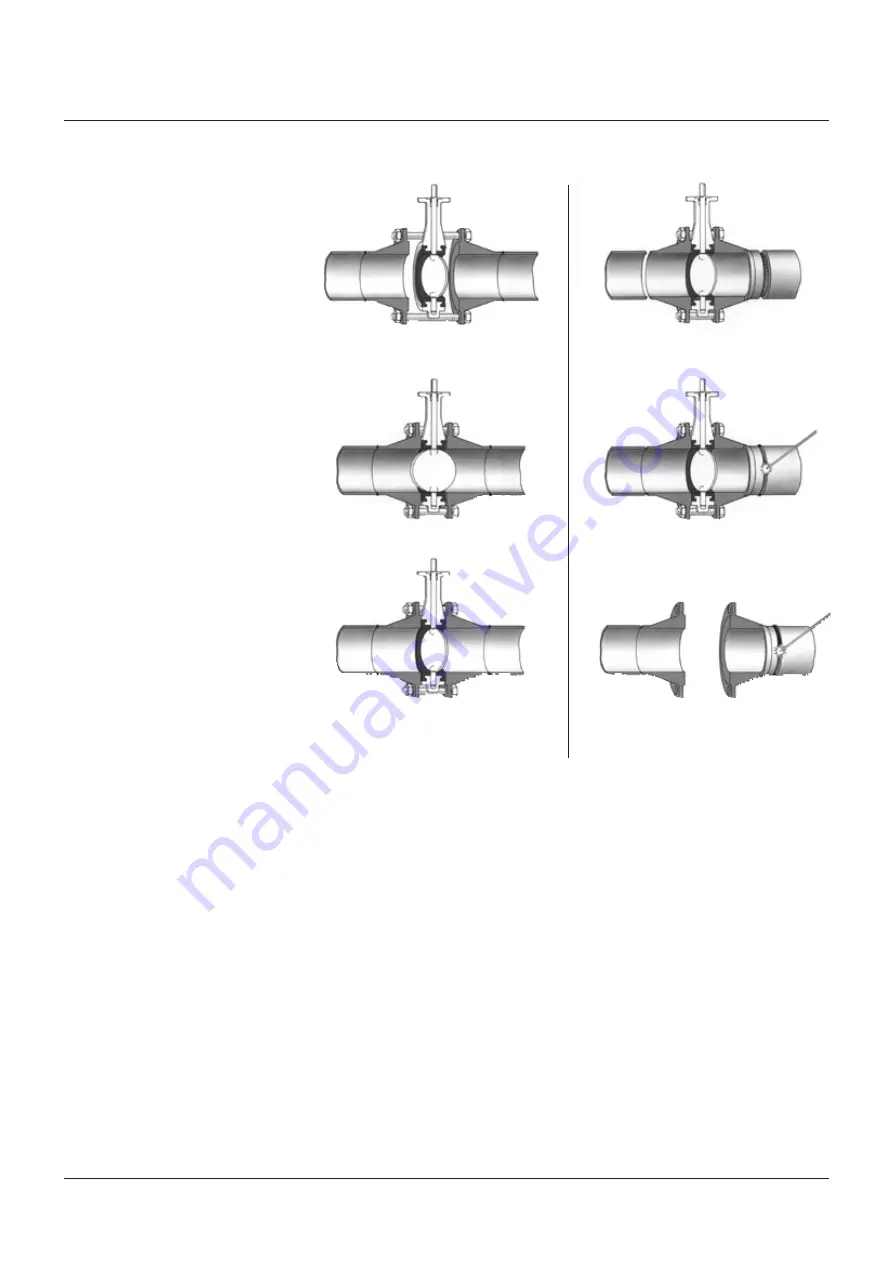
4
EXISTING SYSTEM
NEW SYSTEM
1. Spread the flanges with the adequate tooling.
Insert some flange bolts to hold the valve.
1. Center a flange-valve-flange assembly between
the pipes.
2. Open the valve and remove the flange spreads.
2. Tack weld the flanges to the pipes.
3. Close the valve clockwise, return to open position
and cross-tighten all bolting.
3. Remove the valve and finish weld.
Install the valve according to the procedure in the
left column.
KEYSTONE
SERIES 60 BUTTERFLY VALVES
INSTALLATION AND OPERATION MANUAL
FIGURE 2
3.5 Sources of possible danger
This section contains some examples of
possible foreseen danger sources.
3.5.1 Mechanical
A. When manual operators are used, available
space should be checked in order to avoid
hands being clamped.
B. Mechanical sparks caused on impact of
valve and e.g. tooling, are a potential source
of ignition of surrounding atmosphere.
3.5.2 Electrical
If static charges or stray electrical currents
can initiate explosions, the valve should be
grounded to earth.
3.5.3 Thermal
A. Isolation should be used on valves with
application temperatures > +40°C (+104°F)
and < -20°C (-4°F) to prevent them from
being touched (to avoid burning).
B. If the valve is used in hot gas/fluid
applications that might give exothermic
reactions, precautions must be taken so
that the valve surface cannot lead to danger
for people or the direct environment. In dust
and possible explosion zones, the operation
temperatures and ignition temperatures for
dust should be reviewed.
3.5.4 Operational
Closing a valve too fast may result in water
hammer in the upstream part of the pipeline.
Water hammer results in excessive stresses in
the valve and will cause severe damage.
Water hammer should be avoided in all
circumstances.
Due to differential pressure across the valve
disc, butterfly valves have the tendency to be
closed by the flow. Take care when unlatching
the valve operating mechanism.
Содержание KEYSTONE 60 Series
Страница 9: ... 2017 Emerson All rights reserved ...