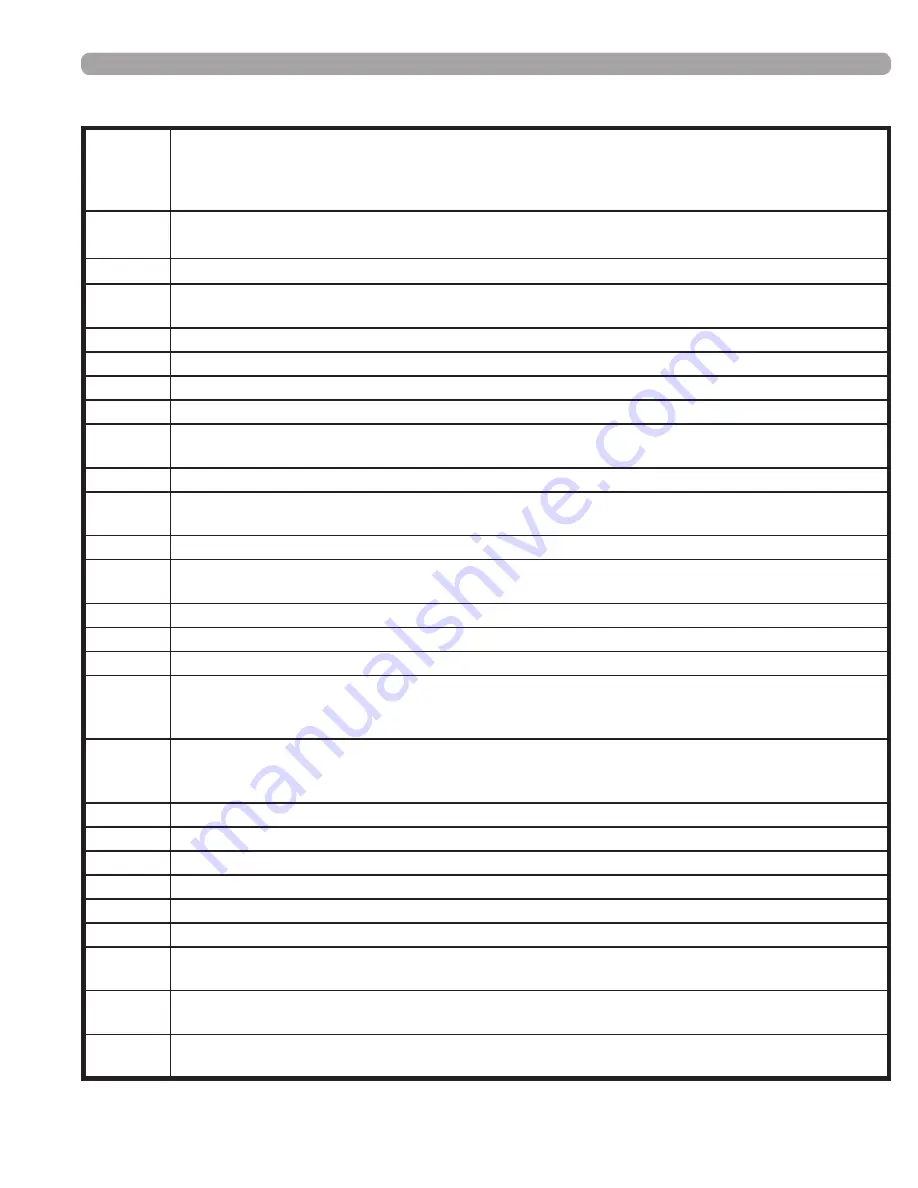
34000 Autry Street, Livonia, MI 48150 | 800.968.5530 | Fax 734.419.0209 | www.hamiltonengineering.com | LIT91127US REV 5/2018
Page 45
29.
First check that the pump is circulating like it should, and that there are no obstacles between
the appliance and the tank (or in any of the inlet/outlet piping). If the appliance is still making a
‘popping’ noise, the heat exchanger will need to be acid cleaned to remove accumulated scale.
DO NOT RUN THE APPLIANCE UNTIL THIS IS DONE!
30.
Replace the high-limit thermostat by unscrewing it from the brass nut; no draining is needed (do
not remove the brass nut)
31.
Go over the Fan RPM settings as outlined in Table 3-5 on page 17–18
35.
Replace. Or when bending, take care: bend near the burner plate, or there may be
risk of cracking
39.
Remove the connection and blow dry using a hair dryer or compressed air
40.
Plug in speed control wire, replace fan.
41.
Check the plugs and fit into one another correctly
42.
Check cables for possible damage or entrapment, and replace as required
44.
Check the seal of the heat exchanger on the flue gas casing, and replace as required. Fit a new
rotary lip seal. Lift the flue gas tube and inspect the Non-Return Valve from the top
45.
Check the piping and repair any leaks
46.
Disconnect leads from sensor and place an OHM meter across both terminals on
the sensor. Compare to Figure 7-1 on page 46. If it does not match, replace.
51.
Contact Hamilton Engineering for assistance at 800.968.5530
52.
Check the type of room thermostat and contact Hamilton Engineering for assistance at
800.968.5530
53.
Contact Hamilton Engineering for assistance at 800.968.5530
54.
Change the “wake-up” times of the clock thermostat
57.
Check the sensor on the storage tank or in the common piping
60.
It may occur that the 18-pin FMT 914 plug moved up one pin too far—this may cause a fault in
the communication between the wiring and the pins. Check both the left and the right-hand side
of the plugs to ensure they are placed correctly
61.
A defective gas valve usually has one of the two causes: the electric coils are
defective, or an internal defect to the gas valve. In either case, it is recommended
to replace the entire gas valve
63.
Contact Hamilton Engineering for assistance at 800.968.5530
66.
Re-adjust the gas valve per the instructions on pages 17-18
67.
Check the venting system completely for blockage
68.
Replace the pressure switch
71.
Check the wiring and correct
72.
Check the entire system including the pump for blockage and scaling
73.
For descaling, see the special instructions. Contact Hamilton Engineering
for assistance at 800.968.5530
74.
Remove leads on burner door high limit and check them for an open circuit; if it’s open, the back
wall high limit is bad
75.
Reset burner door high limit with button between the two leads; open combustion chamber and
check back side of burner door
SERVICING
(TABLE 7-6) TROUBLESHOOTING THE FAULT (CONTINUED)