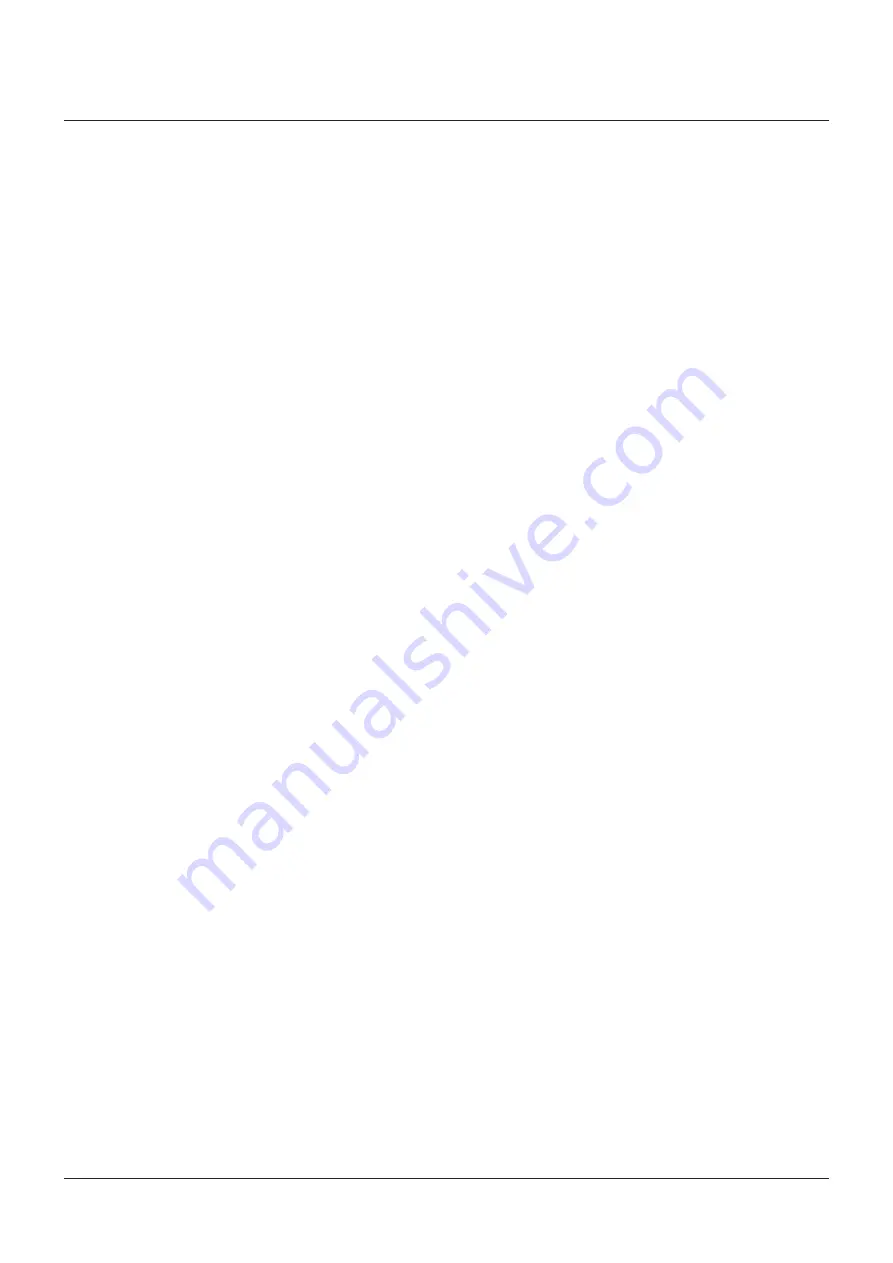
15
KTM
VIRGO SERIES N TRUNNION MOUNTED BALL VALVES
INSTALLATION, OPERATION AND MAINTENANCE INSTRUCTIONS
11.5 Series N trunnion mounted ball valve -
without gland
Construction: Two-piece
Type: External trunnion
Refer Section 11.5.3 for exploded view and
location of parts.
11.5.1 Disassembly procedure
1. Position the valve vertically by resting body
side end flange as shown in Figure 17.
2. Slowly remove the vent / drain plug (21) to
relieve any residual pressure from the body
cavity.
3. Remove fasteners (09) and ISO pad (07).
Remove fasteners (08) and housing (06).
Remove O-ring (14) and gasket (13 and 15)
from housing.
4. Remove key (19 and 20). Remove the stem
(04) from the housing. Remove O-ring from
housing. Remove bearing (22) from housing,
if it requires replacement due to wear /
tear / damage. Remove thrust washer (23)
from stem.
5. Remove trunnion (27) from body by
removing fasteners (32). Remove O-ring (30)
and gasket (31) from trunnion.
6. Disassemble the adapter (02) by removing
nuts (18). Where threaded “Puller Holes”
are provided on adapter flange, appropriate
fasteners can be used to gradually separate
the adapter from the body before lifting. This
can be done by screwing the fasteners in the
puller holes until they touch the body face
and thereby pulling adapter away from the
body. The size of the puller hole threading is
same as that of the fastener (09) size of body
to housing joint. Remove ‘O’-ring (10) and
gasket (11) from adapter. Use puller holes
provided on adapter for easy removal.
7. Remove the seat (05) from adapter. Remove
O-ring (16) from seat. Remove seat springs
(24) from adapter or seat.
8. Remove ball (03) and seat (05) from body.
Remove O-ring (16) from seat. Remove
seat springs (24) from body or seat.
Remove thrust washer (29) from ball.
Remove bearing (28) from ball, if it requires
replacement due to wear / tear / damage.
9. Where applicable, the sealant injection
fittings (25) may be removed for cleaning.
11.5.2 Re-assembly procedure
1. Ensure all parts are clean prior to assembly
of the valve.
2. Pay attention to references marked during
disassembly.
3. Position the body (01) vertically by resting
on end flange. Insert springs (24) in body or
seat (05). Mount O-rings / lip seals (16) as
applicable on seat and insert seat in body.
4. Assemble bearing (28) and thrust washer (29)
in ball pocket and place the ball (03) on body
side seat such that ball is in closed position.
5. Insert springs (24) in adapter (02) or
seat (05). Mount O-rings / lip seals (16)
as applicable on seat and insert seat in
adapter.
6. Place gasket (11) and O-ring (10) on adapter.
Place the adapter assembly on body.
Assemble lifting hooks (26) as applicable.
Tighten the nuts (18) in criss-cross pattern.
7. Assemble the trunnion (27) along with
O-ring / lip seal (30) and gasket (31) as
applicable on body with fasteners (32).
8. Place O-rings (12) and bearing (22) in
housing (06).
9. Insert stem (04) along with thrust washer
(23) in housing.
10. Assemble housing along with stem on body
using gasket (15), O-ring (14), fasteners (08)
and dowel (33).
11. Place gasket (13) between ISO pad (07)
and housing and assemble ISO pad using
fasteners (09) and dowel pins (34).
12. Assemble key (19 and 20) on stem.
13. Assemble drain / vent plug (21) as
applicable.
14. Assemble sealant injection fittings (25) as
applicable.