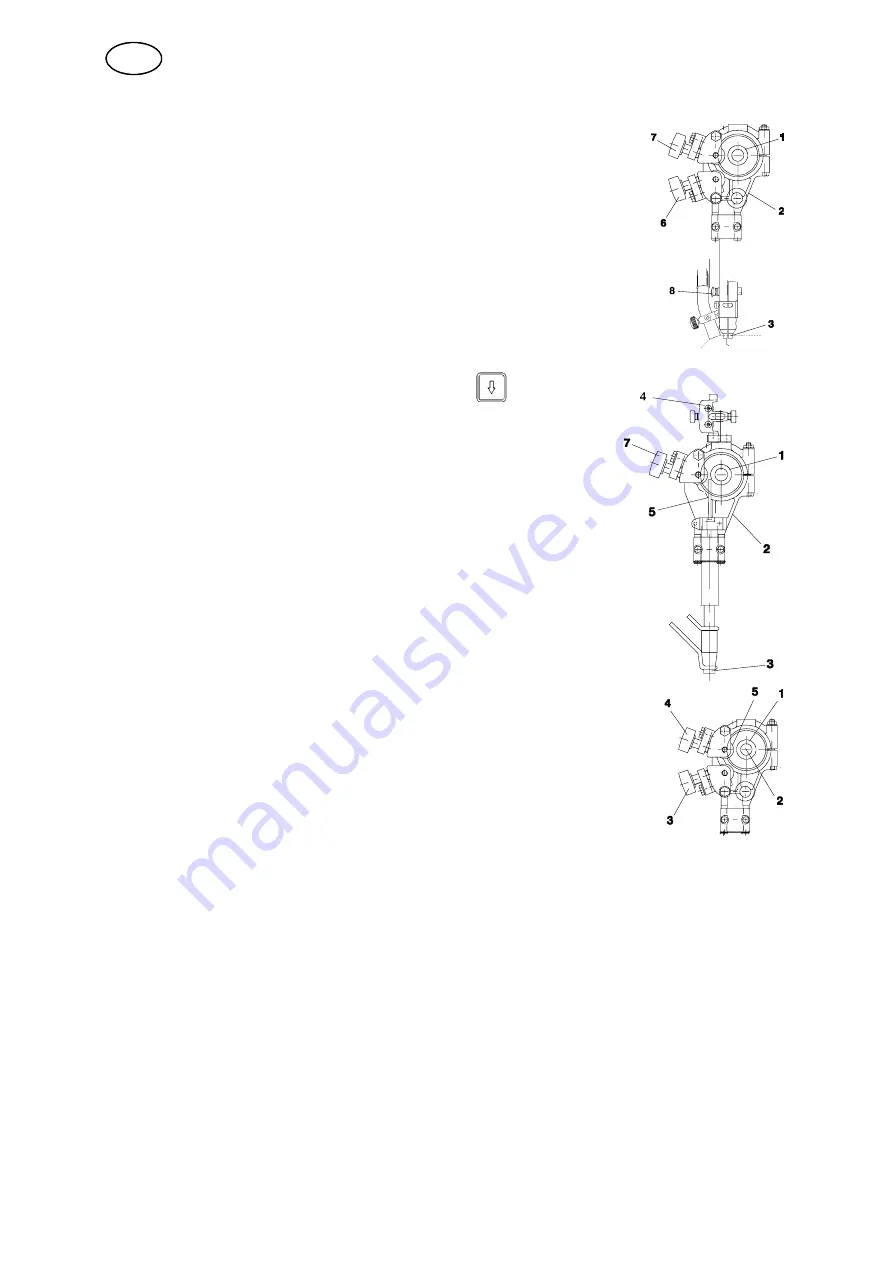
SAW
MIG/MAG
-- 71 --
ffa9d1ea
S
Check that the feed roller (1) and contact jaw or contact tip
(3) are of the correct dimension for the selected wire size.
S
Pull the end of the wire through the straightener (2). For a
wire diameter greater than 2 mm; straighten out 0.5 m of
wire and feed it by hand down through the straightener.
S
Locate the end of the wire in the feed roller (1) groove.
S
Set the wire tension on the feed roller with the knob (7).
Note!
Do not tension more than is required to achieve an
even feed.
S
The pressure screw (8) must not be dismantled. (Applies to
Submerged--arc Heavy duty).
S
Feed the wire forward 30 mm by pressing
on the
control box A2--A6 Process Controller.
S
Direct the wire by adjusting the knob (6).
For fine wire, the special fine wire straightener (4) is used
for both single and twin wire.
Ensure that the straightener is correctly adjusted so that the
wire emerges straight out through the contact jaws or
contact tip.
Always use a guide tube (5) to ensure even feeding of fine
wire (1.6 -- 2.5 mm).
For MIG/MAG welding with wire sizes < 1.6 mm, use a
guide spiral, which is inserted in the guide tube (5).
Changing the feed roller
S
Single wire
S
Release the knobs (3) and (4).
S
Release the hand wheel (2).
S
Change the feed roller (1). The rollers are marked with
their respective wire sizes.
S
Twin wire (Twin--arc)
S
Change the feed roller (1) with twin grooves in the same way as for single
wire.
S
NOTE!
The pressure roller (5) must also be changed. A special spherical
pressure roller for twin wire replaces the standard pressure roller for single
wire.
S
Assemble the pressure roller with special stub shaft
(order no. 146 253--001).
S
Flux--cored wire
(for knurled rollers)
S
Change the feed roller (1) and pressure roller (5) in pairs for the wire size to
be used.
NOTE!
A special stub shaft is required for the pressure roller
(order no. 0212 901 101).
S
Tighten the pressure screw (4) with moderate pressure to ensure that the
flux--cored wire does not deform.
GB