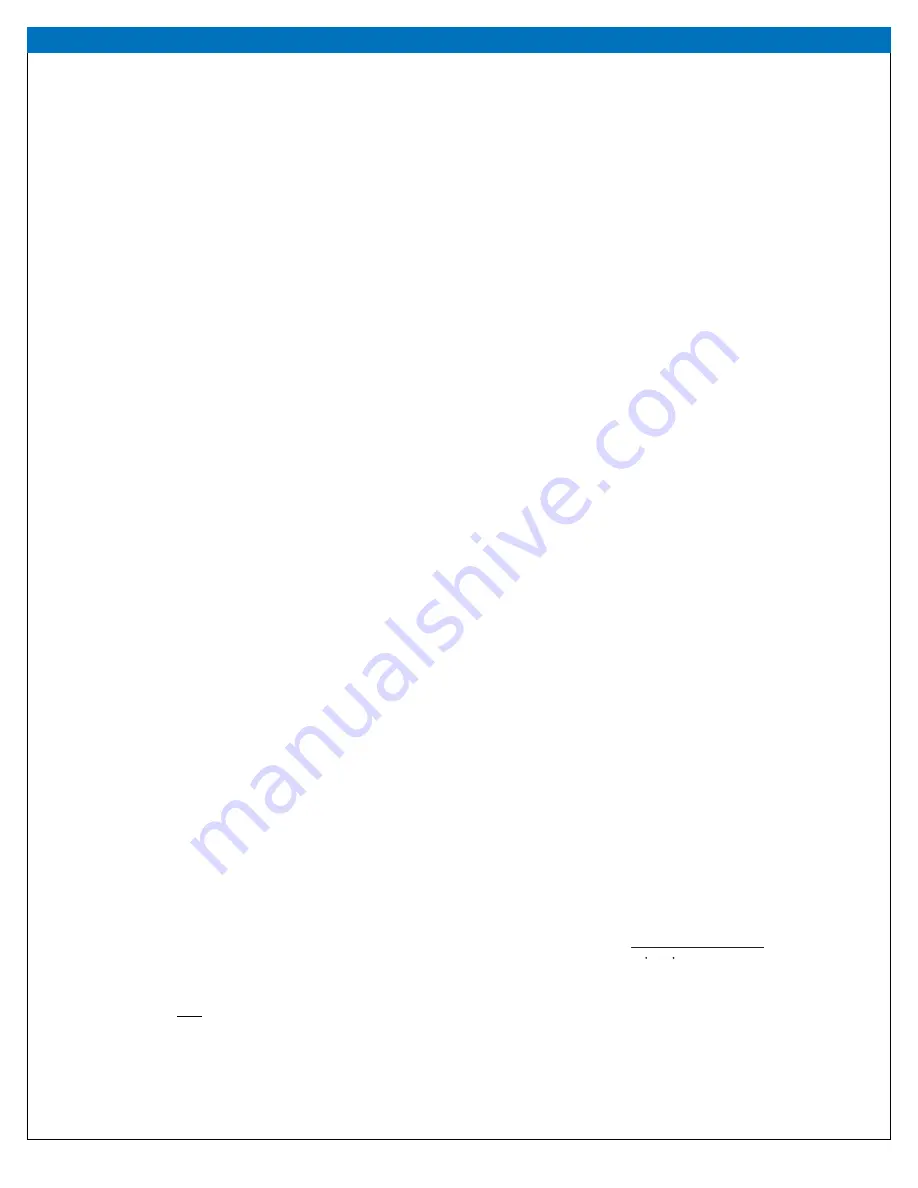
QUICK START GUIDE
4 | | EPC – EFFICIENT POWER CONVERSION CORPORATION |
WWW.EPC-CO.COM
| COPYRIGHT 2018
Demonstration System EPC9129
The pre-regulator can also be disabled in a similar manner as the
oscillator using JP50. However, note that this connection is floating
with respect to the ground so removing the jumper for external
connection requires a floating switch to correctly control this function.
Refer to the datasheet of the controller IC and the schematic in this
quick start guide for specific details.
The ZVS timing adjust circuits for the ZVS class-D amplifiers are each
independently settable to ensure highest possible efficiency setting
and includes separate ZVS tank circuits.
Additional protection features
An undervoltage-lockout circuit has been implemented for the input
voltage (V
IN
). The amplifier board will not start unless V
IN
reaches its
minimum required value specified in table 1.
A clamp diode also protects the board from V
IN
over-voltage for a
brief period and accidental reverse polarity connection with up to
11 A current protection.
On-Off-Key (OOK) modulation
On-Off-Key (OOK) modulation (as illustrated in figure 6) can be
implemented by applying the modulation signal at J76. It is
compatible with 5 V logic only. When the signal is high, the power
stage functions normally; when the signal is low, the gate drive signal
of one half-bridge is shut off. Therefore, for optimal performance,
the signal should be synchronized with the oscillator signal. The
modulation signal should also change state between the oscillator
states and must complete an even number of clock cycles. Failure
to follow this will lead to DC voltage shift on the ZVS capacitor (C
zvs
)
and other harmonic generation issues in the amplifier output. The
OOK modulation frequency will also become present and thus could
lead to radiated emission violations if the frequency exceeds what is
allowed in the ISM band.
When not using OOK modulation, J76 should be left open – an on-
board pull-up resistor keeps the level high.
Single ended or Differential Mode operation
The EPC9512 amplifier can be operated in one of two modes; single-
ended or differential mode. Single ended operation offers higher
amplifier efficiency but reduced imaginary impedance drive capability.
If the reflected impedance of the tuned coil load exceeds the capability
of the amplifier to deliver the desired power, then the amplifier can be
switched over to differential mode. In differential mode, the amplifier
is capable of driving an impedance range of 1 Ω through 56 Ω and
±35j Ω and maintains either the 1.375 A
RMS
coil current or deliver up to
33 W of power. The EPC9512 is set by default to differential mode and
can be switched to single ended mode by inserting a jumper into J75.
When inserted the amplifier operates in the single-ended mode.
Using an external pull down with floating collector drain connection
will have the same effect. The external transistor must be capable of
sinking 25 mA and withstand at least 6 V.
For differential mode only operation, the two ZVS inductors L
ZVS1
and
L
ZVS2
can be replaced by a single inductor L
ZVS12
and by removing C
ZVS1
and C
ZVS2
.
ZVS Timing Adjustment
Setting the correct time to establish ZVS transitions is critical to
achieving high efficiency with the EPC9512 amplifier. This can be
done by selecting the values for R71, R72, R77, and R78 or P71, P72,
P77, and P78 respectively. This procedure is best performed using a
potentiometer installed at the appropriate locations that is used to
determine the fixed resistor values. The procedure is the same for
both single-ended and differential mode of operation. The timing
MUST initially be set WITHOUT the source coil connected to the
amplifier. The timing diagrams are given in figure 12 and should
be referenced when following this procedure. Only perform these
steps if changes have been made to the board as it is shipped
preset. The steps are:
1. With power off, remove the jumper in JP1 and install it into JP50 to
place the EPC9512 amplifier into Bypass mode. Connect the main
input power supply (+) to JP1 (bottom pin for bypass mode) with
ground connected to J1 ground (-) connection.
2. With power off, connect the control input power supply bus (19 V)
to (+) connector (J1). Note the polarity of the supply connector.
3. Connect a LOW capacitance oscilloscope probe to the probe-hole
of the half-bridge and the ground post.
4. Turn on the control supply – make sure the supply is approximately
19 V.
5. Turn on the main supply voltage starting at 0 V and increasing
to the required predominant operating value (such as 24 V but
NEVER exceed the absolute maximum voltage of 80 V).
6.
While observing the oscilloscope adjust the applicable
potentiometers to achieve the green waveform of figure 12.
7. Repeat for the other half-bridge.
8. Replace the potentiometers with fixed value resistors if required.
Remove the jumper from JP50 and install it back into JP1 to
revert the EPC9512 back to pre-regulator mode.
Determining component values for L
ZVS
The ZVS tank circuit is not operated at resonance, and only provides
the necessary negative device current for self-commutation of the
output voltage at turn off. The capacitors C
ZVS1
and C
ZVS2
are chosen
to have a very small ripple voltage component and are typically
around 1 µF. The amplifier supply voltage, switch-node transition
time will determine the value of inductance for L
ZVSx
which needs
to be sufficient to maintain ZVS operation over the DC device load
resistance range and coupling between the device and source coil
range and can be calculated using the following equation:
Where:
Δt
vt
= Voltage Transition Time [s]
ƒ
SW
= Operating Frequency [Hz]
C
OSSQ
= Charge Equivalent Device Output Capacitance [F]
C
well
= Gate driver well capacitance [F]. Use 20 pF for the LM5113
L
ZVS
=
∆
t
vt
8 f
sw
(C
OSSQ
+ C
well
)
(1)