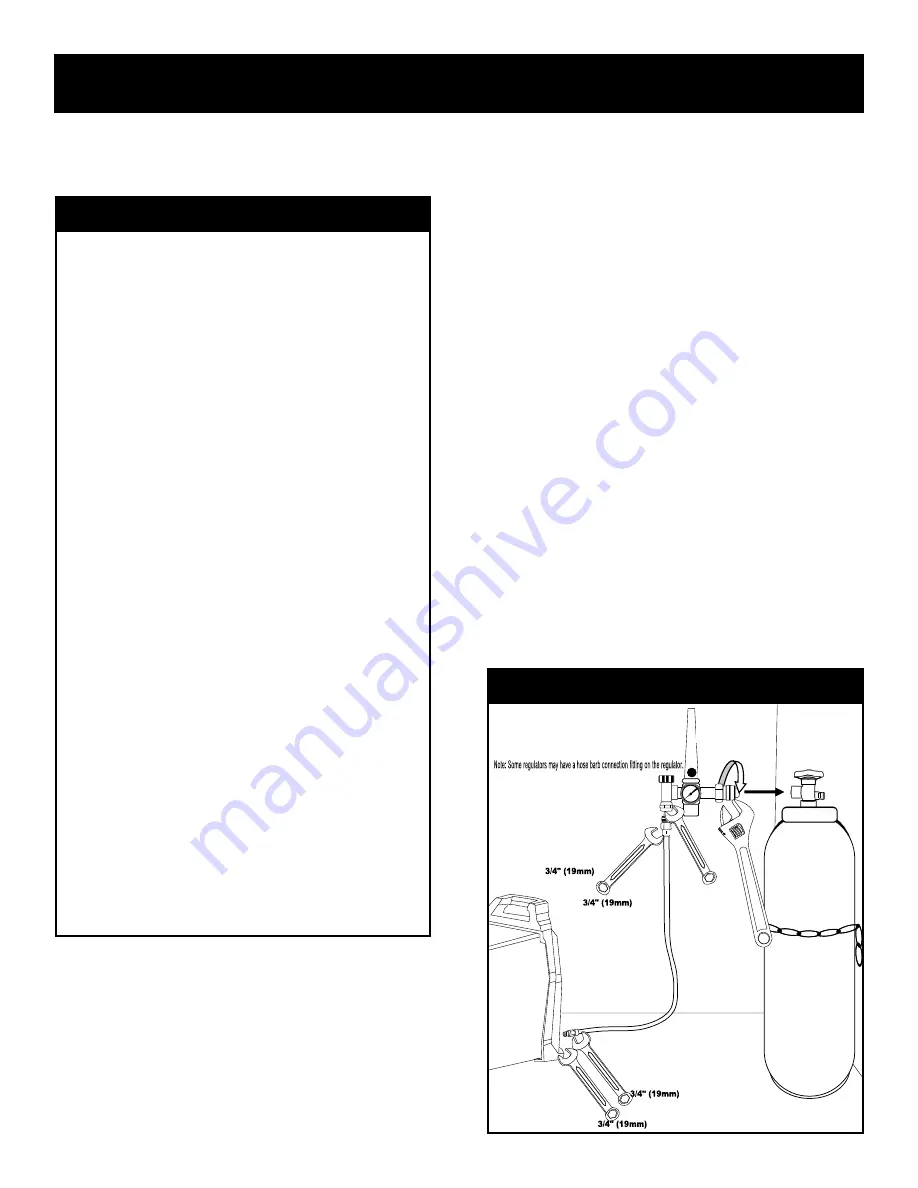
14
Setup Guide
Getting Started
CONNECT YOUR UNIT TO THE SHIELDING GAS.
Always wear safety glasses when changing a cylinder. Before in-
stalling any cylinder, stand to the site of the valve, away from the
discharge, and quickly open the cylinder to give it a quick blast. This
will dislodge any dirt or particles stuck in the valve or the connection
seat. This will help reduce the chance of dirt particles making its way
into the solenoid valve, causing sticking issues later on.
Connecting your cylinder will require a cylinder wrench(1
1/16”)
to
connect the regulator to the cylinder (North American Cylinders with
What Shielding Gas Should Be Used?
Selecting shielding gas for MIG is straightforward. For all metals,
whether using in AC or DC, use 100% Argon. Never use a gas mix
mixed with CO
2
. CO
2
will rapidly consume the tungsten and intro-
duce porosity into the weld even at low concentrations.
With that said, if you are welding at or near the maximum capability
of the unit, you may also wish to use an Argon/Helium mix. This
will increase the overall heat going into the weld. No more than
25% Helium mix should be used with this unit, or Arc starting effi-
ciency will be reduced (hard to start arc). Arc stability will also be
affected at higher percentages. Helium is expensive and the cost
versus benefit of adding it must be weighed carefully as a cylinder or
two of high percentage Helium may approach the cost difference of
upgrading to a larger unit! If a high Helium content is used, expect
some trade
-
offs. Arc starting may be improved slightly by readjust-
ing the point gap.
There are a few new gas mixes (blends) on the market with promise,
but as of publication they have not been thoroughly evaluated for
use with this welder. Exercise caution when using a new mixture
(often marketed with Nitrogen or Hydrogen) as the application is very
specific. Pure 100% Argon is the most economical and best for
nearly every application, and having multiple gases should not be a
concern for even the most advanced user.
BE AWARE:
It is increasingly common for users to get cylinders of
“
bad gas,
”
creating mysterious and difficult to identify issues
. An
Argon cylinder is the same type of cylinder as an Argon/CO
2
cylinder
used for MIG and sometimes times can get mixed in and relabeled
as pure argon. Another increasingly common issue is that a gas mix
cylinder gets refilled with Argon with residual Ar/CO
2
mix without
using proper purging techniques. Usually this occurs in
“
batches
”
and complete lots of cylinders can be affected. Sometimes swapping
with another cylinder from the same supplier will not correct the
problem. Also it has been found that a customer to specify
“
Argon
”
and receive a cylinder marked as Argon/CO
2
mix. Always check your
cylinder label below the cap area for proper labeling before accept-
ing the cylinder.
a 580 CGA valve). If you do not have a cylinder wrench, an adjusta-
ble type wrench will work, but make sure it is properly adjusted to
prevent rounding of the fitting shoulders. Do not use pliers, or a
serrated jaw wrench such as a pipe wrench or basin wrench to tight-
en the fitting. The design of the fitting means that no thread sealing
tape or compound needs to be used.
Connect the regulator tubing to the regulator. The regulator may
have either a hose barb connection, or a threaded connection. If the
regulator supplied has a hose barb, make sure the hose barb fitting is
tight on the regulator. Tighten with a
3/4”
(19mm) wrench. If it is a
threaded connection, use two
3/4”
(19mm) wrenches to hold both
the regulator and the tubing connection at the same time. Hold
counter pressure on the regulator connector while tightening the
hose fitting to prevent damage to the regulator and to ensure maxi-
mum sealing. After connecting the tubing to the regulator, connect
the other end of the tubing to the
5/8”
CGA fitting on the unit. Hold
the fitting on the unit with one
3/4”
(19mm) wrench firmly while
tightening the hose fitting with another
3/4”(19
mm) wrench. Im-
portant! Do not use thread tape or pipe sealant on any cylinder, regu-
lator or unit connection. The residue and debris may get into the gas
solenoid and cause operational issues.
CAUTION!
Do not tighten the rear unit connection without holding
the female fitting on the unit with a wrench, or damage may occur to
the bezel as the fitting may turn in the plastic housing while the hose
fitting is being turned..
Connect Regulator To Cylinder And Unit.
Содержание PowerTIG 200 EXT
Страница 38: ...38...