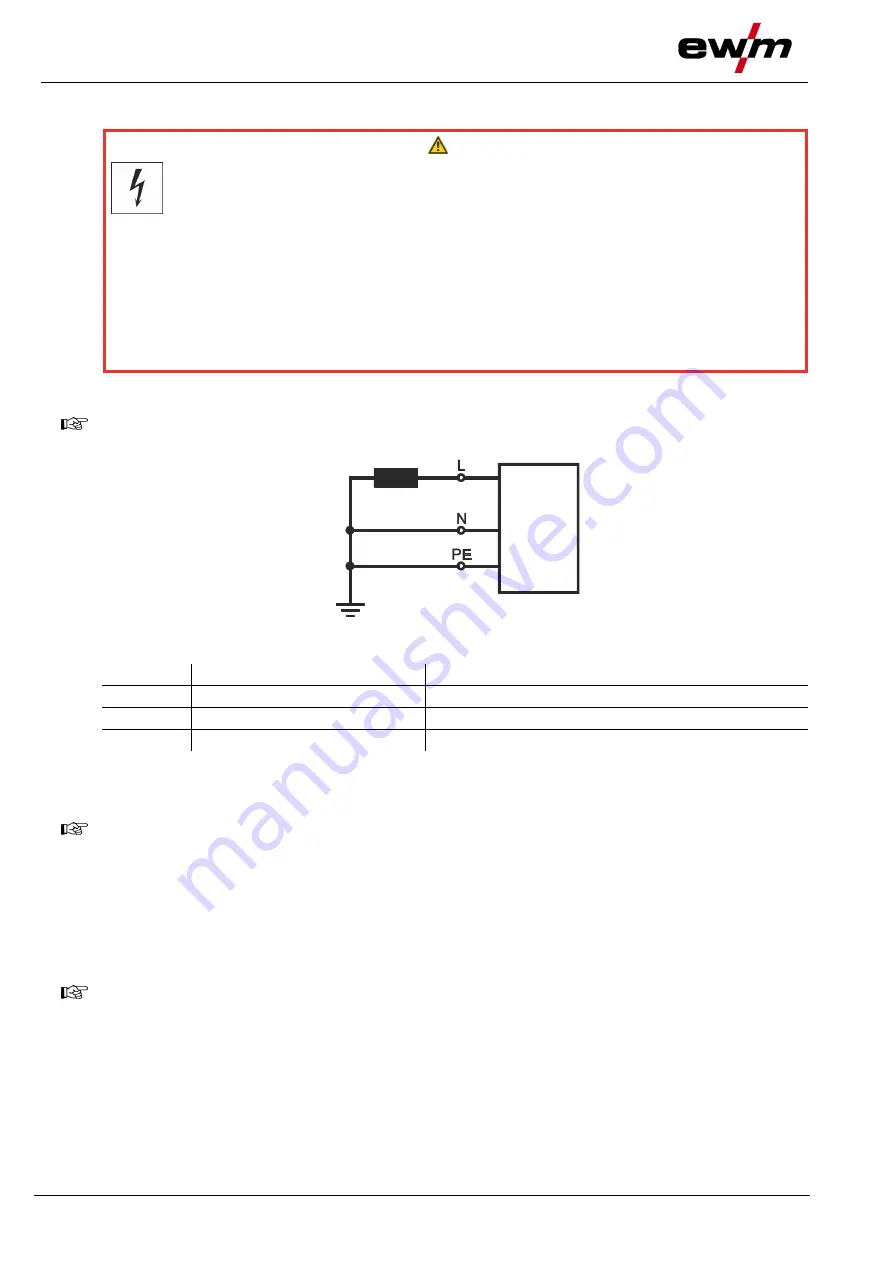
Design and function
Transport and installation
30
099-000237-EW501
25.04.2019
5.1.7
Mains connection
DANGER
Hazards caused by improper mains connection!
An improper mains connection can cause injuries or damage property!
• The connection (mains plug or cable), the repair or voltage adjustment of the device must
be carried out by a qualified electrician in accordance with the respective local laws or nati-
onal regulations!
• The mains voltage indicated on the rating plate must match the supply voltage.
• Only operate machine using a socket that has correctly fitted protective earth.
• Mains plug, socket and lead must be checked by a qualified electrician on a regular basis!
• When operating the generator, always ensure it is earthed as stipulated in the operating
instructions. The network created must be suitable for operating machines according to pro-
tection class I.
5.1.7.1 Mains configuration
The machine may only be connected to a one-phase system with two conductors and an earthed
neutral conductor.
Figure 5-6
Legend
Item
Designation
Colour code
L
Outer conductor
brown
N
Neutral conductor
blue
PE
Protective conductor
green-yellow
• Insert mains plug of the switched-off machine into the appropriate socket.
5.1.8
Welding torch cooling system
Insufficient frost protection in the welding torch coolant!
Depending on the ambient conditions, different liquids are used for cooling the welding
torch > see 5.1.8.1 chapter.
Coolants with frost protection (KF 37E or KF 23E) must be checked regularly to ensure that the
frost protection is adequate to prevent damage to the machine or the accessory components.
• The coolant must be checked for adequate frost protection with the TYP 1 frost protection
tester .
• Replace coolant as necessary if frost protection is inadequate!
Coolant mixtures!
Mixtures with other liquids or the use of unsuitable coolants result in material damage and ren-
ders the manufacturer's warranty void!
• Only use the coolant described in this manual (overview of coolants).
• Do not mix different coolants.
• When changing the coolant, the entire volume of liquid must be changed.
Dispose of the coolant in accordance with local regulations and the material safety data sheets.