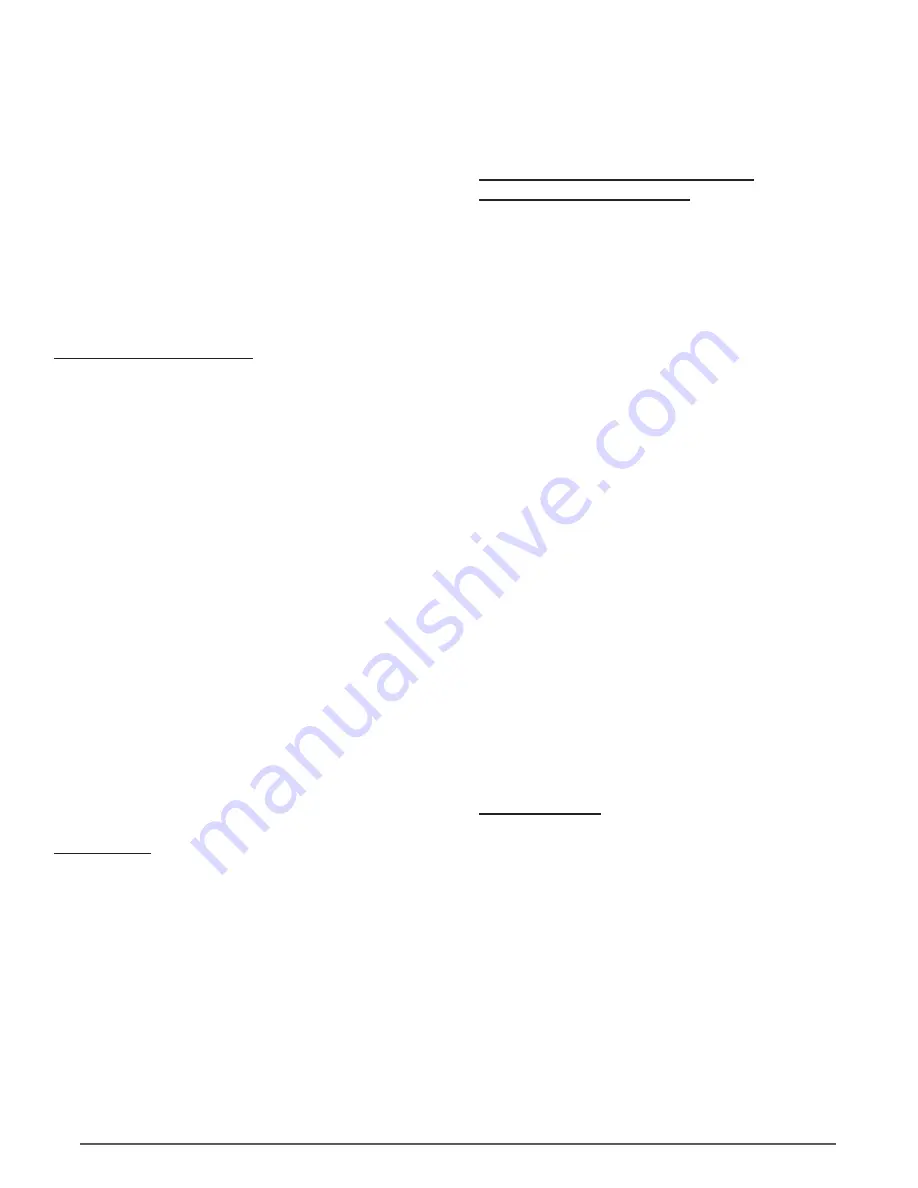
p 4
Eraser Company Inc. • Syracuse, NY USA • Ph: 315-454-3237 • [email protected] • www.eraser.com • Fax 315-454-3090
!
Caution: The rigid tubing cutting wheel head is
intended for rigid tubing. Thin wall soft steel is
the practical limit for the machine.
Place the Model RTC1 on a sturdy workbench with
the right corner of the exit opening even with the
right corner of the bench. Short and long cut lengths
will drop out the side of the exit bushing. Material
collection bins can be placed to collect the cut
material as it exits the unit.
BUSHING INSTALLATION:
To aid in bushing installation refer to the drawing.
If different sizes of material are going to be cut,
additional bushing sets must be ordered. There
are two guide bushings, the input and exit bushing.
Install the input bushing & gently tighten the set
screw with the 3/32 Allen wrench. Install the exit
bushing in the front cover with the two screws
provided.
See pictures 1 & 2
.
Feed the tubing in through the input bushing and out
through the exit bushing. Set the length stop block
to approximately provide the desired cut length.
While gently squeezing them together, tighten
the adjacent collars with the provided 7/64” Allen
wrench. The actual cut length may be refined after a
sample is cut. Longer cut lengths may be produced
by purchasing additional length stop rods (TR0176)
which may be screwed directly into the one provided
with the machine.
See picture 1
.
Connect the power cord to the IEC connector, and
plug the unit into the appropriate power supply
(either 120V 60Hz OR 230V 50Hz).
OPERATION:
Push the material through the input bushing, head,
& exit bushing until it reaches the length stop block.
See pictures 1 & 2.
Turn the machine on using the I/O switch on the top
of the unit. Set the speed control to approximately
75% as a starting point. Depress the footswitch to
cut the material. When the material is cut; release
the footswitch. The cut time will vary based the
material being cut. Cut times will range from a
fraction of a second to several seconds. Lower
machine speeds may cut better on lighter or softer
materials & higher speeds will be necessary for
thicker wall or harder materials. Rotate the length
Model RTC1 Rigid Tube Cutter
stop block, remove cut piece & return block to
verticle position.
See picture 2.
CUTTING WHEEL REPLACEMENT,
AND DEPTH ADJUSTMENT:
!
CAUTION: BE SURE UNIT IS UNPLUGGED
BEFORE CHANGING CUTTING WHEELS.
To replace the cutting wheels first remove the 2
screws near the top of the front cover with a 1/8”
Allen wrench. Lift off the cover. Remove 2 roller
holder screws with the 5/32 Allen wrench. Remove
1 brass washer & the cutting wheel assembly from
the roller holder. Using (2) 1/2” wrenches loosen the
jam nut from the disk bushing & remove the cutting
wheel. Install the new cutting wheel & reverse the
disassembly procedure to reassemble. Repeat this
process for the other cutter wheel.
See pictures 1,3
& 4.
To adjust the cutting wheels deeper, turn the depth
screws counterclockwise using the 5/32” Allen
wrench provided. The depth is properly set when the
cutting wheels are slightly deeper than the inside
wall of the tubing being cut. The depth screws must
be adjusted equally for the cutting head to function
properly.
See pictures 3 & 4.
!
CAUTION: BE CERTAIN THAT THE JAM NUT
SIDE OF THE CUTTER WHEEL ASSEMBLY
FACES THE ROLLER HOLDER. IF THE DISK
BUSHING SIDE FACES THE ROLLER HOLDER
THE CUTTER WILL NOT OPERATE.
MAINTENANCE:
!
CAUTION: BE SURE TO UNPLUG THE UNIT
BEFORE PERFORMING ANY MAINTENANCE.
BE SURE TO EMPLOY APPROPRIATE ANTI-
STATIC PROCEDURES/DEVICES WHEN
DISASSEMBLING AND ASSEMBLING UNIT.
1)
Check the cutting wheels for wear after
prolonged use.
See pictures 3 & 4.
2)
Belt tensioning or replacement begins with
removing 4 screws & the rear housing with a #2
Phillips screwdriver. Remove the 2 screws & the
front cover with a 1/8” Allen wrench. Loosen the
4 motor mounting screws using the 5/32 Allen
wrench. Slip the old belt off the cutterhead pulley