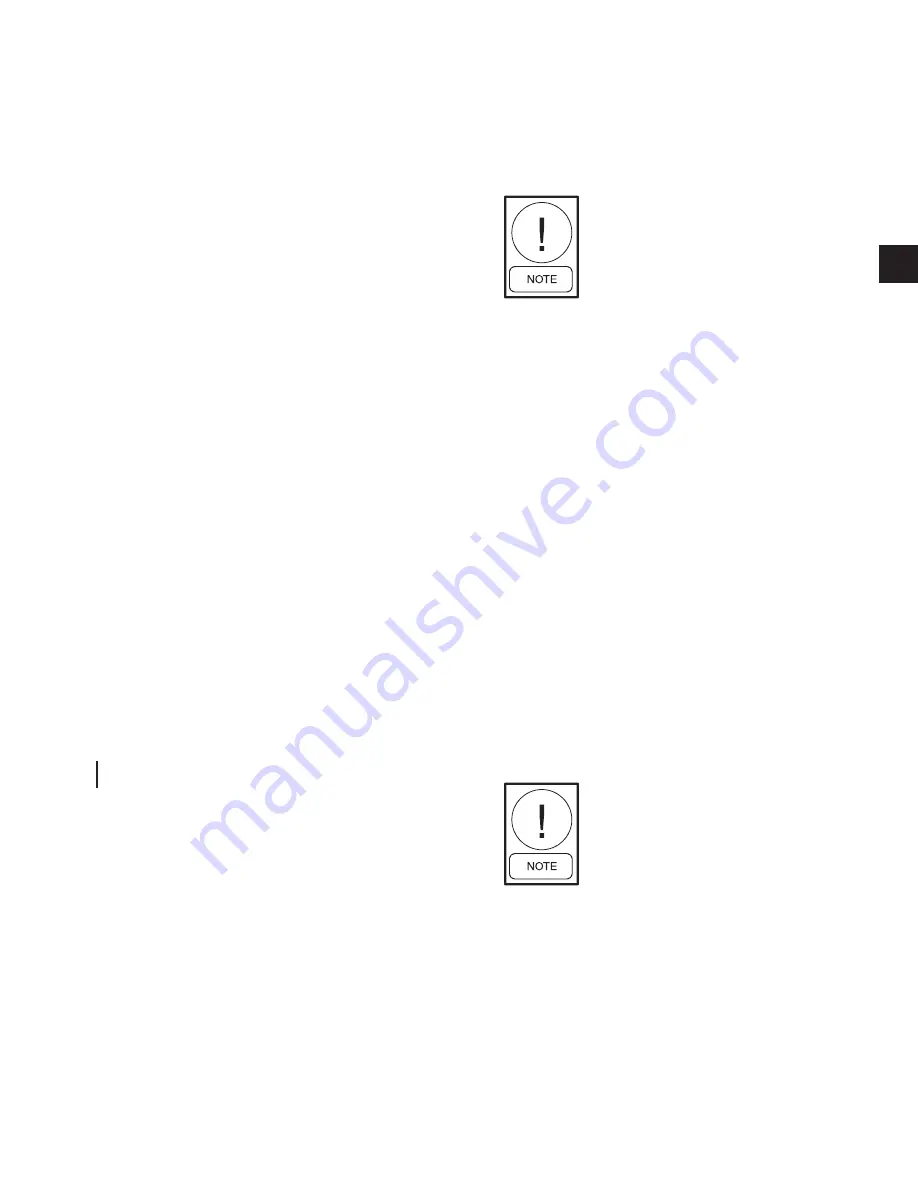
4
2. DX coils are shipped capped and sealed with a 20
PSIG holding charge of dry nitrogen. Remove ni-
trogen charge from coil by depressing Schraeder
stem, prior to cap removal.
3. Heat the soft solder and remove the Schraeder
valve and flare.
4. Attach thermal expansion valve to distributor.
5. Do not apply heat to the body or thermal element
of the expansion value. Wrap in wet rag while
brazing.
6. The thermostatic expansion valve must be of the
external equalizer tube type. Connect the ¼-inch
diameter external equalizer tube provided on the
coil to connection on expansion valve.
7. Care should be exercised when piping up the sys-
tem to be sure all joints are tight and all lines are
dry and free of foreign material.
Steam Coils
(maximum steam pressure is 15 PSIG)
1. Steam supply and steam return connections are
male N.P.T. copper pipe and are labeled on the end
panel of coil section. Connections extend through
coil section end panel.
2. When installing couplings, do not apply undue
stress to the connection extending through unit
panel. Use backup pipe wrench to avoid breaking
the weld between coil connection and header.
3. Support piping independently of coils and provide
adequate piping flexibility. Stresses resulting from
expansion of closely coupled piping can cause se-
rious damage.
4. Do not reduce pipe size at the coil return connec-
tion. Carry return connection size through the dirt
pocket, making the reduction at the branch lead-
ing to trap.
5. It is recommended that vacuum breakers be in-
stalled on all applications to prevent retaining con-
densate in the coil. Generally, the vacuum breaker
is to be connected between the coil inlet and the
return main, the vacuum breaker should be open
to the atmosphere and the trap design should al-
low venting of large quantities of air.
6. Do not drip supply mains through the coil.
7. Do not attempt to lift condensate when using
modulating or on/off control.
8. Size traps in accordance with manufacturers’ rec-
ommendations. Be certain that the required pres-
sure differential will always be available.
Do not undersize.
9. Float and thermostatic or bucket traps are recom-
mended for low-pressure steam. Thermostatic
traps should be used only for air venting.
10. Locate traps at least 12 inches below the coil re-
turn connection.
11. Multiple coil installation.
a. Each coil or group of coils that is individu-
ally controlled must be individually trapped.
b. Coils in series: Separate traps are required
for each coil, or bank of coils, in series.
c. Coils in parallel: A single trap may generally
be used but an individual trap for each coil is
preferred.
d. Do not attempt to lift condensate when using
modulating or on/off control.
12.
With coils arranged for series airflow, a separate
control is required on each back or coil in the di-
rection of airflow.
13. Modulating valves must be sized properly.
Do not undersize.
14. Freezing conditions (entering air temperature be-
low 35ºF)
a. 5-psi steam must be supplied to coils at all
times.
b. Modulating valves are not recommended.
c. Consideration should be given to the use of
two or three coils in series with two posi-
tion steam control valves on that coil or coils
ENVIRO-TEC
31
SECTION 4 - PERIODIC MAINTENANCE AND SERVICE
FORM ET102.19-NOM1 (0521)
Содержание MQL B Series
Страница 8: ...THIS PAGE INTENTIONALLY LEFT BLANK ENVIRO TEC 8 FORM ET102 19 NOM1 0521 LIST OF FIGURES...
Страница 12: ...THIS PAGE INTENTIONALLY LEFT BLANK ENVIRO TEC 12 FORM ET102 19 NOM1 0521 Section 1 introduction...
Страница 18: ...INTENTIONALLY LEFT BLANK ENVIRO TEC 18 FORM ET102 19 NOM1 0521 Section 2 installation...
Страница 35: ...5 ENVIRO TEC 35 Section 5 TROUBLESHOOTING FORM ET102 19 NOM1 0521...