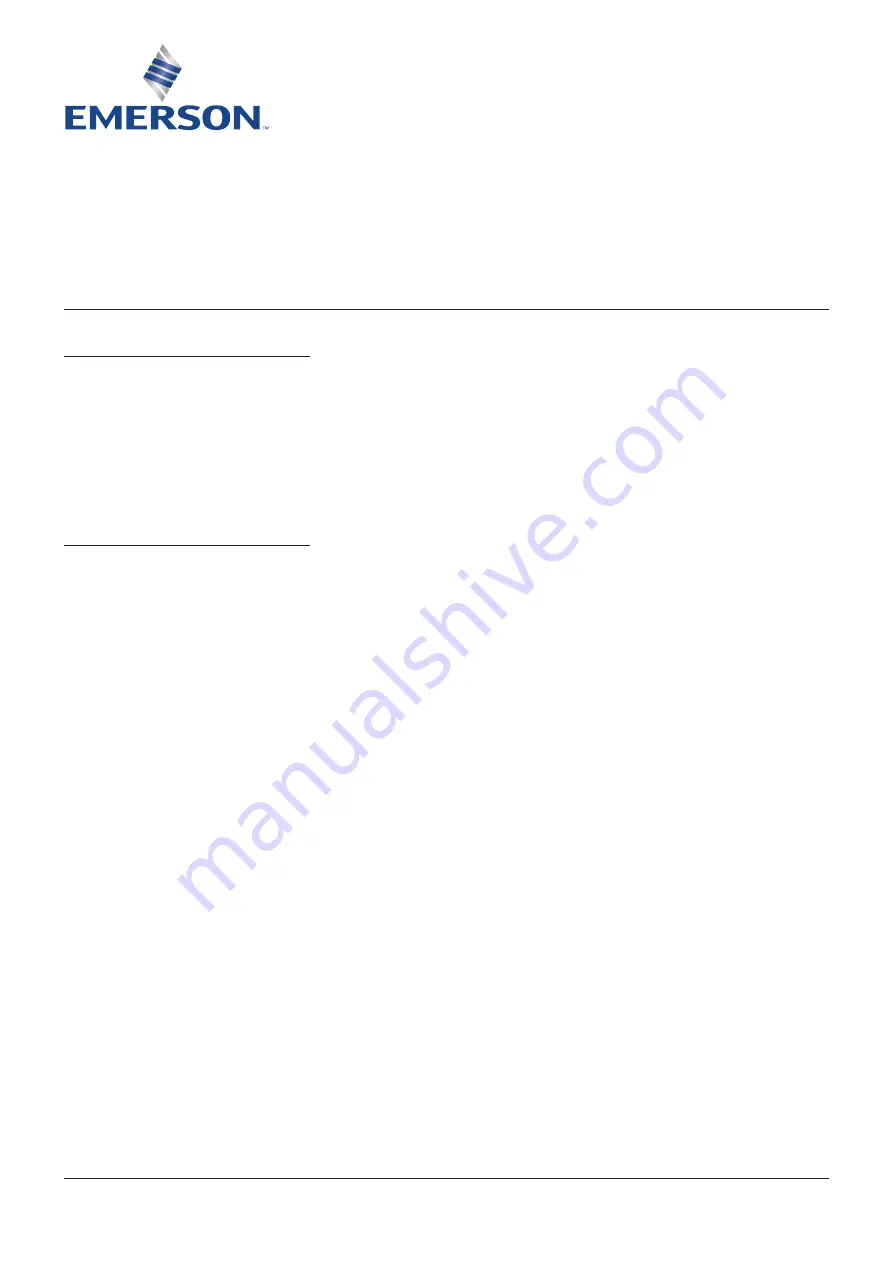
Sempell
Dewrance BleeD steam check valves
InstallatIon and maIntenance InstructIons
General
• this covers bled steam check valves fitted
with pneumatic actuator and external limit
switches.
• For spare parts, refer to sheet giving details
of classification. when ordering spare parts,
quote full product number stamped on
nameplate.
• refer to appendix 2 for specific product
numbers.
VCIOm-01422-en 15/05
Before installation these instructions must be fully read and understood
nr. D129
1 Safety nOtICe
Proper installation, operation and maintenance
are essential to the safe and reliable operation
of all valve products. the relevant procedures
recommended by Dewrance and described
in this manual, are effective methods of
performing the required tasks. some of these
procedures require the use of tools specifically
designed for an intended purpose. these
special tools should be used when, and as,
recommended.
It is important to note that this manual contains
various ‘safety messages’ which should be
carefully read in order to minimize the risk of
personal injury, or the possibility that improper
procedures will be followed which may damage
the involved Dewrance product, or render it
unsafe. It is also important to understand that
these ‘safety messages’ are not exhaustive.
Dewrance cannot possibly know, evaluate,
and advise any customer of all the conceivable
ways in which tasks might be performed, or
of the possible hazardous consequences of
each way. consequently, Dewrance has not
undertaken any such broad evaluation and,
thus, who uses a procedure and/or tool, which
is not recommended by Dewrance, or deviates
from Dewrance recommendations, must be
thoroughly satisfied that neither personal
safety, nor valve safety, will be jeopardised
by the method and/or tools selected. If not so
satisfied, contact Dewrance if there are any
questions relative to tools/methods. some
of the products manufactured by Dewrance
may be used in radioactive environments.
the installation, operation and maintenance
of valves and/or valve products may involve
proximity to fluids at extremely high pressure
and/or temperature. consequently, every
precaution should be taken to prevent injury
to personnel during the performance of any
procedure. these precautions should consist
of, but not limited to, ear drum protection, eye
protection and the use of protective clothing
(i.e. gloves etc.) when personnel are in or
around a valve work area. Due to the various
circumstances and conditions in which these
operations may be performed on Dewrance
products, and the possible hazardous
consequences of each way, Dewrance can
not possibly evaluate all conditions that might
injure personnel or equipment. nevertheless,
Dewrance does offer the safety precautions
listed on page 5 for customer information only.
It is the responsibility of the purchaser or user
of Dewrance valves/equipment to adequately
train all personnel who will be working with
the involved valves/equipment. Further,
prior to working with the involved valves/
equipment, personnel who are to perform
such work should become thoroughly familiar
with the contents of this manual. accordingly,
should any additional copies of this manual be
required, they can be purchased by contacting
Dewrance.
consequently, prior to starting any operation in
a radioactive environment, the proper “health
physics” procedures should be consulted and
followed, if applicable.
Emerson.com/FinalControl
© 2017 Emerson. All rights reserved.