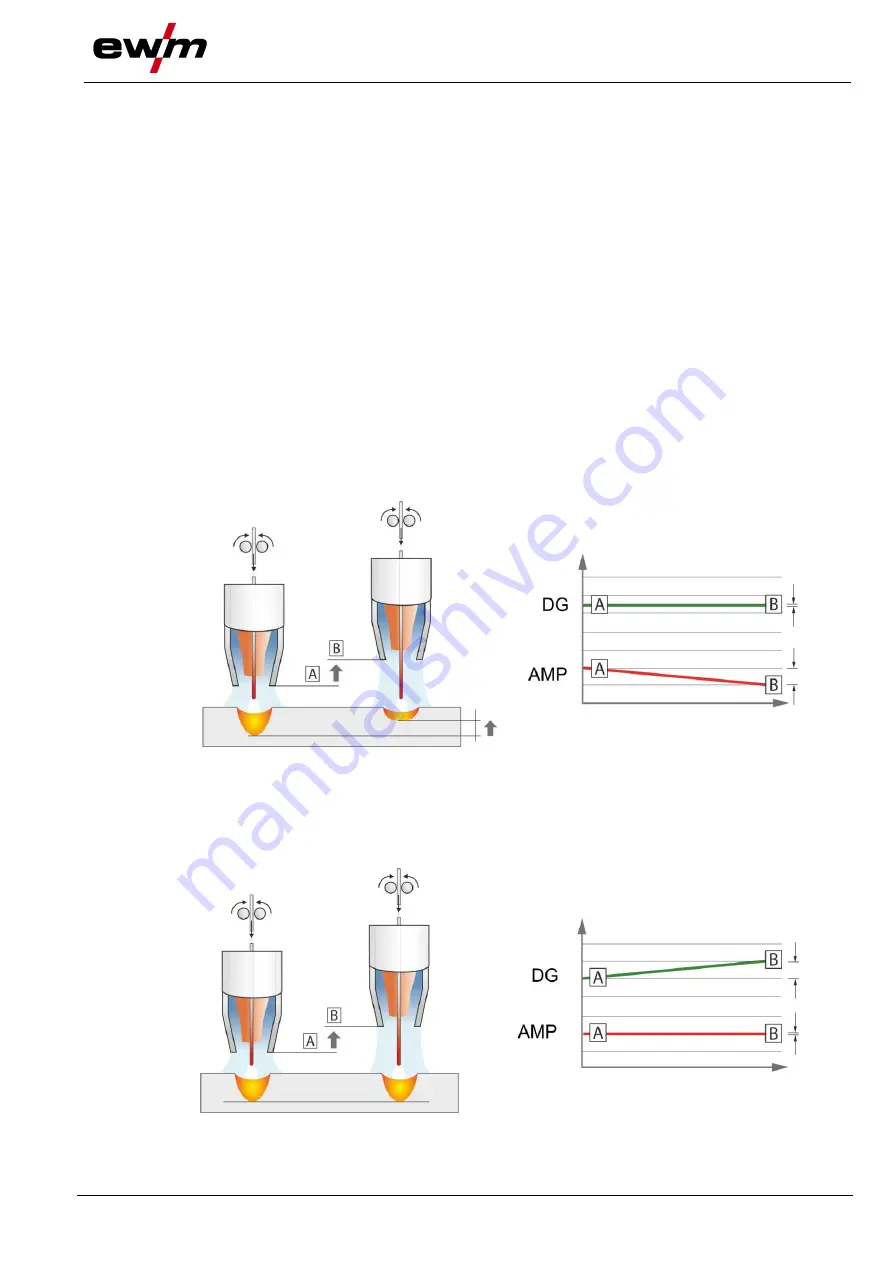
Welding procedure
MIG/MAG welding
099-00L105-EW501
07.06.2019
71
The basic requirement for optimum welding results is the application-specific equipment of the
wire feed system. For the acArc puls XQ welding process, the entire wire feed system of the
Titan XQ AC series is factory-equipped with components for aluminium welding consumables!
Recommended system components:
• Power source of type Titan XQ 400 AC puls D
• Wire feeder of type Drive XQ AC
• Welding torch series of type PM 551 W RD3 X Alu
Note the following equipment and setting features of the wire feed system:
• Wire feed rolls (set contact pressure depending on welding consumables and hose package
lengths)
• Central torch connection (use guide tube instead of capillary tube)
• Combined liner (PA liner with matching inner diameter for welding consumables)
• Use contact tips with forced contact
6.1.7 wiredArc
Welding process with active wire control for stable and uniform penetration characteristics and perfect arc
length stability, even in difficult applications and positional welding.
With a GMAW arc, the welding current (AMP) changes with the change of the stick-out. If, for instance,
the stick-out is extended, the welding current decreases at constant wire feed speed (DG). Thus, the heat
input into the workpiece (molten metal) decreases and the penetration reduces.
Figure 6-17
With the EWM wiredArc arc with wire control, the welding current (AMP) changes with the change of the
stick-out only slightly. The compensation of the welding current takes place with an active control of wire
feed speed (DG). If, for instance, the stick-out is extended, the wire feed speed will be increased. Due to
this, the welding current remains almost constant and thus the heat input into the workpiece remains al-
most constant. As a result, the penetration changes with the change of the stick-out only slightly.
Figure 6-18