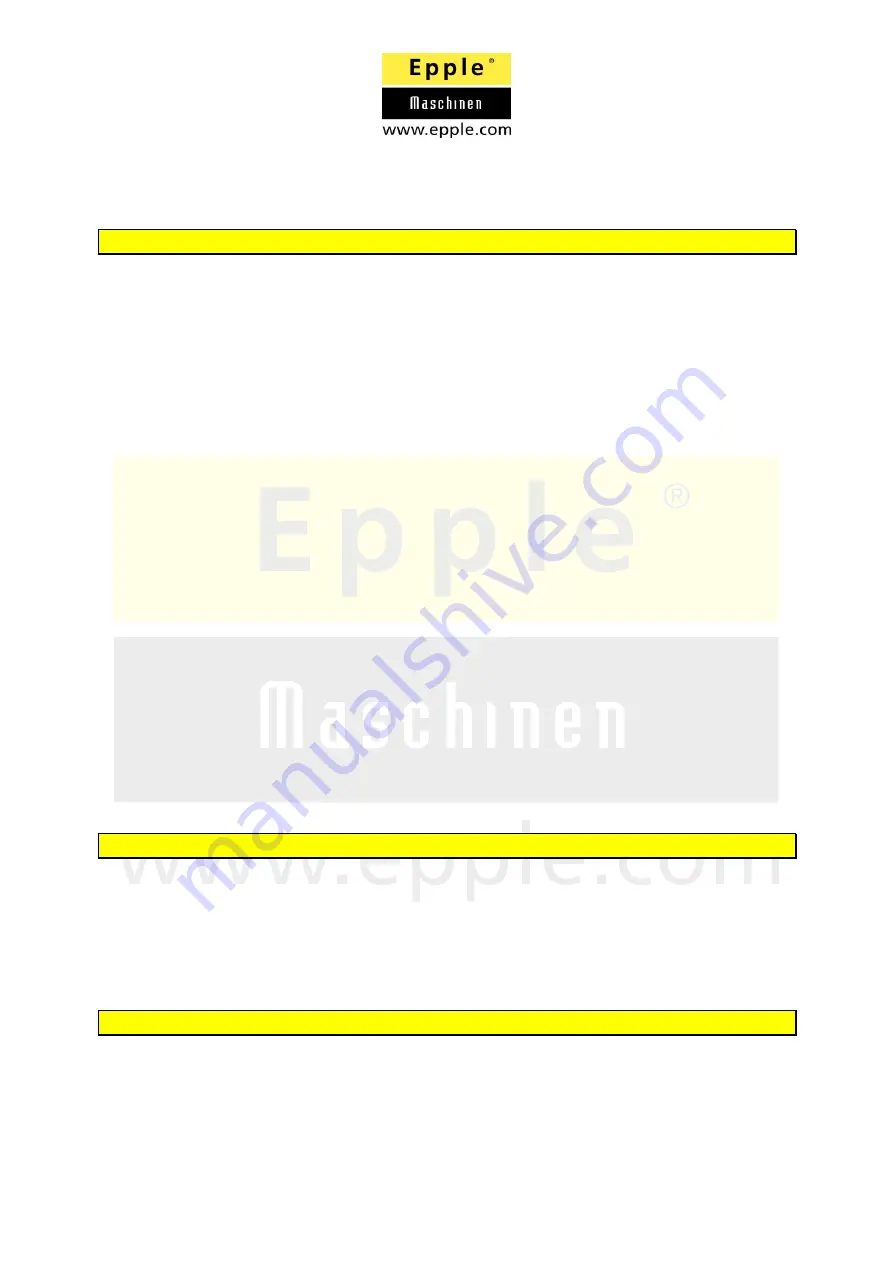
26.01.07, SBS 32, Drills
Page 2 from 33
Table of contents
Danger, which can emanate from drill ..............................................................8
Special claims to the qualification ...........................................................11
Prohibition, instruction and warning signs .............................................12
Personal protective equipment for special work ............................................ 14
Safety during general maintenance work ....................................................... 16
Breaking and assuring the machine ........................................................16
Use of hoisting devices for attendance work ..........................................16
Mechanic attendance work at the machine .............................................17
Claims to installation location..................................................................20
Содержание SBS 32 400 V
Страница 1: ...26 01 07 SBS 32 Drills Page 1 from 33 User manual Drill SBS 32 400 V Keep for future reference ...
Страница 4: ...26 01 07 SBS 32 Drills Page 4 from 33 7 1 Copyright 30 7 2 Product follow up 30 ...
Страница 31: ...26 01 07 SBS 32 Drills Page 31 from 33 8 Exploded view 8 1 Exploded view SBS 32 ...