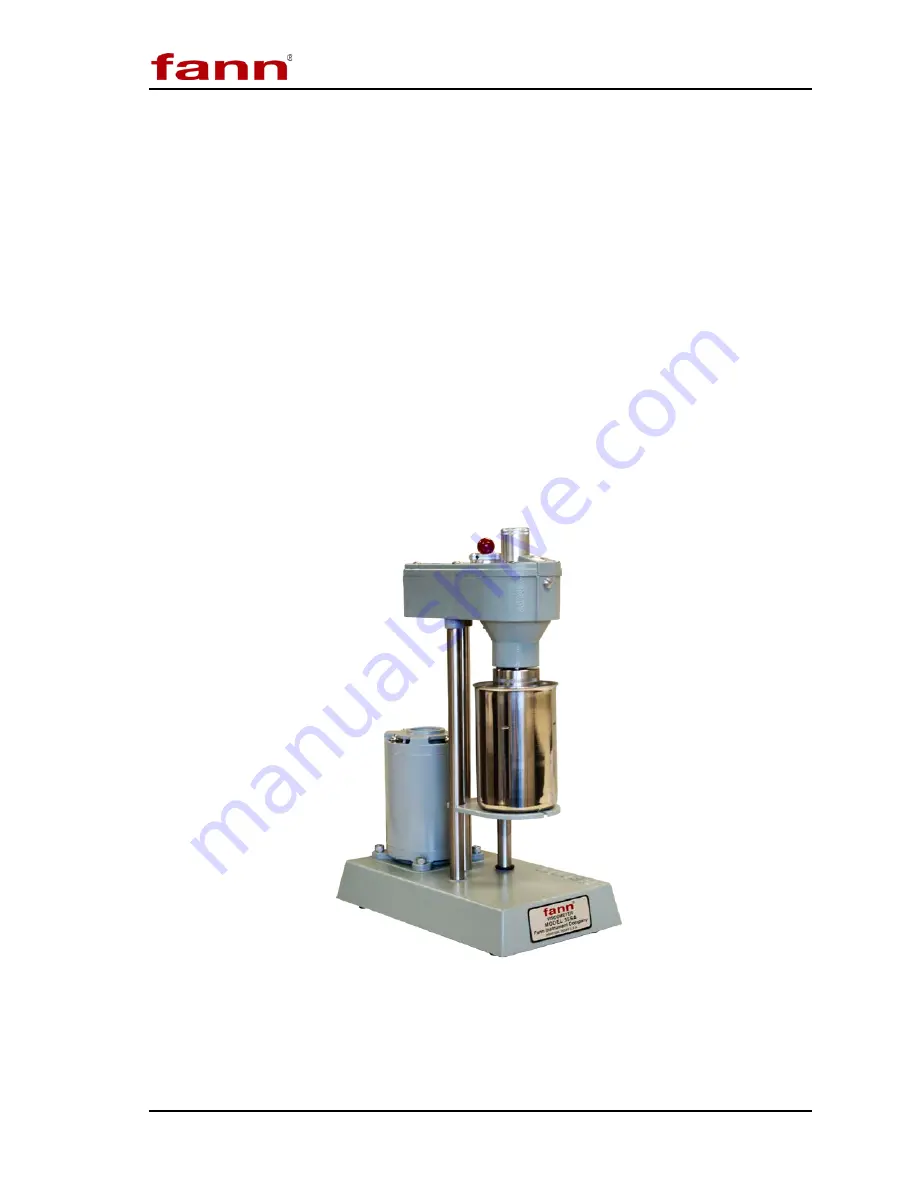
Model 35 Viscometer Instruction Manual
208878
Revision N, February 2013
9
3
Features and Specifications
The Fann direct-indicating viscometers are equipped with the standard R1 rotor
sleeve, B1 bob, F1 torsion spring, and a stainless steel sample cup. Other rotor-bob
combinations and/or torsion springs can be substituted to extend the torque
measuring range or increase the sensitivity of the torque measurement.
Each viscometer is supplied with a 115 volt motor. For operation on 230 volts, a
step-down transformer is required.
The viscometers are available in six-speed and twelve-speed models.
See Table 3-1, 3-2, 3-3, and 3-4 for specifications. Table 3-5 lists the recommended
environmental conditions for use.
Figure 3-1 is a picture of the viscometer and Figure 3-2 is a detailed drawing that
names the individual parts.
Figure 3-1 Model 35SA Viscometer