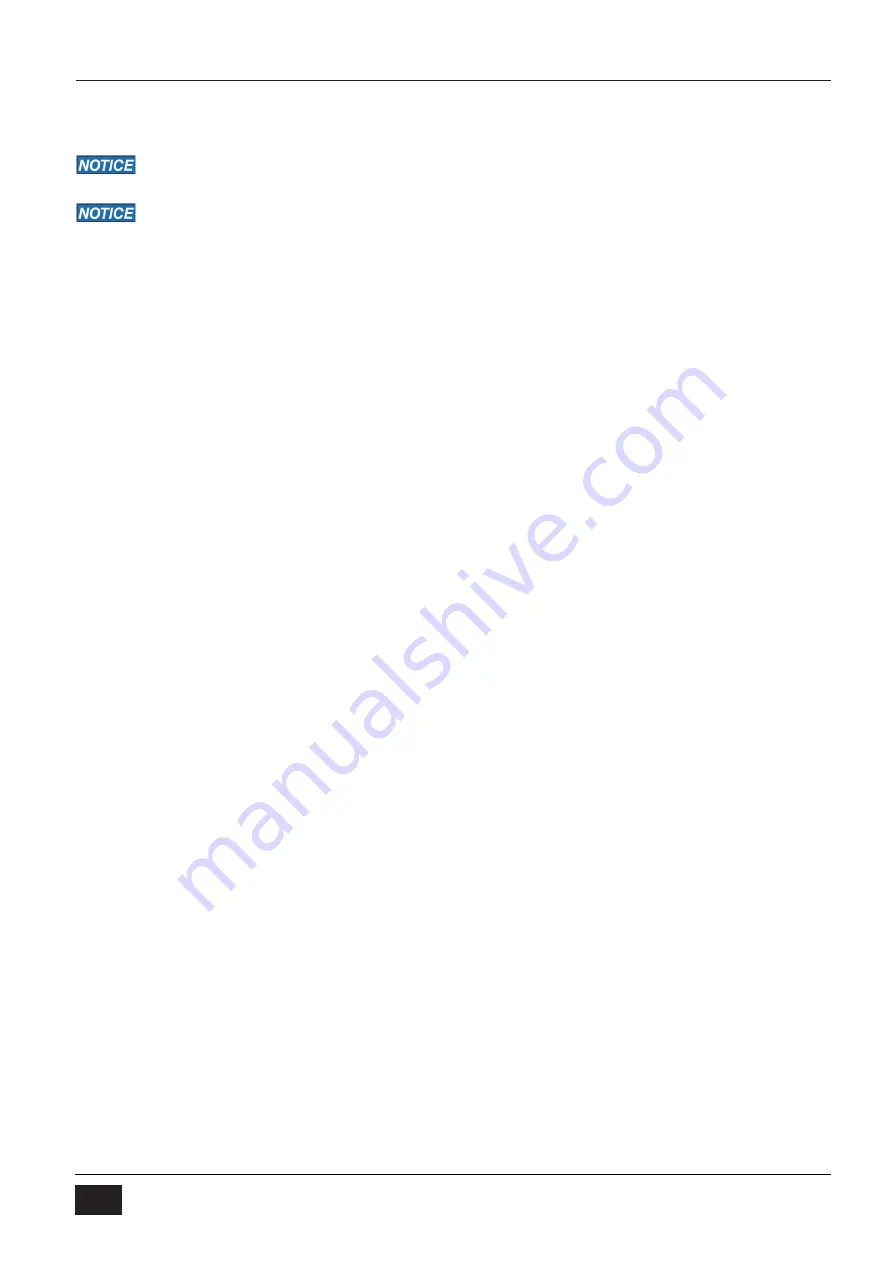
18
RSL Torque Wrench
5 Warranty, Maintenance and Assembly
5.1 General
Always assess risks and mitigate hazards
while performing maintenance and assembly work.
Follow all applicable safety procedures.
5.1.1 STORAGE: Clean and lubricate tool if
stored (not used) for 5 days or more
5.1.2 SERVICE: Enerpac highly recommends
customers have their tools repaired by
Enerpac, or a Enerpac approved service
center.
5.1.3 These Items Void Tool Warranty:
a.
Failure to use Enerpac replacement
parts
b. Inadequate or improper lubrication
c. Failure to replace worn or cracked parts
d. Operating tool at excessive pressure
e. Striking tool with a hammer or other
impact device
f. Tool modification
g. Improper reaction method
h. See tool warranty for complete details.
5.2 Torque Wrench Drive Maintenance
5.2.1 If seal has small leak, replace seal because
of high hydraulic pressure hazard. Refer to
RPS for seal kit information.
5.2.2 Check zero leak plug / plug (Refer to RPS
for location) for o-ring extrusion and/or oil
leak. Re-tightening or replace plug. See
notes in Section 5.3.
5.2.3 Check front cap (or end cap) for oil leak.
Re-tightening cap and/or replace seal. See
notes in Section 5.3.
5.2.4 Hose service life and replacement intervals:
a. Due to the wide variety of operating
conditions, Enerpac cannot define or
guarantee exact hose assembly:
i. Service life
ii. Inspection intervals
iii. Replacement intervals
b.
As a general industry practice, the
maximum recommended hose assembly
service life is 6 years, including storage
time of the hose assembly. This will be
impacted by the application, pressure
cycles, cleanliness, environment, abuse,
etc.
5.2.5 Clean and lubricate bronze block and pawl
driver mating surfaces. Use appropriate
lubricant. Frequency:
a.
Depends on work environment -
increase frequency if tool is exposed to
sand or other abrasive material.
b. Increase frequency with high operating
pressure.
c. Increased frequency lengthens tool life.
5.2.6 Before each use:
a.
Check for oil leaks and repair
immediately.
b. Inspect tool structure (including splines,
torque wrench drive, reaction arm, etc.)
for cracks, chips, galling, or deformities.
If irregularities are found, service or
replace immediately.
c.
Check retractor, bronze block, and
retractor pin for fit.
d. Hoses and QC's:
i. Clean properly.
ii. Inspect thoroughly for damage,
including underneath the strain reliefs.
iii. Hoses shall be replaced if they have
any damage, including, but not limited
to: kinks, exposed wires, nicks, cuts,
scrapes, and dents. If in doubt, replace
the hose.
iv. Replace missing hose strain reliefs.
e. Confirm torque wrench drive and wrench
cassette are:
i. Properly engaged – Retractor pin is
inserted properly in pawl driver slot
ii. Secured properly with socket head cap
screws, screws torqued per Table 4.6-1.