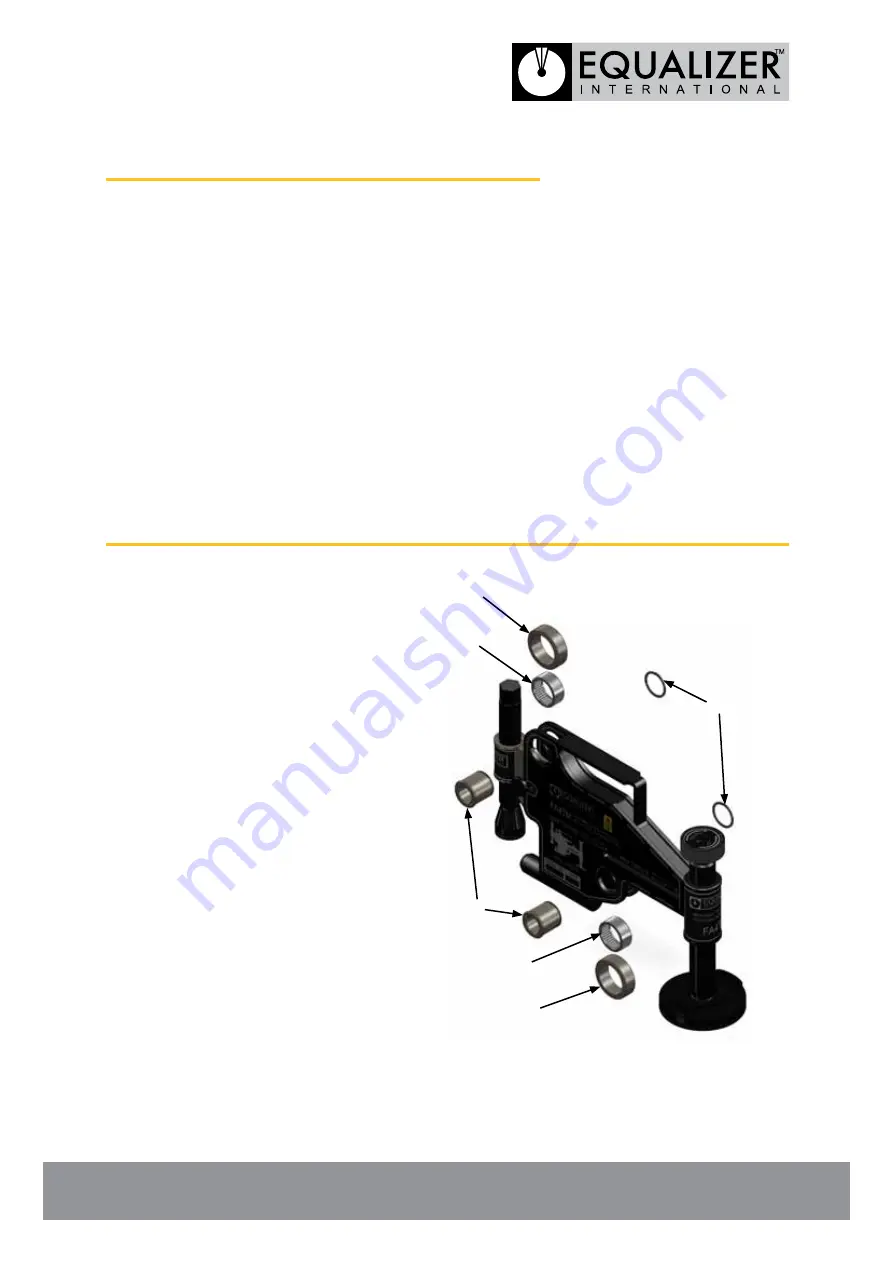
FLANGE ALIGNMENT TOOLS
OPERATOR INSTRUCTION MANUAL
PAGE 13
•
On return from each job and before allocation against subsequent work the
completeness of the Equalizer FA4TM kit must be established and
items examined to ensure that they are serviceable
•
Any missing or damaged items are to be replaced as soon as possible and prior to the
tool being used again
•
Store the FA4TM in a cool dry place and ensure all machined surfaces
are greased
•
Return all items to carry case when not in use
•
Ensure rollers, pins and wing remain grit free and that the rollers rotate freely
•
Grease all moving parts regularly:
5.4 EXAMINATION, MAINTENANCE AND STORAGE
1.
Secure the tool upright on a
bench.
2.
Using a small flat screw driver, lever
out the end of the spiral clips and
then rotate anti-clockwise and
remove.
3.
Slide the roller shafts out in order to
remove the rollers and bearings for
examination.
4.
Inspect the roller shafts, rollers and
bearings for damage. If there is no
damage present then they can be
cleaned, greased and re-assembled
by reversing steps 1-4
Recommended grease -
Hi-load bearing grease
e.g. Rocol Saphire hi-load
SPIRAL
CLIPS
NEEDLE
BEARING
ROLLER
NEEDLE
BEARING
ROLLER
ROLLER
SHAFTS