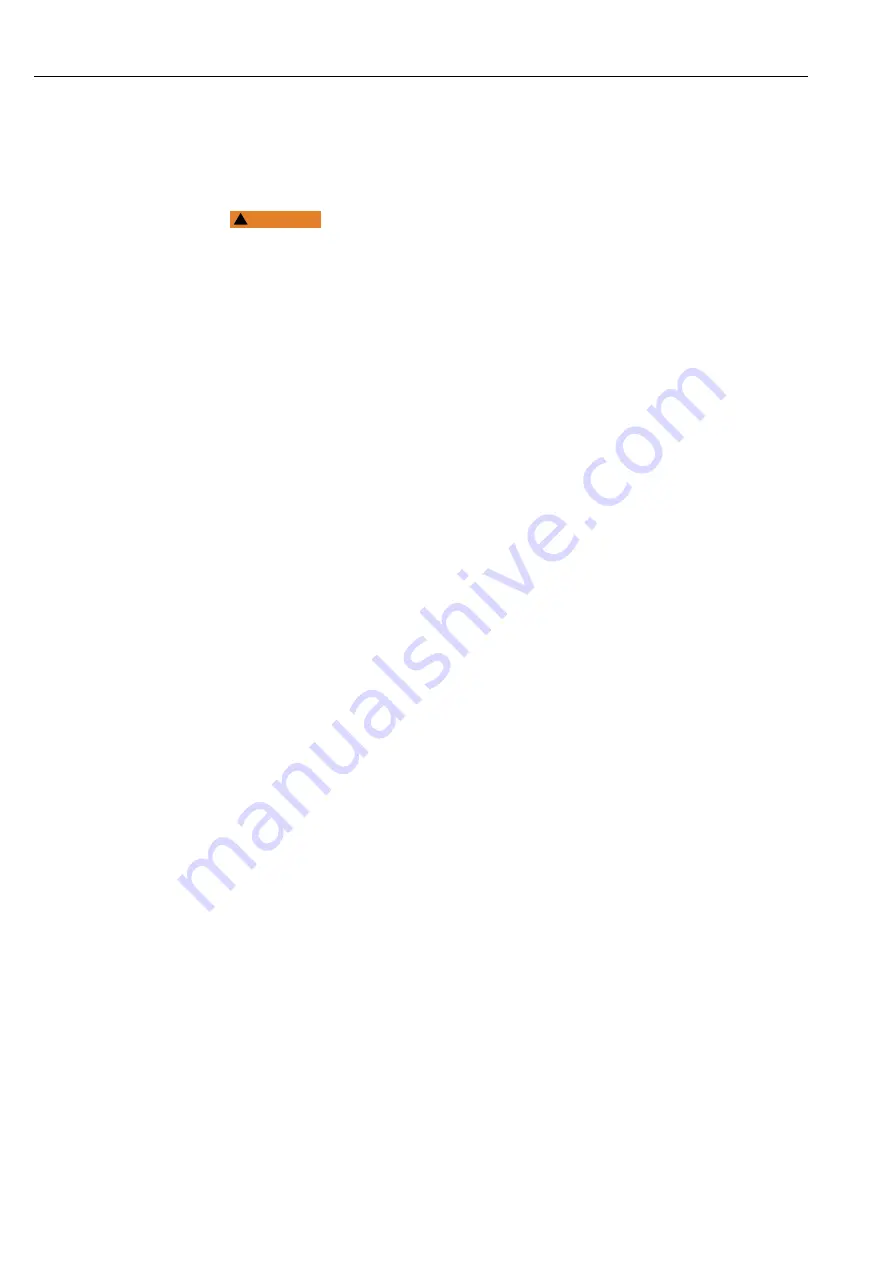
Repair
Cleanfit CPA875
34
Hauser
6
Repair
6.1
Replacing damaged components
WARNING
!
Danger resulting from improper repair
‣
Damage to the assembly, which compromises pressure safety, must be repaired
only
by
authorized and qualified personnel.
‣
Damage to the drive can be repaired only at the place of manufacture. Repairs cannot be
carried out onsite.
‣
Following each repair and maintenance task, the assembly must be checked for leaks
using appropriate procedures. Following this, the assembly must again comply with the
specifications in the technical data.
Replace all other damaged components immediately.
6.2
Spare parts kits
Detailed information on spare parts kits can be obtained using the "Spare Part Finding Tool"
on the internet: www.products.endress.com/spareparts_consumables
6.3
Return
The product must be returned if it is in need of repair or a factory calibration, or if the wrong
product was ordered or delivered. Legal specifications require Hauser, as an ISO-
certified company, to follow certain procedures when handling all returned products that
have been in contact with the medium.
To ensure that your device is returned swiftly, safely and in an appropriate manner,
please read the procedures and conditions on the Hauser website at
www.services.endress.com/return-material
6.4
Disposal
All assembly components must be disposed of separately, based on the material they are
made of.
Please observe local regulations.
Содержание Cleanfit CPA875
Страница 43: ...Cleanfit CPA875 Endress Hauser 43...
Страница 44: ...www addresses endress com 71237906...