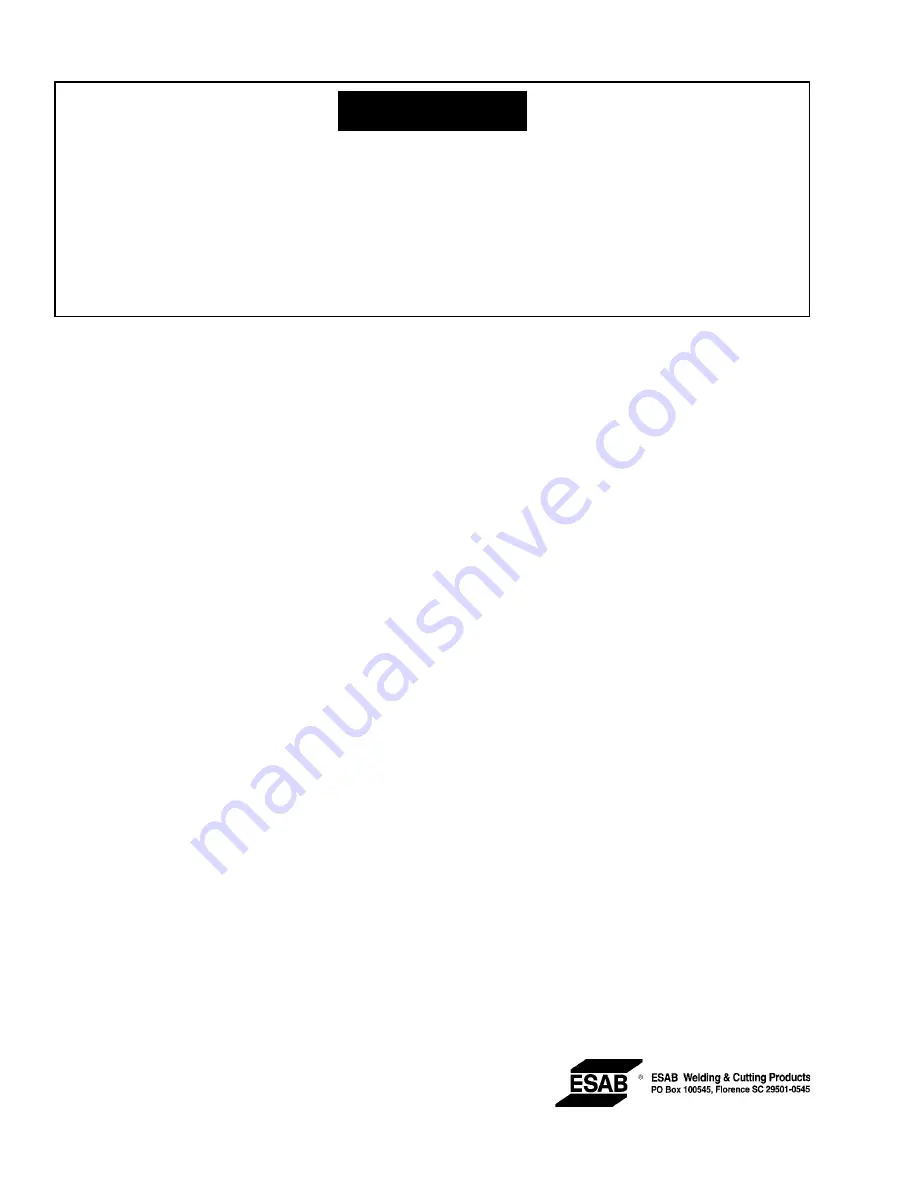
1. Close the cylinder valve.
2. Release gas from the regulator by opening valve
downstream.
3. When pressure gauge reads zero, the regulator may
be removed from the cylinder.
INLET FILTER MAINTENANCE
Each regulator is equipped with a porous metal inlet filter,
P/N 71Z33, pressed into the regulator inlet nipple. No
regulator should be connected to a cylinder or station
valve unless it contains this filter. You can replace the
filter if you have reason to do so. To remove a filter, insert
a No. 1 "EZY-OUT" or a No. 6 wood screw (about 2.00" - 51
mm long) into the filter and pull it out. Carefully press
the new filter into the nipple with a 0.25" (6.4 mm) round
metal rod.
REPAIR SERVICE
If gas is escaping through the safety release device, or if
any leakage was noted, the regulator should be returned
to your distributor or to ESAB Remanufacturing Center,
411 S. Ebenezer Road, Florence, SC 29501.
If you have your own properly equipped and staffed repair
facility, repair parts information for this regulator (Form
F14-239) is available on request to your distributor.
NOTE:
Safety release device equipped on these regula-
tors is designed for regulator protection; not for
hose or equipment downstream. If gas escapes
through the safety release device, immediately
close cylinder valve and then remove regulator
from service for repair.
F14-237
04 / 2007
Printed in U.S.A.
TO CONNECT:
1. Open the cylinder valve slightly for an instant, and
then close it. This is known as cracking the valve. This
blows away and dirt or dust which may have accumu-
lated in the valve outlet. Be sure to keep your face
away from the valve outlet to protect your eyes.
2. Attach the torch hose to the regulator outlet ("B"- size
inert gas female connection) and tighten the con-
nection snugly with a wrench. (A shutoff valve, such
as the OXWELD V-30 Argon-Water Shutoff Valve, P/N
16X21, may be connected between the regulator and
torch if desired.
3. Open the cylinder valve slowly a fraction of a turn.
When the cylinder pressure gauge pointer stops mov-
ing, open the valve fully. Never stand directly in front
of or behind the regulator when opening the cylinder
valve. Always stand to one side.
IMPORTANT:
Before starting operation, test all con-
nections with a Leak Test Solution
such as P/N 998771. Correct any leaks
before starting work. Testing should be
performed after torch or other gas-using
device has been properly connected,
with valve(s) downstream of regulator
closed.
Also, check all joints on the regulator, including vent holes
in the cap, for leakage. If leakage is noted, the regulator
should be removed from service and sent out for repair.
TO STOP FLOW
If work is to be stopped for a half-hour or more, or the
regulator is to be removed from the cylinder, shut down
the regulator as follows:
INERT GAS OR CARBON DIOXIDE CAN CAUSE SUFFOCATION IN CONFINED SPACES.
ALWAYS WORK IN WELL VENTILATED AREA.
PREVENT LEAKS.
DO NOT CHANGE CGA INLET CONNECTION FROM NUMBER STAMPED ON REGULATOR BODY.
FOLLOW OPERATING INSTRUCTIONS ON THIS SHEET.
THIS REGULATOR MUST BE INSTALLED, OPERATED AND MAINTAINED ONLY BY TRAINED SERVICEMEN.
FOR COMPLETE SAFETY INFORMATION ON WELDING AND CUTTING EQUIPMENT, READ FORM 2035 (OXY-
FUEL GAS) AND 52-529 (ARC WELDING). FOR SAFETY INFORMATION ON GASES, SEE YOUR SUPPLIER.
•
•
•
•
•
•
WARNING