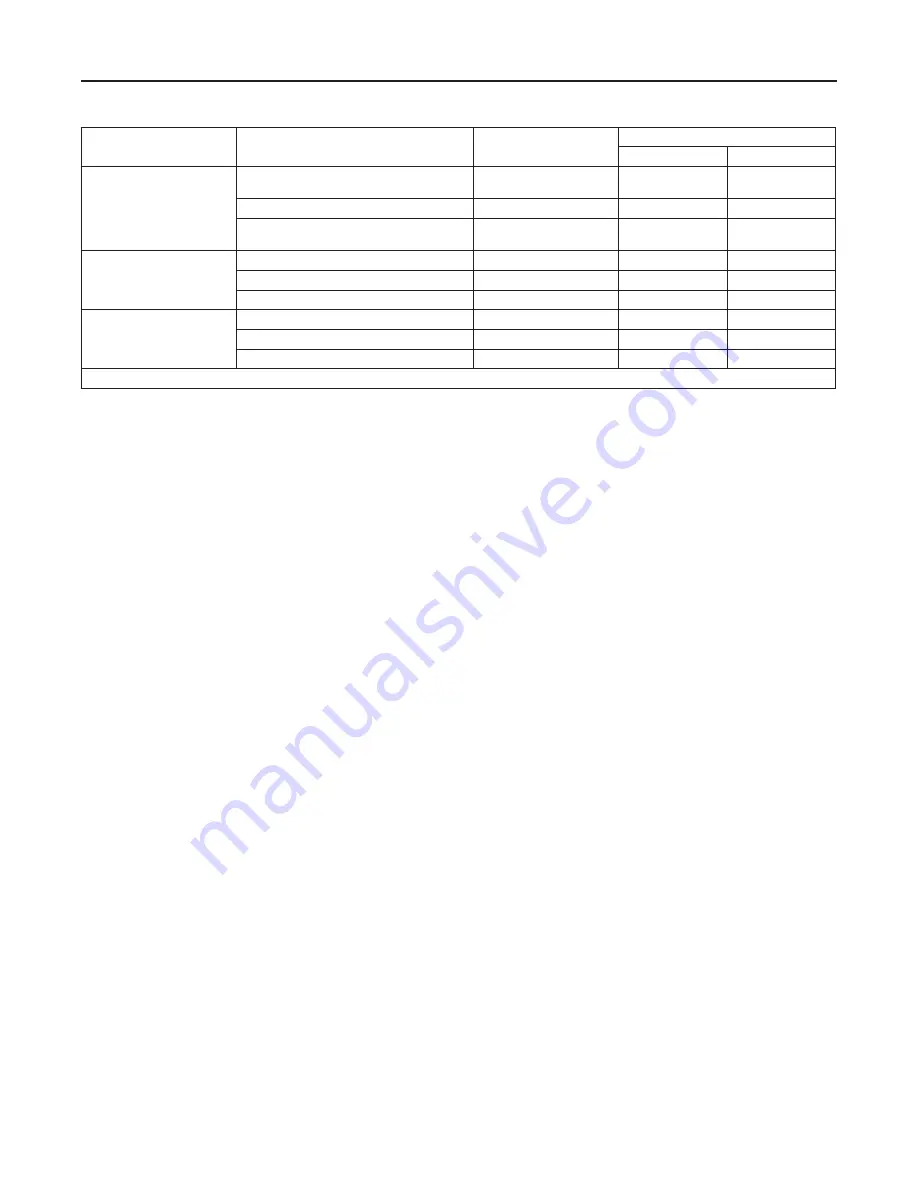
4. Loosen the nut (key 16) while holding wrench flats on plug
(key 3) to inspect internal wetted parts. Remove the lock
washer (key 24) and flat washer (key 23). The lower spring
seat (key 8), guide ring (key 9), diaphragm (key 7) and plug
O-ring (key 3) can now be removed from the plug (key 2). An
optional lower diaphragm plate (key 10) and O-ring (key 4)
are included for the constructions offering protection against
vacuum conditions.
5. Remove the plug (key 2) through the inlet port of the body
(key 1). Inspect parts for damage. Replace if damage is
noted. Refer to the section titled Soft Seat Maintenance
when the seat needs to be replaced.
6. Reassemble in the reverse order of the above procedure.
Start by inserting the plug (key 2) through the inlet port of
the body (key 1). The order is listed below or please refer to
Figure 3.
a.) Plug (key 2)
b.) Plug O-ring (key 3)
c.) Diaphragm plate (key 10) (vacuum protection
construction only)
d.) Diaphragm plate O-ring (key 4) (vacuum protection
construction only)
e.) Diaphragm gasket (key 6) (Metal diaphragms only)
f.) Diaphragm (key 7)
g.) Diaphragm gasket (key 6) (Metal diaphragms only)
h.) Guide ring assembly (keys 9 and 5)
i.) Lower spring seat (key 8)
j.) Flat Washer (key 23)
k.) Lock Washer (key 24)
l.) Hex Nut (key 16)
7. Hold wrench flats on plug (key 2), then torque hex nut
(key 16) to 6 to 8 in-lbs / 0.7 to 0.9 N•m for the 1/2 and
3/4 in. / 15 and 20 mm, 5 to 7 ft-lbs / 7 to 9 N•m for the
1 and 1-1/2 in. / 25 and 40 mm and 28 to 30 ft-lbs /
38 to 41 N•m for the 2 and 3 in. After tightening, apply
threadlocker medium/high strength sealant or equivalent to
the nut/thread interface.
8. Position diaphragm assembly in body (key 1). Replace
regulator spring (keys 12 and 13, when applicable) and
upper spring seat (key 11). Replace the spring case
(key 14) and sanitary clamp (key 15). Torque clamp
nuts to 20 to 22 ft-lbs / 27 to 30 N•m for the 1/2 through
1-1/2 in. / 15 through 40 mm and 38 to 40 ft-lbs / 52 to
54 N•m for the 2 and 3 in. / 50 and 80 mm.
Note
Lubricate the adjusting screw (key 18) threads
and the sanitary clamp bolt threads (key 15) to
reduce galling of the stainless steel. Factory
recommends anti-seize lubricant.
Keep even spacing between clamp halves
when tightening clamp nuts. This will ensure
even loading of the diaphragm. If clamp
halves touch, please contact factory for a
replacement clamp.
9. Install in pipeline and follow Startup and
Adjustment procedures.
Soft Seat Maintenance
Take care not to damage the internal/wetted surface finish when
performing Soft Seat Maintenance.
1. Disassemble the regulator as stated above.
2. To access soft seat (key 28), unscrew the lower plug
(key 27) from the upper plug (key 26). If damaged, replace
with new part. Apply Loctite 246 or equivalent to the male
threads before assembly. Proper torque for the assembly is
6 to 8 in-lbs / 0.7 to 0.9 N•m for the 1/2 and 3/4 in. / 15 and
20 mm; 8 to 10 in-lbs / 0.9 to 1.1 N•m for the 1 and 1-1/2 x
1 in. / 25 and 40 x 25 mm; and 5 to 7 ft-lbs / 7 to 9 N•m for
the 1-1/2 in. / 40 mm. Torque for 2 and 3 in. / 50 and 80 mm
is 23 to 25 ft-lbs / 31 to 34 N•m.
3. Reassemble as stated in the prior section.
Table 4.
Temperature Capabilities
SEAT TYPE
DIAPHRAGM MATERIAL
O-RING MATERIAL
TEMPERATURE RANGE
°F
°
C
Metal
(Stainless Steel)
Ethylene Propylene Diene (EPDM)/
Stainless Steel
EPDM
-20 to 275
-28 to 135
Stainless Steel
PTFE/Fluorocarbon (FKM)
(1)
20 to 400
-6 to 204
Polytetrafluoroethylene (PTFE)/
Fluorocarbon (FKM)
PTFE/Fluorocarbon (FKM)
20 to 400
-6 to 204
Soft
(Polytetrafluoroethylene
(PTFE)/Stainless Steel)
EPDM/Stainless Steel
EPDM
-20 to 150
-28 to 65
Stainless Steel
PTFE/Fluorocarbon (FKM)
(1)
20 to 150
-6 to 65
PTFE/Fluorocarbon (FKM)
PTFE/Fluorocarbon (FKM)
20 to 150
-6 to 65
Soft
(Polyether Ether Ketone
(PEEK)//Stainless Steel)
EPDM
EPDM
-20 to 275
-28 to 135
Stainless Steel
PTFE/Fluorocarbon (FKM)
(1)
20 to 400
-6 to 204
PTFE/Fluorocarbon (FKM)
PTFE/Fluorocarbon (FKM)
20 to 400
-6 to 204
1. O-ring material is PTFE for the 1/2 and 3/4 in. / 15 and 20 mm sizes. Temperature range is the same.
6
Type SR5