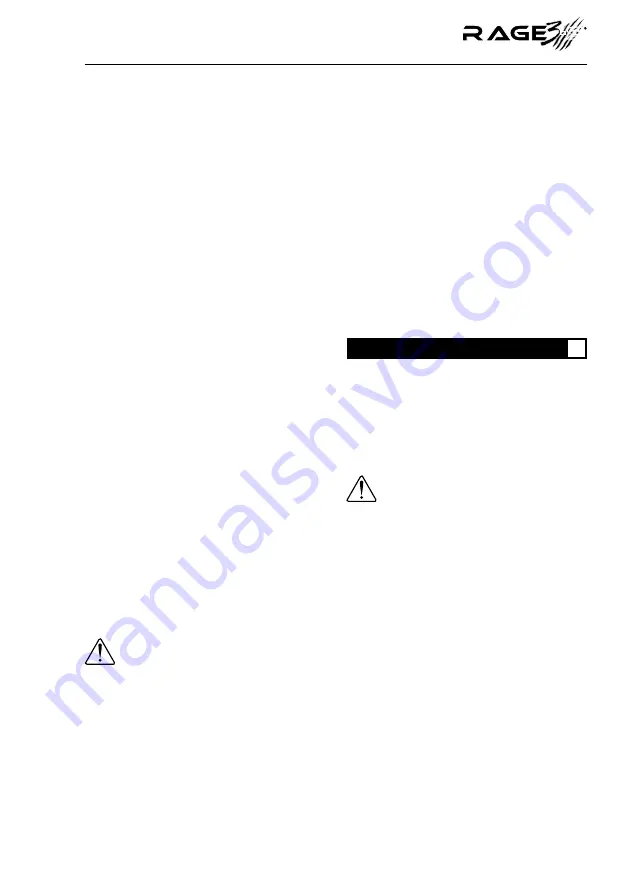
-
S
9
www.evolutionbuild.com
be adjusted to the required distance from the saw blade
for repetitive cutting operations etc. The repeat stop can
be fitted at either side of the table, but normally it will be
positioned to the RH side of the blade.
6. HOlD DOWn ClaMP (fig. 6)
1.
Hold down clamps can be fitted on either side of the saw
and are fully adjustable to suit the size of the workpiece.
2.
Do not operate the saw without clamping the workpiece.
3.
Make sure that the hold down clamp securing screws are
tightened.
4. WaRnInG:
Always check clamp position does not
interfere with any saw operation. Before switching on, lower
the saw head to ensure the clamp clears the guard and saw
head assembly.
7. fROnT ClaMP (OPTIOnal aCCessORY)
A Front Clamp can be fitted into the RH or LH sockets
incorporated into the front of the machines base.
1.
Fit the clamp to the socket which best suits the cutting
application.
2.
Adjust the clamp so that it securely holds the workpiece.
3.
Check that the clamp does not interfere with any saw
operation.
note:
Using a Hold Down Clamp and Front Clamp in
combination will usually provide the best solution to securing
the workpiece on the machine.
8. laseR GUIDe
This saw is equipped with a laser cutting guide. This allows
the operator to preview the path of the blade through the
workpiece. The ON/OFF switch for the Laser Guide is
positioned on top of the motor housing.
(fig 7)
Avoid direct eye contact, and do not use on material that
could reflect the laser beam.
WaRnInG:
Do not stare directly at the laser beam.
A hazard may exist if you deliberately stare into the beam,
please observe all safety rules as follows.
• The laser beam shall not be deliberately aimed at personnel
and shall be prevented from being directed towards the eyes
of a person.
• Always ensure the laser beam is only aimed at workpieces
without reflective surfaces, i.e. wood or rough coated
surfaces are acceptable.
• Do not change the laser module assembly with a different type.
• Repairs to the laser module must only be conducted by
Evolution Power Tools or their authorised agent.
9. DePTH sTOP (fig. 8)
Use of the depth stop allows the operator to cut slots in the
workpiece. The downward travel of the saw head can be
set so that the saw blade does not completely cut through
the workpiece.
note:
It is advisable that the depth of cut is checked using
a scrap piece of timber to ensure that the slot cut is correct.
By making a cut in the workpiece, and then repeating the
cut but with the workpiece slightly repositioned to the left or
right, it is possible to perform trenching cuts.
To use the depth stop feature follow these steps:
1. Loosen the wing nut.
2. Adjust the thumb knob to the required depth.
3. Once set to the desired depth, tighten the wing nut
against the retaining bracket to lock the depth stop and
ensure that there is no movement.
Caution:
The Mitre Saw should be inspected (particularly
for the correct functioning of the safety guards) before each
use. Do not connect the saw to the power supply until a
safety inspection has been carried out.
Ensure that the operator is adequately trained in the use,
adjustment and maintenance of the machine, before
connecting to the power supply and operating the saw.
WaRnInG:
To reduce the risk of injury, always
unplug the saw before changing or adjusting any of the
machines parts. Compare the direction of the rotation arrow
on the guard to the direction arrow on the blade. The blade
teeth should always point downward at the front of the saw.
Check the tightness of the arbor screw.
1. PRePaRInG TO MaKe a CUT
Caution:
NEVER pull the saw toward you during a cut. The
blade can suddenly climb up on top of the workpiece and
force itself toward you.
• Avoid awkward operations & hand positions where a sudden
slip could cause fingers or hand to move into the blade.
• Cut only one workpiece at a time.
• Clear everything except the workpiece and related support
devices away from the blade before turning the mitre saw on.
• Position the workpiece using clamp(s) to hold securely in
the required position.
OPeRaTInG InsTRUCTIOns
GB