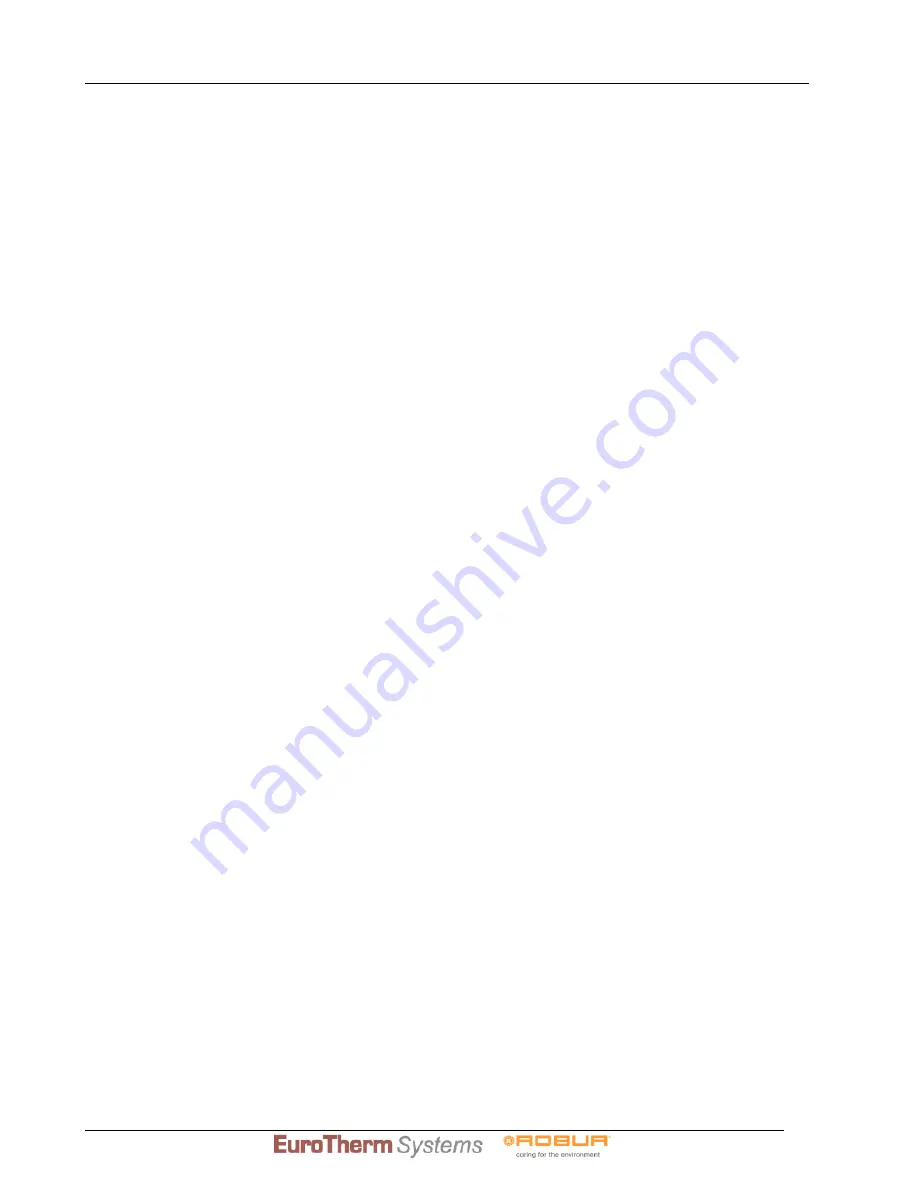
5001/5002 – 8001/8002 Installation Instructions and Owner’s Manual
16
Ed. 06/2006
GAS SUPPLY
Check all local codes for requirements,
especially for the size and type of gas supply
line required. On Natural gas lines less than 15”
(380 mm) long, use 1/2” tube; on longer runs,
use 3/4” iron tube or equal. On LP gas lines
please consult LP gas supplier.
INSTALLING A NEW MAIN GAS COCK
Each appliance should have its own manual gas
cock. A manual main gas cock should be
located in the vicinity of the unit. Where none
exists, or where its size or location is not
adequate, contact your local authorized installer
for installation or relocation.
Compounds used on threaded joints of gas
piping shall be resistant to the action of L.P. gas.
The gas lines must be checked for leaks by the
installer. This should be done with a soap
solution watching for bubbles on all exposed
connections, and if unexposed, a pressure test
should be made.
Never use an exposed flame to check for
leaks. Appliance must be disconnected from
piping at inlet of control valve and pipe
capped or plugged for pressure test. Never
pressure test with appliance connected;
control valve will sustain damage!
A gas valve and ground joint union should be
installed in the gas line upstream the gas control
to aid in servicing. It is required by the National
Fuel Gas Code that a drip line be installed near
the gas inlet. This should consist of a vertical
length of pipe tee connected into the gas line
that is capped on the bottom in which
condensation and foreign particles may collect.
The use of the following gas connectors is
recommended:
– ANSI Z21.24 Appliance Connectors of
Corrugated Metal Tubing and Fittings., CGA
6.10.
– ANSI Z21.45 Assembled Flexible Appliance
Connectors
of
Other
Than
All–Metal
Construction.
The above connectors may be used if
acceptable by the authorities having jurisdiction.
PRESSURE TESTING OF THE GAS SUPPLY
SYSTEM
1. To check the inlet pressure to the gas
valve, a plugged tapping, accessible for
test gauge connection, is provided on the
gas valve (see A in Figure 11, page 17).
2. The appliance and its individual shutoff
valve must be disconnected from the gas
supply piping system during any pressure
testing of that system at test pressures in
excess of 1/2 psig (3.5 kPa).
3. The appliance must be isolated from the
gas supply piping system by closing its
individual manual shutoff valve during any
pressure testing of the gas supply piping
system at test pressures equal to or less
than 1/2 psig (3.5 kPa).
Attention
: If one of the above procedures
results in pressures in excess of 1/2 psig (14”
w.c.) (3.5 kPa) on the appliance gas valve, it will
result in a hazardous condition.
HIGH ALTITUDES (U.S. ONLY)
For altitudes/elevations above 2,000 feet (610
m), ratings should be reduced at the rate of 4
percent for each 1,000 feet (305 m) above sea
level by reducing the manifold pressure at 8%
rate on the gas supply.
HIGH ALTITUDES (CANADA ONLY)
The appliance is tested according to CGA 2.17
M91 for installation between 0 and 4500 ft. (0
and 1370 m) altitude without changes.
FIRST FIRING OF THE FURNACE
Light up the furnace following the instructions
given
in
section
3
“OPERATING
INSTRUCTIONS” on page 21.
The first lighting can be difficult because of the
air trapped in the gas lines.
During initial firing of the furnace, residual
manufacturing grease will bake out and smoke
will occur which is not a health danger. To
prevent nuisance and operation of fire alarms,
ventilate the room for the first two hours of
operation.
CHECKING THE GAS INLET PRESSURE
The gas inlet pressure can be measured by
connecting a test gauge to the connection
provided on the gas valve (see A in Figure 11,
page 17).