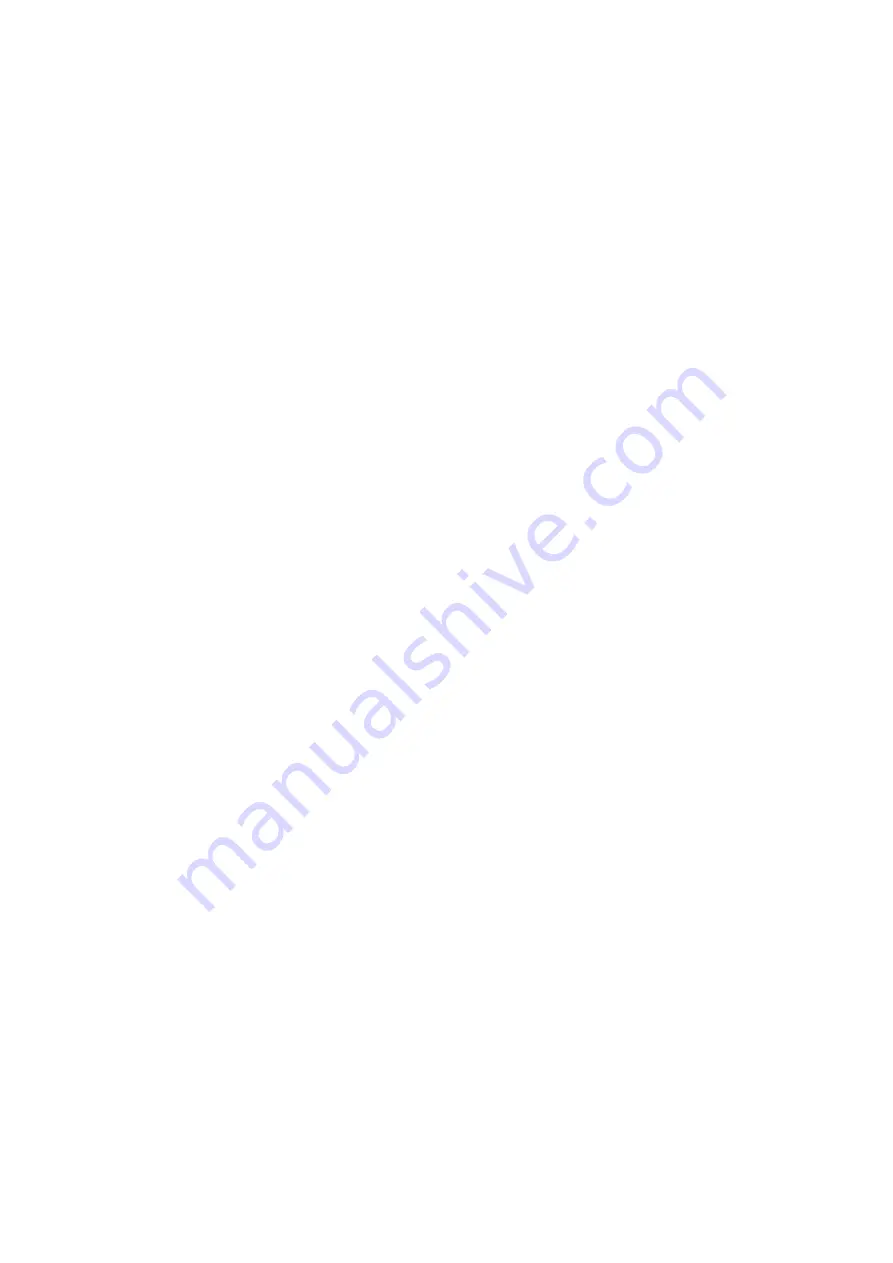
- 20 -
4
PROTECTION AGAINST EXCESSIVE OUTPUT VOLTAGE
The DTG405 is designed for welding operations where higher-than-normal electric hazards exist.
Usually, only no-load DC voltages of about 90 V are applied to the output of the DTG405. The
maximum permitted no-load DC voltage as per the relevant standard is 113 V.
No-load AC voltages cannot occur at the output unless a fault has occurred. When the weld cur-
rent is interrupted, the unit promptly changes to the positive and attempts to initiate positive start-
ing.
This complies with the hazard-minimisation features described in regulation EN60974-1.
Irrespective of this, the electronics module A1 comprises an additional safety circuit (see section
A1-6). Two separate cables convey the output voltages to the connectors X9-1 and X9-3. The
safety circuit is activated at zero current and monitors whether an excessive positive, excessive
negative, or excessive AC voltage is applied to the output. If any of these cases occurs, a memory
signal is set. It disconnects the complete inverter supply.
As a result, there is no supply to A1 and A8 and conductive control of the primary switch and the
inverter power sections is disabled. This interrupts energy flow from the mains to the outputs of
the power supply.
This status can only be cancelled by turning the unit OFF and back ON again.
This complies with the stipulation for "Safe Failure" described in regulation EN60974-1.
5
PATH OF THE START-UP SIGNALS
The Torch button signal passes through X4/5,6 to the module A6, where it is transferred from X4
on A6 to X7 of module A2-1 via a potential-isolated relay.
In addition, the start-up signal is generated independently on A2-1 in MMA mode. The start-up
signal, together with all necessary references, passes from X4 on A2-1 to X1 on A8.
On A8, the start signal is further processed, and a PWM clock signal is generated as a function of
all current and voltage references and actual values. The clock signal passes from X2 on A8 to
X7 on A1. On A1, the cycle signal is potential-isolated and then amplified in the MOSFET driver
stages. The control signals for the MOSFETs pass from X11 and X12 on A1 to X2 on A4, A5, A11,
A12.
The MOSFETs on A4, A5, A11, A12 control the power transformer T3 as a function of the PWM
clock signal.
In addition, signals for the AC converter are generated on A8. The driver signals generated for the
AC converter are transferred from X6 and X7 on A8 to X1 on A9, A13 and A10, A14.
The MOSFETs on A9, A13 and AP013 control the polarity of the machine's output voltage as a
function of the control signal from A8.
Содержание Aristotig 405 AC/DC
Страница 1: ...0458 165 002 9910 DTG 405 Aristotig 405 AC DC Welding rectifier Service manual...
Страница 9: ...9 NOTES...
Страница 10: ...10 CONNECTION DIAGRAM DTG 405...
Страница 11: ...11...
Страница 15: ...15 NOTES...
Страница 16: ...16 BLOCK DIAGRAM DTG 405 405a pcx...
Страница 17: ...17 Warning Some parts of this circuit are connected to mains voltage potential 405b pcx...
Страница 27: ...27 A2 COMPONENT POSITIONS a2 1b pcx a2 2b pcx...
Страница 30: ...30 A4 A11 COMPONENT POSITIONS Warning The circuit and its parts are connected to mains voltage potential...
Страница 40: ...40 A9 A13 COMPONENT POSITIONS A10 A14 COMPONENT POSITIONS...
Страница 57: ...57 209 201 212 203 204 205 206 207 208 D04 0301 1 214 215 216 218 217 219 220 110 221 222 213 202...
Страница 62: ...62 8 WAVEFORM AC2 SMOOTH WAVE ac2 pcx...
Страница 67: ...67 LOAD CHARACTERISTICS NOTES 0 10 20 30 40 50 60 70 80 90 0 50 100 150 200 250 300 350 400 A V TIG MMA DTG 405...
Страница 81: ...81 NOTES...
Страница 86: ...86 D04 0304 1 D04 0305 0 501 502 503 502 502 504 505 506 507 508 509 510 511 512 513 515 516 505 517...
Страница 91: ...page...