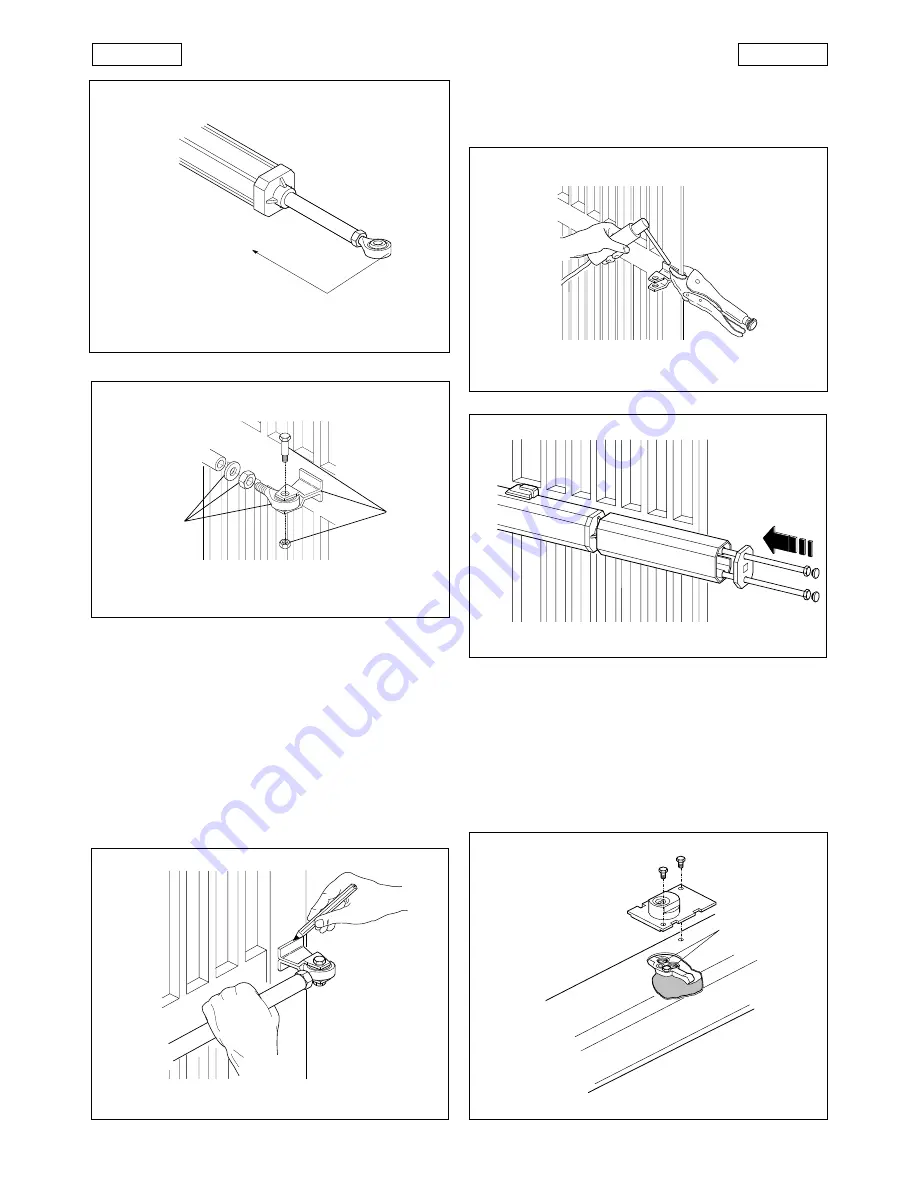
11
ENGLISH
ENGLISH
Fig.10
with no stiff points and that it stops on the phisical travel stops.
11) Completely weld the front bracket to the leaf. To weld,
detach the operator temporarily from the bracket to prevent
any waste material from damaging it (Fig. 8).
N.B
.:
1) Grease all pivots on brackets
2) If welding is not possible, the front and rear bracket
plates are also designed for fixing by screws and
screw anchors.
12) Fit the cover on the operator as shown in Fig. 9. Fit the cable
sheath (3, Fig. 11).
13) Repeat the above operations to install the second operator.
14) Make the electrical connections of the electronic control unit
following the instructions provided.
4.
START-UP
Fig. 7
Fig. 7
Fig. 9
4.1.
ANTI-CRUSHING SYSTEM ADJUSTMENT
The 400 automation is equipped with an anti-crushing system
which limits the torque applied by the operator when the gate
leaf encounters an obstacle during its movement.
When the obstacle is removed, the gate proceeds until the set
operation time is complete.
To adjust the intervention threshold of the anti-crushing system,
it is first necessary to remove the release unit (Fig. 10).
Fig. 9
By-pass
Fig. 5
5 mm
Fig. 8
Fig. 6
a
b