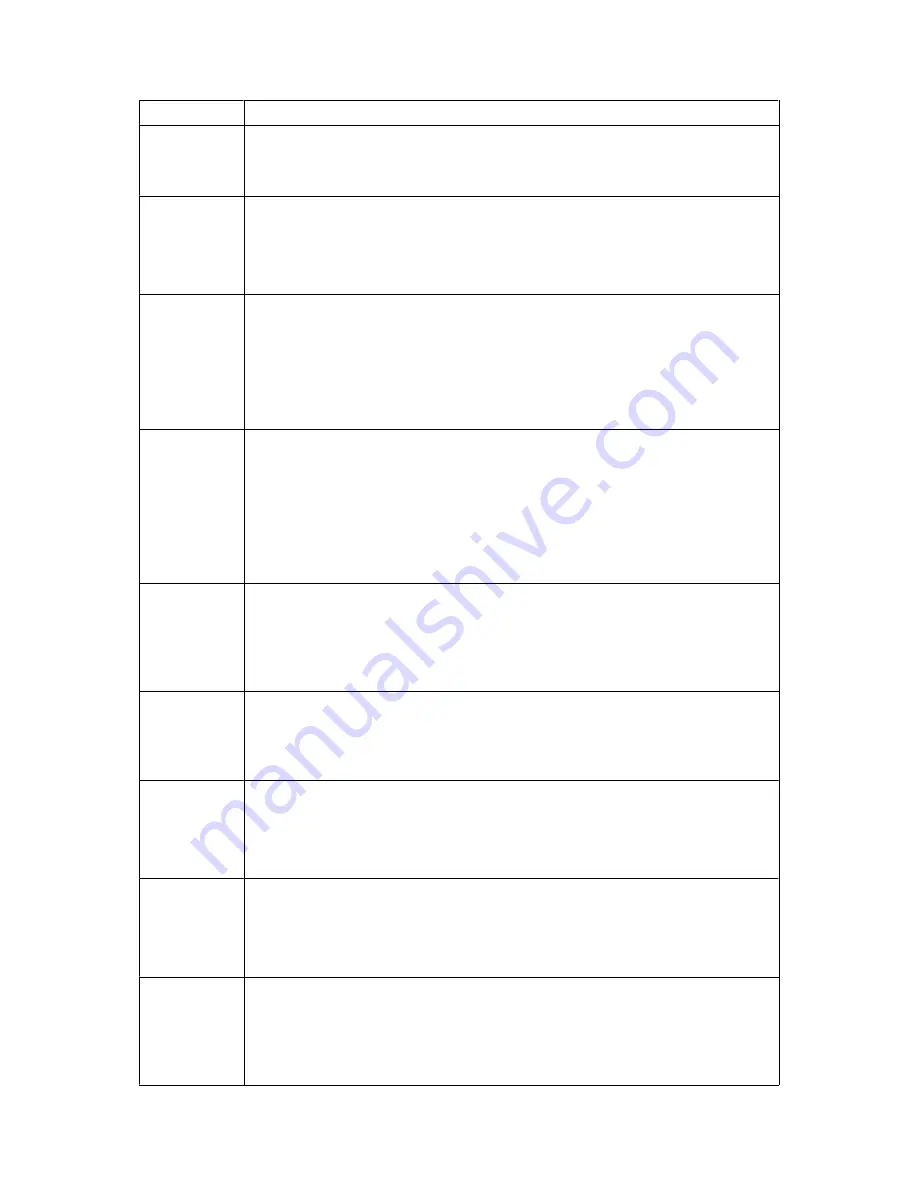
10 FAULT CODES
0459 287 474
- 31 -
© ESAB AB 2016
Fault code
Description
10
+24V power supply
The voltage is too high or too low.
Action:
Send for a service technician.
11
Wire feed speed
The wire feed speed differs from the set value.
Wire feed stops if this fault occurs.
Action:
Send for a service technician.
12
Communication error (warning)
The load on the system CAN bus is temporarily too high.
The power unit or wire feed unit may have lost contact with the control panel.
Action:
Check the equipment to ensure that only one wire feed unit or
remote control unit is connected. If the fault persists, send for a service
technician.
14
Communication error
The system's CAN bus has temporarily ceased to work due to excessive
load.
The current welding process is stopped.
Action:
Check the equipment to ensure that only one wire feed unit or
remote control unit is connected. Turn off the mains power supply to reset
the unit. If the fault persists, send for a service technician.
15
Messages lost
The microprocessor is unable to process incoming messages sufficiently
quickly, with the result that information has been lost.
Action:
Turn off the mains power supply to reset the unit. If the fault persists,
send for a service technician.
16
High open-circuit voltage
The open-circuit voltage has been too high.
Action:
Turn off the mains power supply to reset the unit. If the fault persists,
send for a service technician.
17
Lost contact
The control panel has lost contact with the wire feed unit.
The current welding process is stopped.
Action:
Check the cables. If the fault persists, send for a service technician.
18
Lost contact
The control panel has lost contact with the power unit.
The current welding process is stopped.
Action:
Check the cables. If the fault persists, send for a service technician.
19
Incorrect settings values in external RAM
This fault will be detected if the information in the battery-backed memory
has become corrupted.
Action:
The fault will correct itself, but the data stored in the current memory
position will be lost.
Содержание Aristo U6
Страница 1: ...Aristo Instruction manual 0459 287 474 GB 20160127 Valid for from program version 2 12A U6 ...
Страница 35: ...DIAGRAM 0459 287 474 35 ESAB AB 2016 DIAGRAM ...
Страница 38: ...MENU STRUCTURE 0459 287 474 38 ESAB AB 2016 MENU STRUCTURE ...
Страница 39: ...MENU STRUCTURE 0459 287 474 39 ESAB AB 2016 ...
Страница 40: ...MENU STRUCTURE 0459 287 474 40 ESAB AB 2016 ...
Страница 41: ...MENU STRUCTURE 0459 287 474 41 ESAB AB 2016 ...
Страница 42: ...MENU STRUCTURE 0459 287 474 42 ESAB AB 2016 ...
Страница 43: ...MENU STRUCTURE 0459 287 474 43 ESAB AB 2016 ...
Страница 44: ...MENU STRUCTURE 0459 287 474 44 ESAB AB 2016 ...