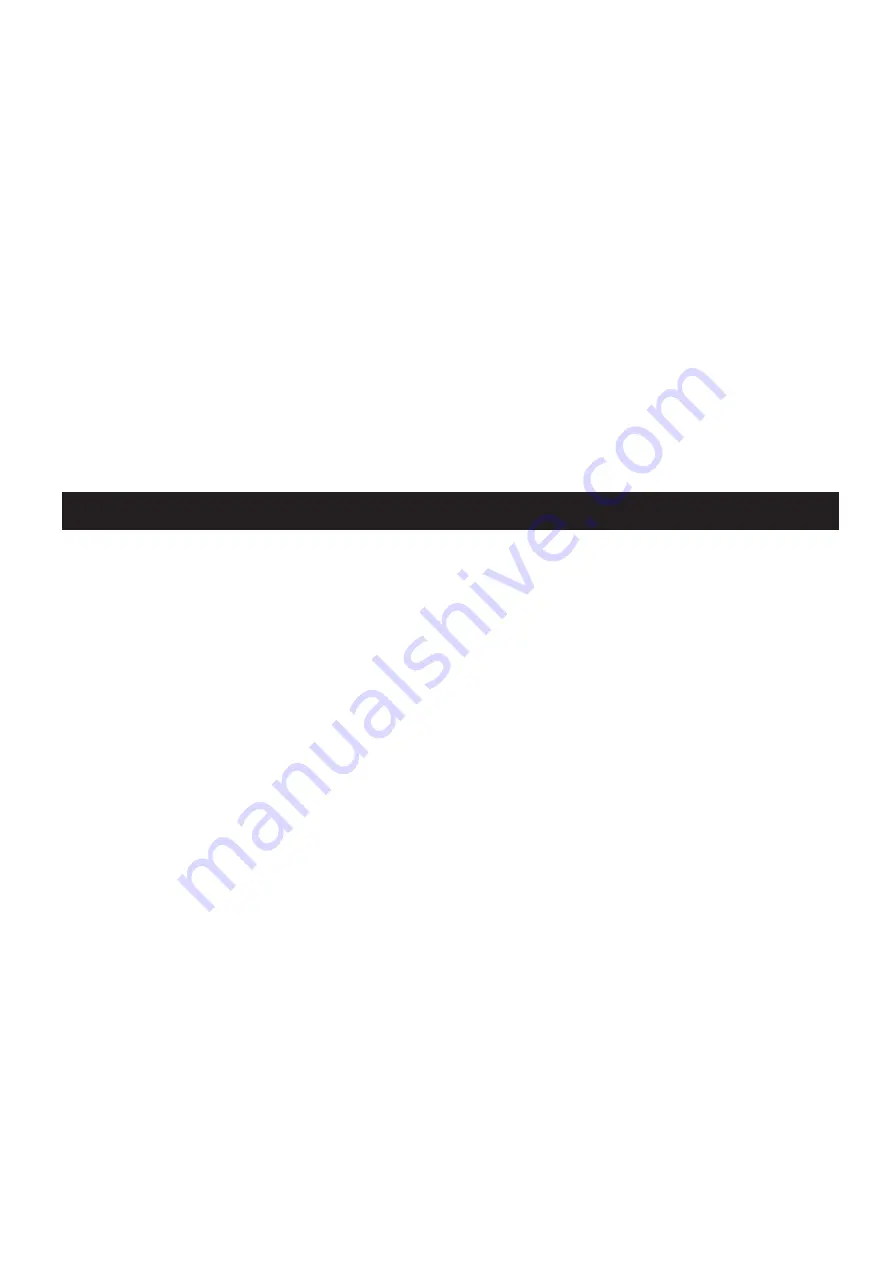
19
system lay-up, if applicable. If excessive microbiological contamination is detected, a more aggressive
mechanical cleaning and/or water treatment program should be undertaken.
It is important that all internal surfaces, particularly the basin, be kept clean of accumulated dirt and
sludge. Additionally, drift eliminators should be inspected and maintained in good operating condition.
Gray Water and Reclaimed Water
The use of water reclaimed from another process as a source of makeup water for evaporative
cooling equipment can be considered as long as the resultant recirculating water chemistry
conforms to the parameters noted in Table 4. It should be noted that using water reclaimed from
other processes may increase the potential of corrosion, microbiological fouling, or scale formation.
Gray water or reclaimed water should be avoided unless all of the associated risks are understood
and documented as part of the site specific treatment plan.
Air Contamination
Evaporative cooling equipment draws in air as part of normal operation and can scrub particulates
out of the air. Do not locate the unit next to smokestacks, discharge ducts, vents, flue gas
exhausts, etc. because the unit will draw in these fumes which may lead to accelerated corrosion
or deposition potential within the unit. Additionally, it is important to locate the unit away from
the building’s fresh air intakes to prevent any drift, biological activity, or other unit discharge from
entering the building’s air system.
Stainless Steel
Stainless steel is the most cost effective material of construction available to extend the life of an
evaporative cooling unit.
The stainless steel sheet material utilized by EVAPCO is Type 304L and Type 316L with a
No. 2B unpolished finish. Type 304L stainless steel is a basic chromium-nickel austenitic stainless
steel and is suitable for a wide range of applications. It is readily available throughout the world
and is easy to form during the fabrication process. Type 316L stainless steel offers more corrosion
resistance than Type 304L due to the addition of molybdenum and a higher nickel content, which
provides greater resistance to pitting and crevice corrosion in the presence of chlorides. As a
result, Type 316L stainless steel is desirable in heavy industrial, marine environments and where
make up water quality requires it.
Stainless steel provides its superior corrosion resistance by developing a surface film of
chromium oxide during the manufacturing process. In order to ensure maximum corrosion
protection, stainless steel must be kept clean and have an adequate supply of oxygen to combine
with the chromium in the stainless steel to form “chromium-oxide”, a protective passivation layer.
The protective layer of chromium-oxide develops during routine exposure to the oxygen content
in the atmosphere. This occurs during the milling process and continuously as the stainless is
formed and shaped for its final use.
Содержание AT 110-112
Страница 39: ...39 ...
Страница 40: ... 2012 EVAPCO Europe Bulletin 113 E 1216 ...