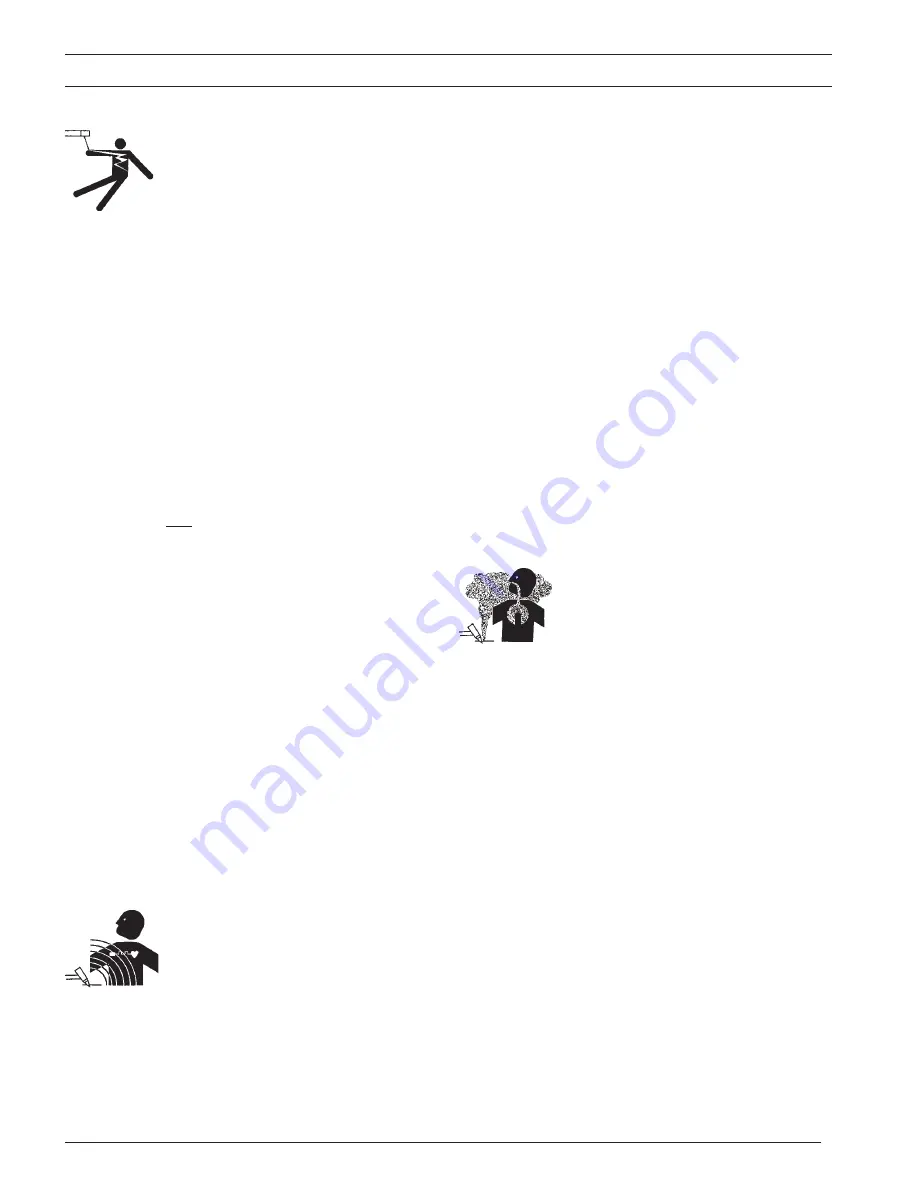
6
1. Be sure the Plasma Console frame (chassis) is con-
nected to the ground system of the input power.
2. Connect the work piece to a good electrical ground.
3. Connect the work cable to the work piece. A poor
or missing connection can expose you or others
to a fatal shock.
4. Use well-maintained equipment. Replace worn or
damaged cables.
5. Keep everything dry, including clothing, work
area, cables, torch/electrode holder, and Plasma
Console.
6. Make sure that all parts of your body are insulated
from work and from ground.
7. Do not stand directly on metal or the earth while
working in tight quarters or a damp area; stand
on dry boards or an insulating platform and wear
rubber-soled shoes.
8. Put on dry, hole-free gloves before turning on the
power.
9. Turn off the power before removing your gloves.
10. Refer to ANSI/ASC Standard Z49.1 (listed on
next page) for specific grounding recommenda-
tions. Do not mistake the work lead for a ground
cable.
electric anD magnetic fielDs — may be danger-
ous. electric current flowing through any conductor
causes localized electric and magnetic fields (emf).
Welding and cutting current creates emf around
welding cables and welding machines. therefore:
1. Welders having pacemakers should
consult their physician before weld-
ing. EMF may interfere with some
pacemakers.
2. Exposure to EMF may have other health effects
which are unknown.
3. Welders should use the following procedures to
minimize exposure to EMF:
A. Route the electrode and work cables together.
Secure them with tape when possible.
B. Never coil the torch or work cable around your
body.
C. Do not place your body between the torch and
work cables. Route cables on the same side of
your body.
D. Connect the work cable to the work piece as close
as possible to the area being welded.
E. Keep welding Plasma Console and cables as far
away from your body as possible.
fumes anD gases -- fumes and
gases, can cause discomfort or harm,
particularly in confined spaces. Do
not breathe fumes and gases. shield-
ing gases can cause asphyxiation.
therefore:
1. Always provide adequate ventilation in the work area
by natural or mechanical means. Do not weld, cut, or
gouge on materials such as galvanized steel, stain-
less steel, copper, zinc, lead, beryllium, or cadmium
unless positive mechanical ventilation is provided.
Do not breathe fumes from these materials.
2. Do not operate near degreasing and spraying opera-
tions. The heat or arc rays can react with chlorinated
hydrocarbon vapors to form phosgene, a highly
toxic gas, and other irritant gases.
3. If you develop momentary eye, nose, or throat ir-
ritation while operating, this is an indication that
ventilation is not adequate. Stop work and take
necessary steps to improve ventilation in the work
area. Do not continue to operate if physical discom-
fort persists.
4. Refer to ANSI/ASC Standard Z49.1 (see listing below)
for specific ventilation recommendations.
electrical shock -- contact with
live electrical parts and ground can
cause severe injury or death. Do not
use ac welding current in damp areas,
if movement is confined, or if there is
danger of falling.
section 1
safetY
Содержание Heliarc 281iAC/DC
Страница 13: ...13 SECTION 4 ASSEMBLY SECTION 4 ASSEMBLY TROLLEY ASSEMBLY fig 4 1 15...
Страница 14: ...14 SECTION 4 ASSEMBLY TROLLEY ASSEMBLY fig 4 2 15b SECTION 4 ASSEMBLY...
Страница 15: ...15 SECTION 4 ASSEMBLY SECTION 4 ASSEMBLY POWER SOURCE TO TROLLEY ASSEMBLY fig 4 3 15c...
Страница 16: ...16 SECTION 4 ASSEMBLY POWER SOURCE TO TROLLEY ASSEMBLY fig 4 4 View From A 15d SECTION 4 ASSEMBLY...
Страница 47: ...47 SECTION 7 warranty...