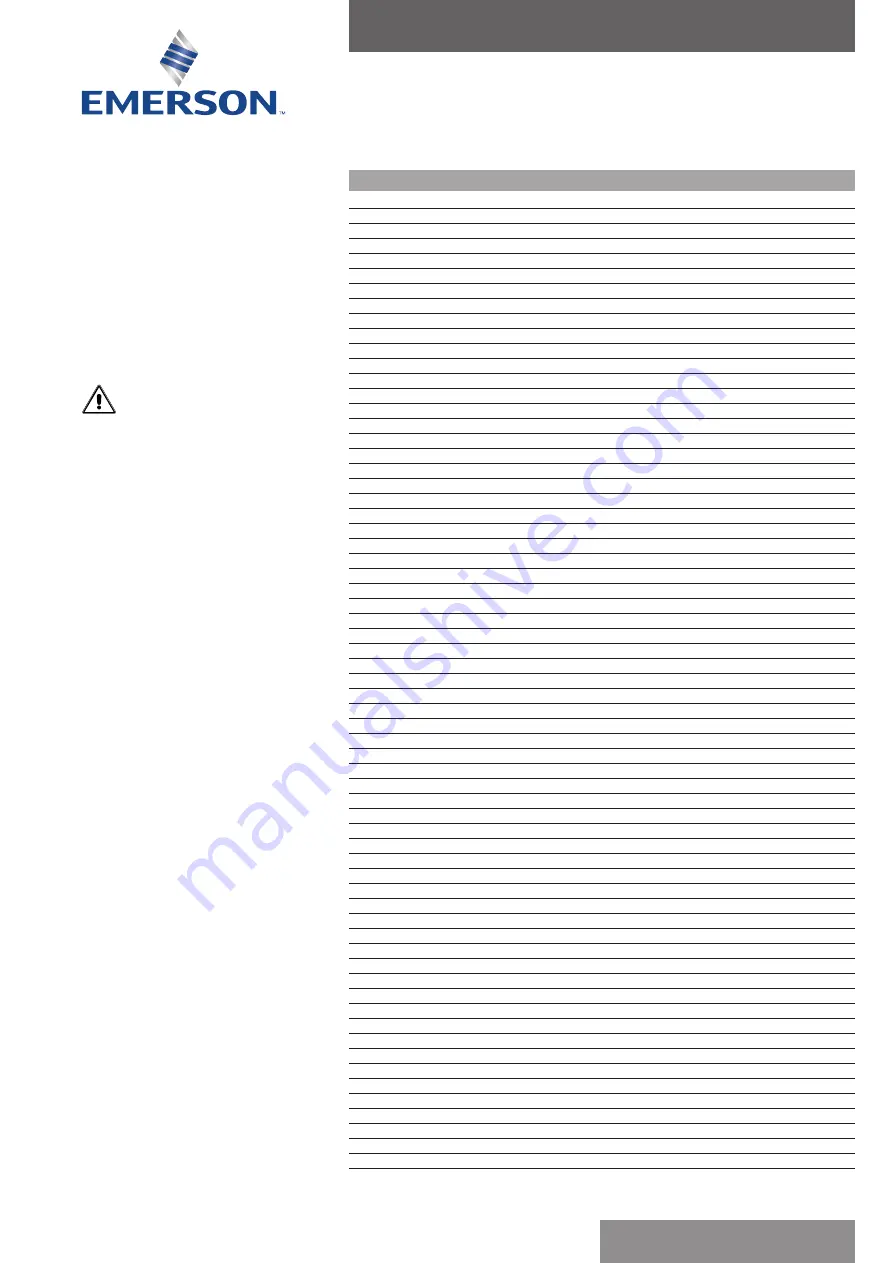
Sapag Safety Valves Series 8400/8500/8490/8590
Installation and Maintenance Instructions
without notice
SAPDR-0060-EN-1308
Table of Contents
1. Introduction
2. Storage and Handling
3. Installation
Care in Handling
Inspection
Inlet Piping
Outlet Piping
4. Hydrostatic Pressure Tests
Hydrostatic Test of Vessel or System
Hydrostatic Test of Outlet System
5. Setting, Testing and Adjustments
New Valves
Reconditioned Valves
Valves Removed from Service
The Test Bench
Test Fluids
Valve Operation
Set Pressure Changes
Set Pressure Adjustment
Nozzle Ring Settings
• Style 8500/8590
Cold Differential Test Pressure Adjustments
• Temperature Correction
• Back Pressure Correction
Seat Leakage Tests
• Metal-to-Metal Seated Valves
• Soft Seated Valves
6. Valve Maintenance
Visual Inspection and Neutralizing
Disassembly
Cleaning
Inspection
Reconditioning of Valve Seats
Lapping Procedures
• Lapping Blocks
• Lapping Compounds
• Machining of Nozzle Seats
• Machining of Disc Insert Seats
Assembly
Assembly of Cap and Lifting Lever Devices
Soft Seat Construction
7. Style Variations
8. Service Records
9. Spare Parts
10. Trouble Shooting Pressure Relief Valves
Seat Leakage
• Seats Damaged by Foreign Matter
• Distortion From Piping Strains
• Operating Pressure too close to Set Pressure
• Chatter
• Incorrectly Adjusting Lifting Gear
• Other Causes of Seat Leakage
• Corrosion
11. Emerson Valves & Controls’ Field Services and Repair Programs
Ordering Information
Attention
The safety of lives and property often
depends on the proper operation of the
pressure relief valves. Consequently, the
valves should be kept clean and should be
periodically tested and reconditioned to
make sure they function properly.
WARNING
Suitability of the material and product for
the use contemplated by the buyer is the
sole responsibility of the buyer. Also storage,
installation and proper use and application are
the sole responsibility of the purchaser.
Emerson
disclaims any and all liability arising
out of same.
Any installation, maintenance, adjustment,
repair and testing performed on pressure relief
valves should be done in accordance with
the requirements of all applicable Codes and
Standards under which those performing such
work should maintain proper authorization
through appropriate governing authorities.
No repair, assembly and test work done by
other than
Emerson
shall
be covered by the warranty extended by
Emerson
to its customers. You assume full
responsibility for your work. In maintaining
and repairing
Emerson
products you should use only parts
manufactured by
Emerson
. Call your nearest
Emerson
regional sales
office or representative for a
Emerson
service
engineer should you wish assistance with your
field needs.
SAPAG
Emerson.com/FinalControl
© 2017 Emerson. All rights reserved.