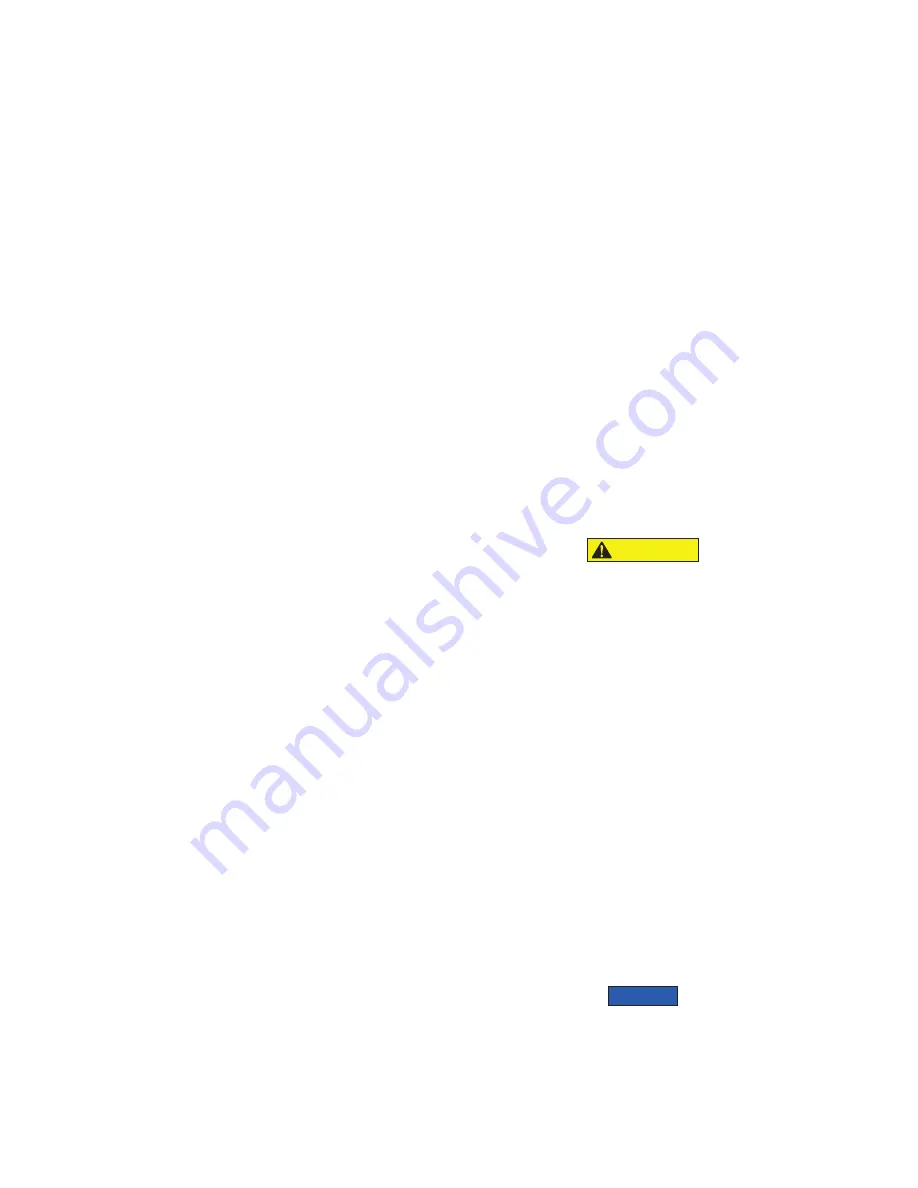
2
Use of additional P.P.E. safety items such as dust mask,
non-skid safety shoes, hard hat, and hearing protection
(used as appropriate for the conditions) will reduce the
chance of personal injuries. The use of these items may also
be required by local regulations or laws.
• Do not handle pressurized hoses. Escaping oil under
pressure can penetrate the skin. If oil is injected under the
skin, see a doctor immediately.
• Do not pressurize disconnected couplers.
• Use hydraulic cylinders only in a coupled system. It is
acceptable to use a cylinder with a disconnected coupler
only if the load is mechanically supported by the cylinder
lock nut, and all hydraulic pressure is completely relieved.
• When holding loads, be certain that the lock nut is turned
down firmly against the cylinder base so that the load is
mechanically supported. Also be sure that all hydraulic
pressure is completely relieved.
• Do not remove or disable the pump relief valve.
• Do not remove or disable the cylinder relief valve (if equipped).
• The system operating pressure must not exceed the pressure
rating of the lowest rated component in the system.
• Install pressure gauge(s) in the system to monitor operating
pressure. It is your window to see what is happening in the system.
• Never set a relief valve to a higher pressure than the
maximum rated pressure of the pump and cylinder. If ratings
are different, relief valve setting should not exceed the
setting of the lowest rated component (pump or cylinder).
• The HCRL-Series cylinders are designed for a maximum
working pressure of 10150 psi [700 bar]. Do not connect a
pump with a higher pressure rating to these cylinders.
• Do not exceed equipment ratings. Never attempt to lift a
load weighing more than the rated capacity of the cylinder.
Overloading may cause equipment failure and possible
personal injury.
• Be sure setup is stable before lifting load. Cylinders should
be located on a firm and level surface capable of supporting
the full load.
• Where applicable, use a cylinder base plate to provide
added stability. If desired, the cylinder can be bolted to the
base plate, using the bolt holes in the bottom of the cylinder
base.
• Do not weld, drill or otherwise modify a cylinder to attach a
base plate or other support unless approved in writing by
Enerpac Engineering Department. Use only the provided
bolt holes.
• Always perform a visual inspection of the cylinder before
placing it into operation. If any problems are found, do not
use the cylinder. Have the cylinder repaired and tested
before it is returned to service.
• Never use a cylinder that is leaking oil. Do not use a cylinder
that is damaged, altered or in need of repair.
• Always lift the cylinder using a hoist, crane or other suitable
lifting device of sufficient rated capacity. Use only the
supplied cylinder lifting eyes to attach the cylinder to the
lifting device. Replace any missing or damaged lifting eyes.
• Allow only trained and experienced personnel to supervise
and perform lifting and lowering procedures.
• Be certain that no persons are working on or near any
cylinders before lifting or lowering of the load begins. Alert all
personnel in advance that lifting or lowering is about to occur.
• Use suitable cribbing of rigid construction to hold loads.
• Never use a hydraulic cylinder as a shim or spacer in any
lifting or pressing application.
• Be certain that the load is centered and covers the entire
plunger saddle surface. Avoid situations where loads are not
directly centered on the plunger saddle. The load may slip or
fall, causing potential danger.
• Lift only dead weight loads. Avoid lifting live weight loads.
• Be especially careful when lifting loads such as partially filled
storage tanks, in which the center of gravity could move or
shift during lifting. Be aware that the distribution of some
loads can change quickly and without warning.
• Do not use the cylinder to lift people. Do not allow people to
be on top of the load during lifting or lowering.
• Keep all personnel clear of the work area while lifting or
lowering is in progress. To avoid personal injury, keep hands
and feet away from cylinder and load during operation.
• Maintain communication with the operator at all times during
lifting or lowering to avoid accidents. Use hand signals, two-
way radios or other appropriate forms of communication (as
required by applicable laws and regulations) if the load is not
visible to the operator.
• Operate pump and valve as required to ensure that the load
is lifted and lowered evenly and at a controlled rate.
• Closely watch the load at all times during lifting and lowering.
Stop lifting or lowering immediately if the load becomes
unstable or appears to be lifting or lowering unevenly.
• Stay clear of loads supported only by hydraulics. As required,
follow the lifted load with cribbing.
• Never allow persons to work under or near the load while the
load is being supported hydraulically. After the load has been
raised or lowered, it always must be blocked mechanically
by the cylinder lock nut or via suitable cribbing.
• Always be certain that hydraulic pressure is fully relieved
and that the load is fully removed from the cylinder(s) before
disconnecting hydraulic hoses, loosening hydraulic fittings,
or performing any cylinder disassembly or repair procedures.
CAUTION
Failure to observe and comply with the following
precautions could result in minor or moderate personal
injury. Property damage could also occur.
• Be careful to avoid damaging hydraulic hoses. Avoid sharp
bends and kinks when routing hydraulic hoses. Do not
exceed the minimum bend radius specified by the hose
manufacturer. Using a bent or kinked hose will cause severe
back-pressure. Sharp bends and kinks will internally damage
the hose, leading to premature hose failure.
• Do not drop heavy objects on hoses. A sharp impact may
cause internal damage to hose wire strands. Applying
pressure to a damaged hose may cause it to rupture.
• Do not lift hydraulic equipment by the hoses or couplers.
Use the cylinder lifting eyes and appropriately rated lifting
equipment.
• Keep hydraulic equipment away from flames and heat.
Excessive heat will soften packings and seals, resulting in
fluid leaks. Heat also weakens hose materials and packings.
• For optimum performance, do not expose hydraulic
equipment to temperatures of 150˚F [65˚C] or higher. Protect
all hydraulic equipment from weld spatter.
• Immediately replace worn or damaged parts with genuine
Enerpac parts. Enerpac parts are designed to fit properly
and to withstand high loads. Non-Enerpac parts may break
or cause the product to malfunction.
NOTICE
• Hydraulic equipment must only be serviced by a qualified
hydraulic technician. For repair service, contact the Enerpac
Authorized Service Center in your area.
• To help ensure proper operation and best performance, use
of Enerpac oil is strongly recommended.
Содержание HCRL-10010
Страница 11: ...Notes 11 ...
Страница 12: ...www enerpac com ...