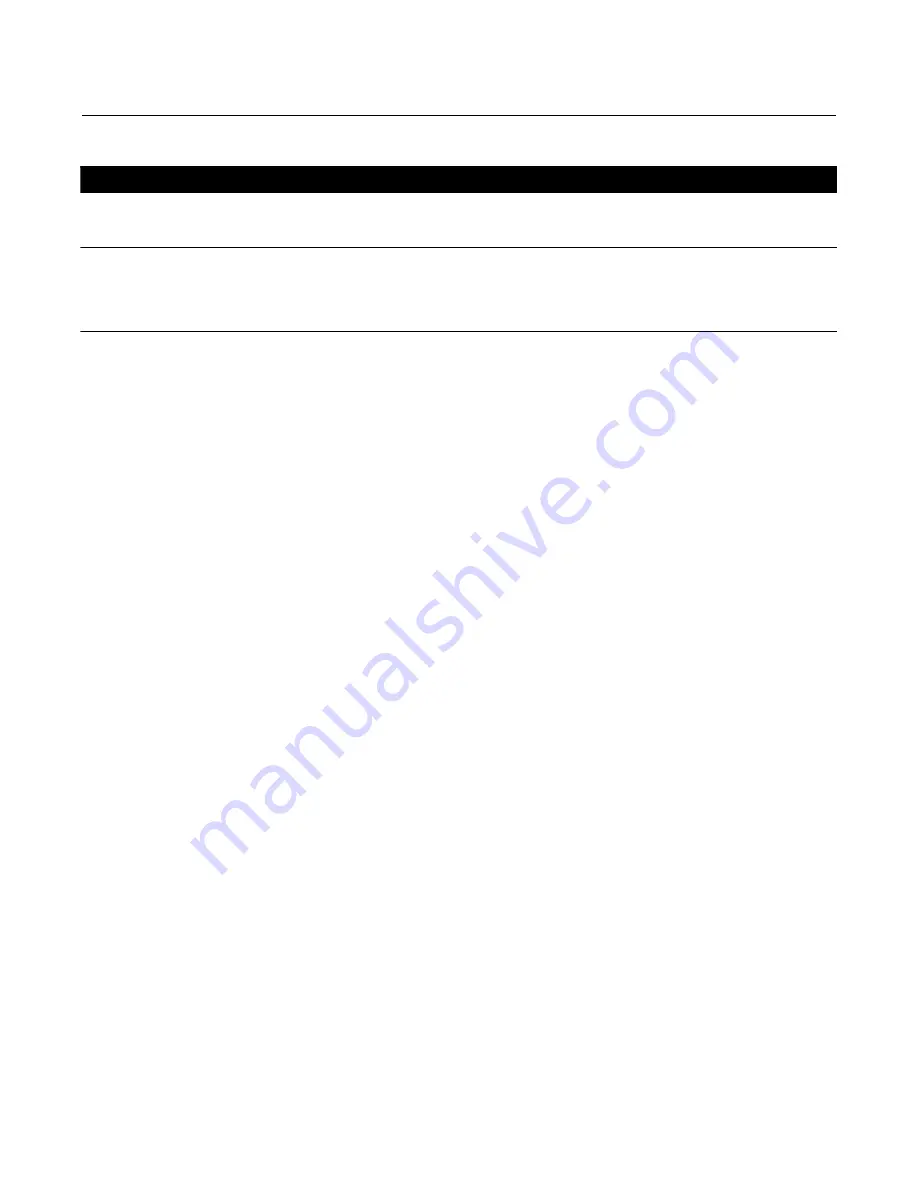
Instruction Manual
D102602X012
657NS Actuator
November 2012
14
CAUTION
Overtightening the diaphragm casing cap screws and nuts (keys 22 and 23) can damage the diaphragm. Do not exceed a
torque of 27 N
S
m (20 lbf
S
ft) when performing this tightening procedure.
Note
Do not use lubricant on these cap screws and nuts. Fasteners must be clean and dry.
7. Place the upper diaphragm casing (key 1) into position, and replace the diaphragm casing cap screws and nuts (keys
22 and 23). Tighten the hex nuts (key 23) in the following manner. The first four hex nuts tightened should be
diametrically opposed and 90 degrees apart. Tighten these four hex nuts to 13 N
S
m (10 lbf
S
ft).
8. Tighten the remaining hex nuts in a clockwise, crisscross pattern to 13 N
S
m (10 lbf
S
ft).
9. Repeat this procedure by tightening four hex nuts, diametrically opposed and 90 degrees apart, to a torque of 27
N
S
m (20 lbf
S
ft).
10. Tighten the remaining hex nuts in a clockwise, crisscross pattern to 27 N
S
m (20 lbf
S
ft).
11. After the last bolt is tightened to 27 N
S
m (20 lbf
S
ft), all of the bolts should be tightened again to 27 N
S
m (20 lbf
S
ft)
in a circular pattern around the bolt circle.
12. Once completed, no more tightening is recommended.
13. Thread the spring adjusting screw (key 12) into the yoke so that it is in the same position recorded during
disassembly. Securely tighten the locking set screw (key 67).
14. Replace the tubing or piping to the top of the upper diaphragm casing. Mount the actuator, and make the stem
connection by following the procedures in the Actuator Mounting section.
Size 80 Actuators
Key number references are shown in figure 4.
1. Place the lower diaphragm casing (key 5) on the actuator yoke (key 9), and secure them together with the cap
screws (key 8). Torque the screws evenly to 102 N
S
m (75 lbf
S
ft) using a crisscross pattern.
2. Carefully slide the upper diaphragm plate (key 48), the diaphragm (key 2), and the diaphragm plate (key 4) onto the
actuator stem (key 10). Thread the two hex nuts (key 49) lightly against the diaphragm plate. To aid in tightening
the hex nuts (key 49), attach the stem connector assembly (key 26) onto the actuator stem, and grip the stem
connector in a vise. Tighten the first hex nut (key 49) to approximately 542 N
S
m (400 lbf
S
ft) torque. Tighten the
second hex nut securely against the first. Remove the actuator stem subassembly from the vise, and remove the
stem connector assembly (key 26) from this subassembly.
3. Place the actuator stem and attached parts into the lower diaphragm casing (key 5). Prop the stem up so that the
diaphragm plates are positioned as shown in figure 4.
4. Lubricate the O-rings (keys 44 and 45) and the inside diameter of the seal bushing (key 46) with either a
high-temperature, radiation-resistant, polyphenyl ether grease or lithium grease, as appropriate for the installation.
Place the seal bushing and O-rings in the casing flange (key 51), and secure the bushing with the snap ring (key 47).
Place a new gasket (key 52) and then the casing flange (key 51) onto the upper diaphragm casing (key 1). Insert and
tighten the cap screws (key 8) to 102 N
S
m (75 lbf
S
ft) torque to secure the parts.
5. Align the diaphragm cap screw holes with the lower diaphragm casing cap screw holes. Slide the upper diaphragm
casing and casing flange (keys 1 and 51) over the actuator stem (key 10) and onto the lower diaphragm casing (key
5) so that all cap screw holes are aligned.