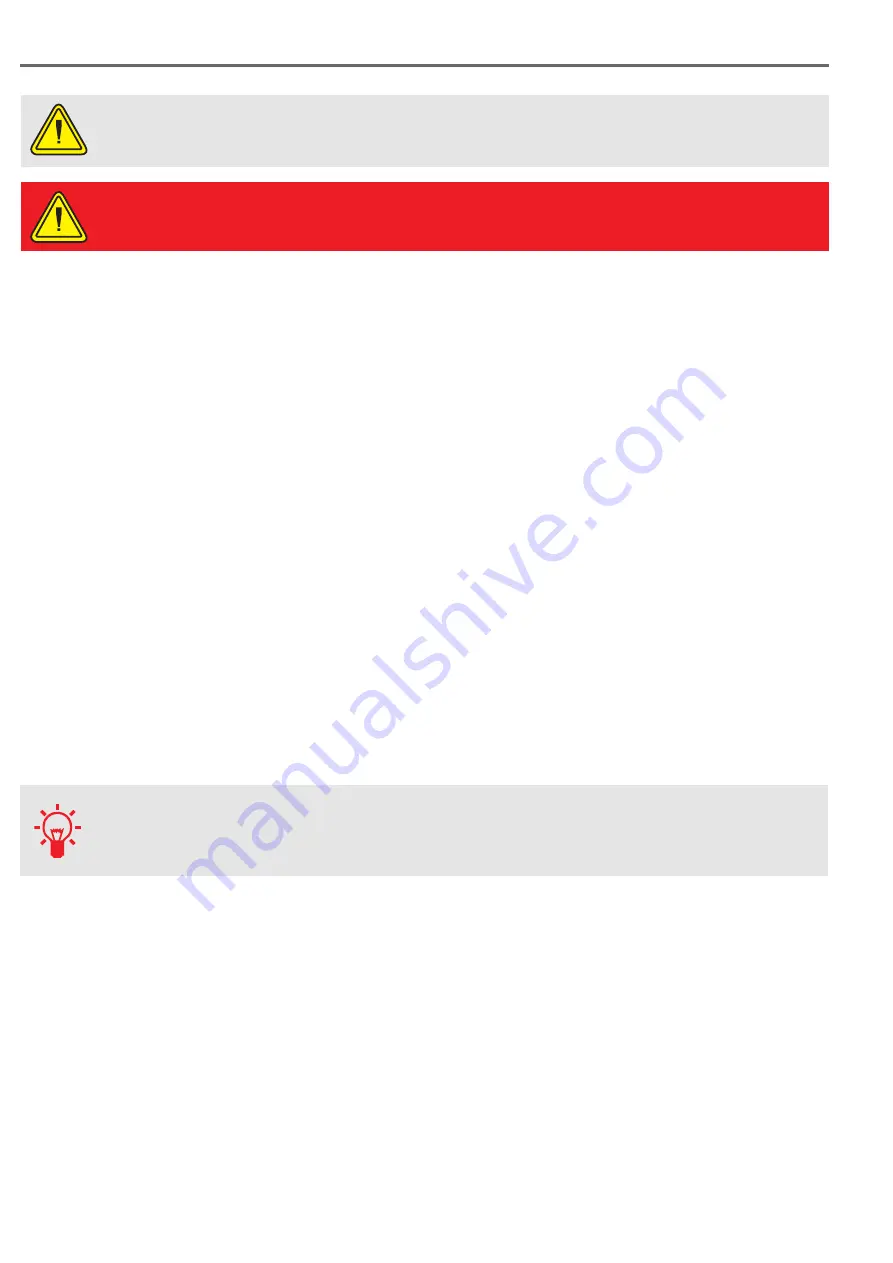
User manual - X-PRO D200
202203-577-ENG
P20
7. MAINTENANCE
After the first 50 hours of operation:
- Replace the return filter cartridge on the hydraulic tank.
Every 50 hours:
- Check cooling radiator fins for cleanliness.
- Check the hydraulic oil level on the level indicator on the tank and refill with HV46 hydraulic oil if necessary.
- Grease the hopper bearing and the jockey wheel.
- Check the safety devices of the vibrating strainer.
- Check the operation of the emergency stop located on the fixed cover.
Every 125 hours:
- Check the drawbar axle mountings.
- Check the condition of the axle and tyres.
- Check the condition of the clamping screws of the swivel drawbar as well as the pins.
- Check the attachment and proper functioning of the coupling system.
Every 500 hours:
- Replace the return filter cartridge on the hydraulic tank.
Every 1000 hours and/or every year:
- Drain the hydraulic tank, clean the suction strainer and replace the filter cartridge.
Verifications concerning the diesel engine and hydraulic part must always be carried out on
a cold machine.
For any work on the diesel engine, refer to the maintenance manual supplied with the
machine.
In order to guarantee a long-lasting operation of the machine, we invite you to contact your
dealer for any maintenance intervention. He will carefully carry out the operations and check
the various points we recommend.
Содержание 40095
Страница 25: ...202203 577 ENG User manual X PRO D200 P25 10 ELECTRICAL SCHEMES...
Страница 26: ...User manual X PRO D200 202203 577 ENG P26 10 ELECTRICAL SCHEMES continued...
Страница 27: ...202203 577 ENG User manual X PRO D200 P27 11 HYDRAULIC SCHEMES...
Страница 28: ...User manual X PRO D200 202203 577 ENG P28 11 HYDRAULIC SCHEMES continued...
Страница 29: ...202203 577 ENG User manual X PRO D200 P29...
Страница 31: ...202203 577 ENG User manual X PRO D200 P31...
Страница 34: ...User manual X PRO D200 202203 577 ENG P34...