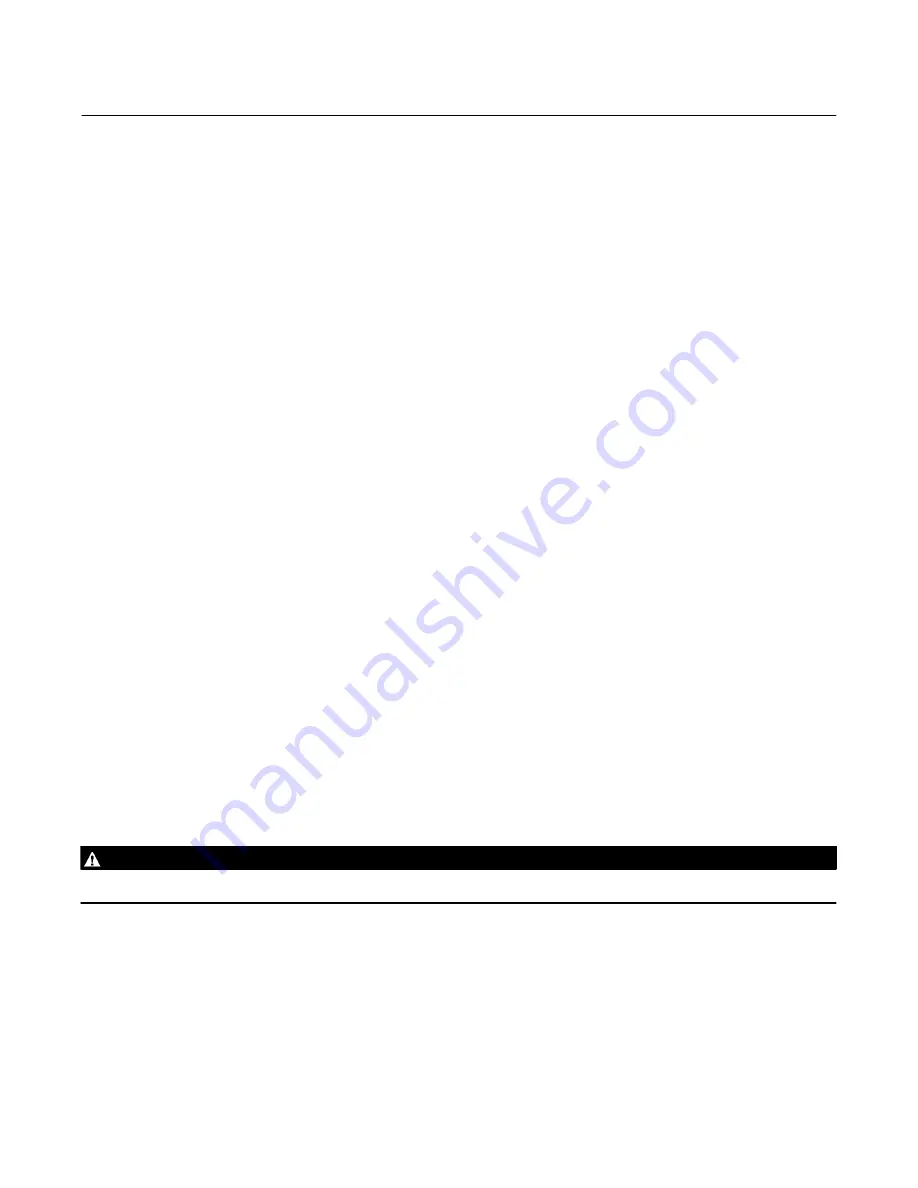
Instruction Manual
D200160X012
4195K Controllers
July 2018
99
1. Decrease the remote set point pressure to 0 percent of the remote set point input range.
2. The set point indicator should indicate the lower limit of the process scale span. If not, loosen the adjustment screw
on link A (key 116), and adjust the length so the set point indicator points to the lower limit of the process scale.
Tighten the screw.
3. Make fine zero adjustments by loosening the zero adjustment locking screw (key 102) and turning the zero
adjustment screw (key 108). Tighten the locking screw. Refer to figure 6‐23 for the screw locations.
4. Apply remote set point pressure equal to 100 percent of the remote set point input range.
5. The set point indicator should indicate the upper limit of the process scale span.
6. To increase the span, proceed as follows:
a. Turn the remote set point span adjustment screw clockwise.
b. To increase the span further than the adjustment screw allows, move both ends of link A (key 116) to the right.
c. Make fine adjustments with the remote set point span adjustment screw.
7. To decrease the span, proceed as follows:
a. Turn the remote set point span adjustment screw counterclockwise.
b. To decrease the span further than the adjustment screw allows, move both ends of link A (key 116) to the left.
c. Make fine adjustments with the remote set point span adjustment screw.
8. Repeat the adjustments until the upper and lower indications are aligned with the upper and lower limits on the
process scale.
9. Adjust the remote set point pressure for 50 percent of the remote set point input range.
10. The set point indicator should indicate mid‐scale
±
2 percent of the process scale span. If the error is within
±
2
percent, proceed to step 11. If the error is greater than
±
2 percent of the scale span, proceed to the remote set
point linearity adjustment procedure.
11. Adjust the set point indicator to mid‐scale
±
1 percent of the process scale span by loosening the zero adjustment
locking screw and turning the zero adjustment screw. Tighten the locking screw.
12. Adjust the remote set point pressure to the upper and lower limits of the remote set point input range and make
sure the set point indicator is still within
±
1 percent at the lower and upper limits of the process scale.
13. Perform the appropriate flapper alignment procedure and, if necessary, the process indicator zero and span
calibration procedure in Section 3, 4, or 5.
Remote Set Point Linearity Adjustment
WARNING
Refer to the Maintenance WARNING on page 51.
Adjust the linearity by loosening and repositioning the linearity adjustment screw in the curved slot on the lever arm of
pivot assembly B (key 115). Adjusting the linearity affects the zero and span adjustment.
1. Adjust the remote set point pressure to 50 percent of the remote set point input range. The set point indicator
should indicate mid‐scale
±
1 percent of the process scale span. If not, make fine adjustments by loosening the zero
adjustment locking screw and turning the zero adjustment screw.
2. Adjust the remote set point pressure to 0 percent of the remote set point input range and note the indicator
position relative to the process scale lower limit.