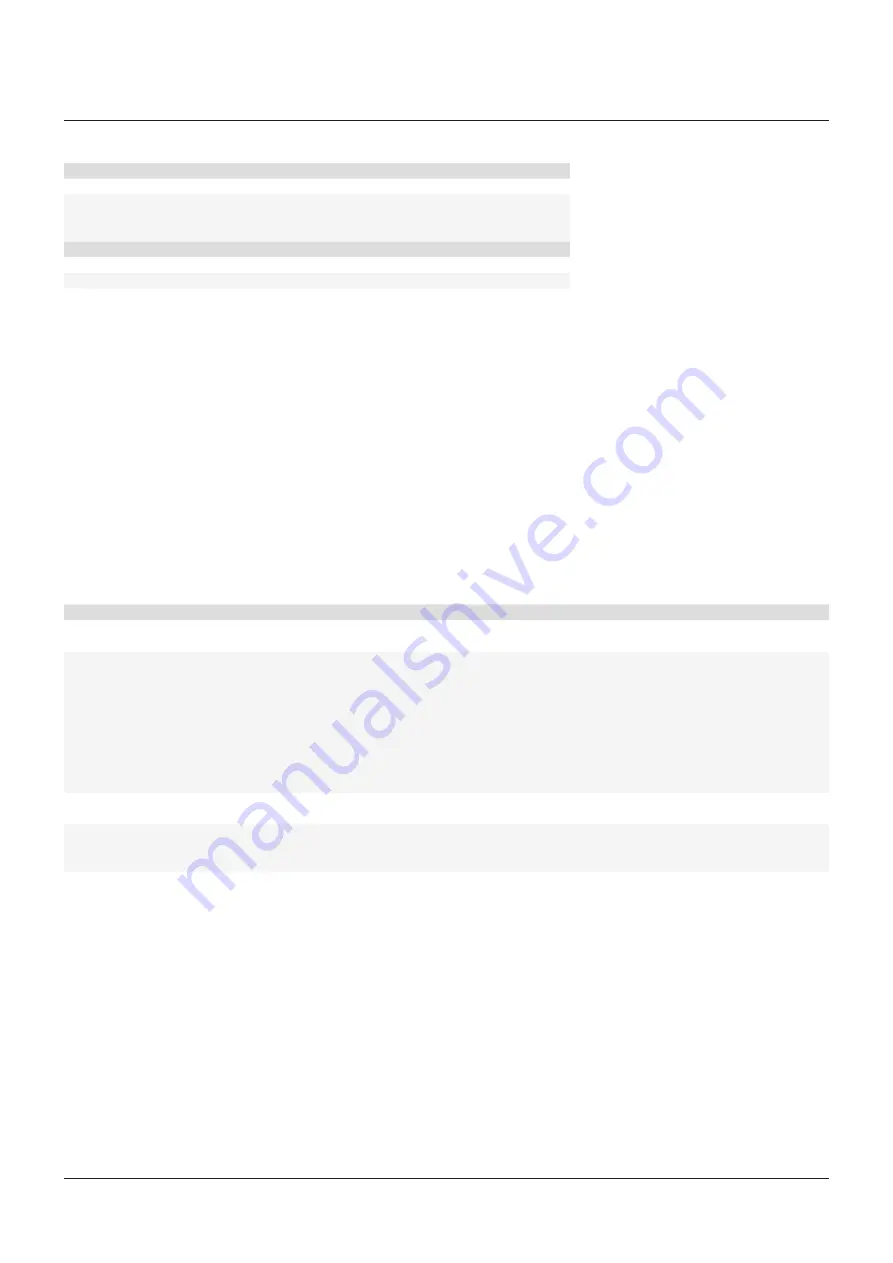
7
SEMPELL
SERIES S, TYPES SO, SC, SB, SOH FULL-LIFT SAFETY VALVES
OPERATING INSTRUCTIONS
3.10 FUNCTIONAL DIFFERENCES
Gases / Vapours:
Opening excess pressure
+5% p or 0.1 bar for p smaller than 3 bar
Closing excess pressure
-10% p or 0.3 bar for p smaller than 3 bar
By means of the adjusting ring (5) a closing pressure difference of -7% p
or 0.2 bar can be reached for p smaller than 2 bar.
Liquids:
Opening excess pressure
+10% p
Closing excess pressure
-20% p or 0.6 bar for p smaller than 3 bar
Change of the functional differences
(only valves with adjusting ring):
ATTENTION
Remove adjusting ring pin (6) only at reduced
pressure.
Push a screwdriver through the hole and adjust
the adjusting ring (5) groove by groove. One
notch pitch corresponds to about 0.2 mm of
change in height. The adjusting ring (5) has a
right-hand thread.
Turn adjusting ring (5) up = closing pressure
difference increases.
After the adjustment screw in adjusting ring
pin (6) again.
3.11 TROUBLE SHOOTING
Malfunction
Causes
Remedies
Safety valve opens at
different pressures.
1. Condensate in the supply line.
1. Improve insulation of line. Observe drain and slope.
2. Pressure change by superimposed vibration.
2. Suppress vibrations at the safety valve.
Safety valve opens and
closes in rapid succession.
1. Pressure loss in the supply line is greater than the closing
pressure difference.
1. Increase closing pressure difference. Otherwise reduce flow resistance
of the supply line: expand, shorten or remove area reductions.
Fast remedy: reduce lift (as far as allowed), thus reduce discharge.
2. Discharge quantity is too small because the subsequent
flow is too small.
2. Install smaller safety valve.
3. Admissible back pressure is exceeded in the exhaust line.
3. Decrease flow resistance of the exhaust line:
e.g. by expanding or shortening the line.
4. Dynamic pressure drop in the supply line,
especially in case of liquids.
4. Provide safety valve with a vibration damper.
Closing pressure
differences are too great.
1. Saturated steam with high moisture.
1. Install spring with a higher spring rate.
2. Adjusting ring (5) is set incorrectly.
2. See section 3.10
Safety valve remains open
after discharge test.
1. Foreign bodies between body seat and disc (3).
1. Open valve again by pressure increase or A 143. In case of valves with
lifting lever, lift and release it. Exhaust surge can blow off foreign
bodies. Otherwise disassemble valve.
Safety valve does not close
tightly.
1. Valve seat (2.1) damaged.
1. Disassemble valve. Rework valve seat (2.1), if necessary replace disc (3).
2. Difference between operating and set pressure is too small. 2. Enlarge difference (section 3.9).
3. Forming of the valve body caused by too great line forces.
3. Lay line elastically.
4. In case of liquids with high temperatures,
no slope in the line to the safety valve.
4. Assemble supply line with slope to the safety valve or as a siphon.