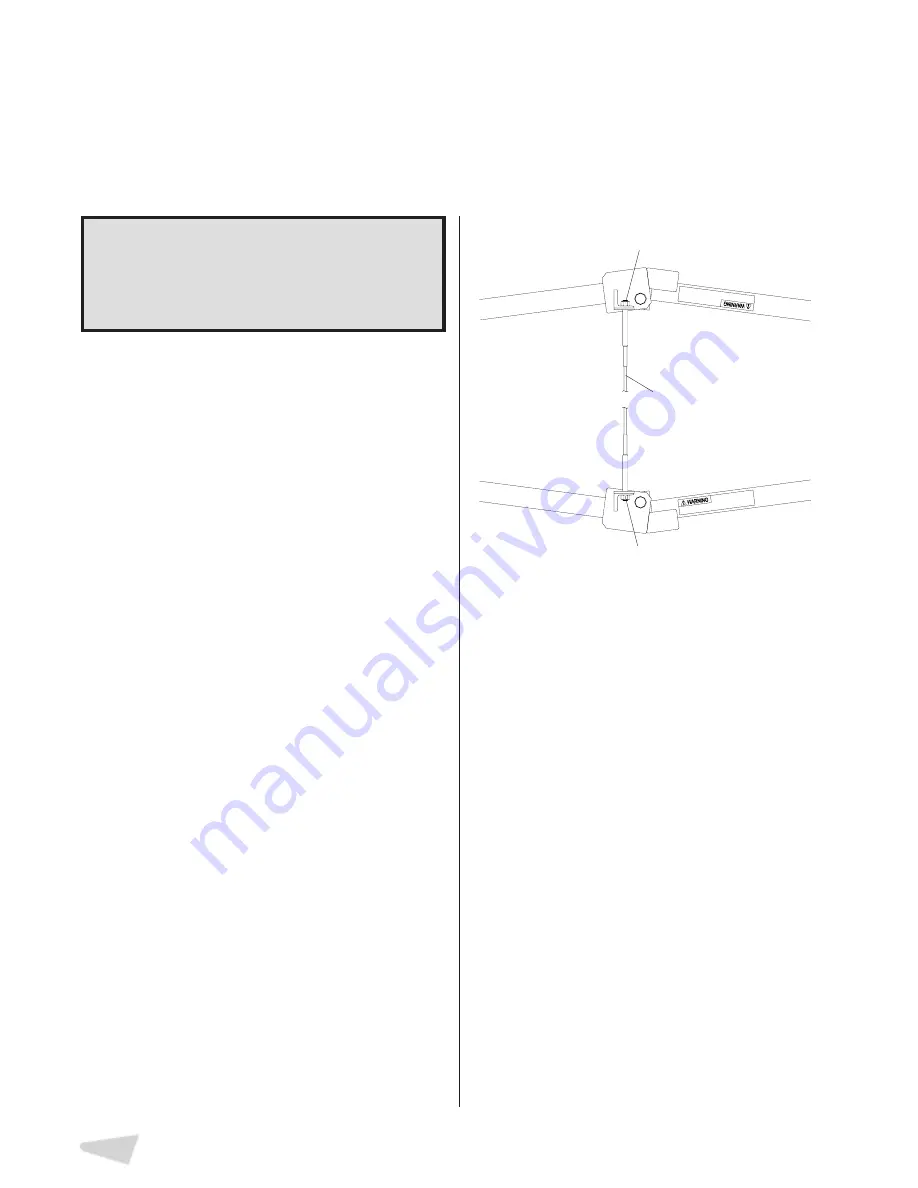
Safe-Stop
®
180 TMA
14
10) Install the Bottom Release Cable
across the Arm Assemblies.
Verify that the frame is extended as far as it will go. In-
stall the Bottom Release Cable across Arm Assemblies.
(see Figure 18). Torque the nuts to 34 Nm (25 ft-Ibf) mak-
ing sure that roughly an equal amount of threads pro-
trude from nuts on both ends of cable. Lock cable in place
using remaining fasteners as "jam" nuts.
WARNING!
For proper System performance, only use Release
Cables supplied by Energy Absorption Systems, Inc.
Failure to use the correct equipment could lead to
fatigue or result in poor System performance.
Figure 18
RELEASE CABLE
TORQUE TO 34 NM (25 FT-LBS.)
TORQUE TO 34 NM (25 FT-LBS.)
Installation Instructions (cont’
Installation Instructions (cont’
Installation Instructions (cont’
Installation Instructions (cont’
Installation Instructions (cont’d.)
d.)
d.)
d.)
d.)
Содержание Safe-Stop 180 TMA 9181
Страница 42: ...Safe Stop 180 TMA 42 ...
Страница 43: ...43 ...
Страница 46: ...Safe Stop 180 TMA 46 ...
Страница 47: ...47 ...