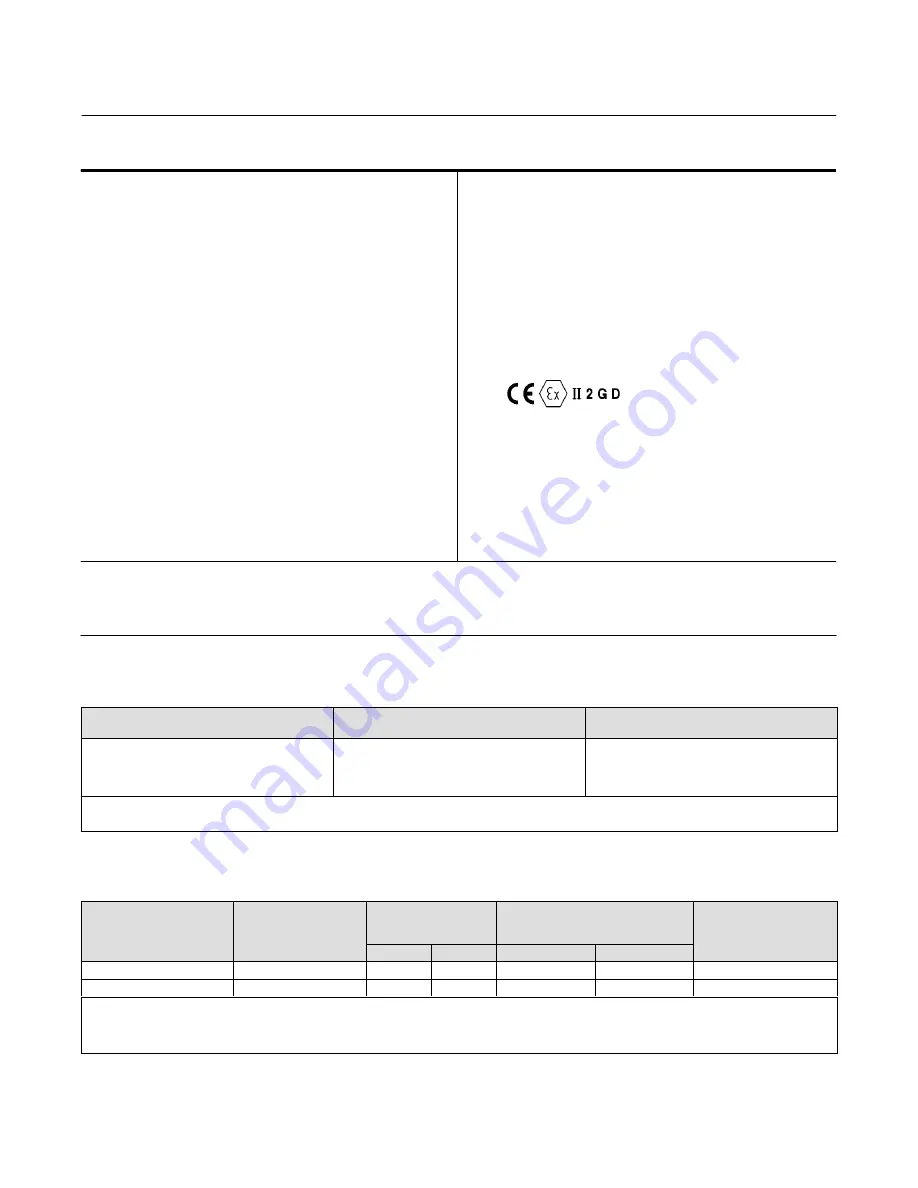
Instruction Manual
D200124X012
2500 and 2503 Controllers/Transmitters
June 2017
4
Table 1. Specifications (Continued)
Performance
Independent Linearity (transmitters only):
1% of
output pressure change for 100% span.
Hysteresis:
0.6% of output pressure change at 100%
proportional band, differential gap, or span
Repeatability:
0.2% of displacer length or
displacement force change
Deadband (except differential gap controllers
):
0.05% of proportional band or span
Typical Frequency Response:
4 Hz and 90 degree
phase shift at 100% proportional band with output
piped to typical instrument bellows using 6.1 meters
(20 feet) of 1/4‐inch tubing
Ambient Operating Temperature Limits
For ambient temperature ranges and guidelines for
use of the optional heat insulator assembly, see figure
2. Relay temperature limits are:
Standard Construction:
‐40 to 71
_
C
(‐40 to 160
_
F)
High‐Temperature Construction:
‐18 to 104
_
C
(0 to 220
_
F)
Typical Ambient Temperature Operating Influence
Output pressure changes
1.5% per 10
_
C (50
_
F)
change in temperature at 100% proportional band
when using a standard wall torque tube with 249
sensors
Hazardous Area Classification
2500 and 2503 controllers/transmitters comply with
the requirements of ATEX Group II Category 2 Gas
and Dust
Supply and Output Connections
1/4 NPT internal
Maximum Working Pressure (sensors only)
Refer to the appropriate sensor instruction manual
NOTE: Specialized instrument terms are defined in ANSI/ISA Standard 51.1 -
Process Instrument Terminology.
1. Controllers are field adjustable between direct or reverse action. The letter R in the type number indicates that the controller/transmitter shipped from the factory set for reverse action (see chang
ing controller action procedures). The letter C in the type number indicates that a pointer is attached to the torque tube shaft providing visual monitoring of torque tube motion.
2. Control and stability may be impaired if the maximum pressures are exceeded.
3. The pressure/temperature limits in this document, and any applicable standard or code limitation should not be exceeded.
4. These statements apply only to units sized to produce a full output change for a 100% level change at the maximum proportional band dial setting.
5. Adjusting the span of the differential gap controller is equivalent to adjusting the deadband.
Table 2. Standard Displacer Volumes
Sensor
Standard Volume
Liters
Standard Volume
Cubic Inches
249, 249B, 249BF, 249BP, 249K, 249P, 249W
249C, 249CP, 249W
249L
249VS
1.6
1.0
1.9
1.3
100
60
120
80
1. For 249W, with standard 812 mm (32‐inch) displacer.
2. For 249W, with standard 356 mm (14‐inch) displacer.
3. With standard 305 mm (12‐inch) flange‐face‐to‐displacer centerline dimension only.
Table 3. Supply Pressure Data
OUTPUT SIGNAL RANGE
STANDARD SUPPLY AND
OUTPUT
PRESSURE GAUGE
INDICATIONS
NORMAL OPERATING
SUPPLY PRESSURE
AIR CONSUMPTION AT
NORMAL OPERATING
SUPPLY PRESSURE
MAXIMUM
SUPPLY PRESSURE
Bar
Psig
Minimum
Maximum
0.2 to 1 bar (3 to 15 psig)
0 to 30 psig
1.4
20
4.2 scfh
27 scfh
3 bar (45 psig)
0.4 to 2 bar (6 to 30 psig)
0 to 60 psig
2.4
35
7 scfh
42 scfh
3 bar (45 psig)
1. Consult your Emerson Automation Solutions sales office about gauges in other units.
2. Control and stability may be impaired if this pressure is exceeded.
3. At zero or maximum proportional band or specific gravity setting.
4. At setting in middle of proportional band or specific gravity range.
5. If air consumption is desired in normal m
3
/hr at 0
_
C and 1.01325 bar, multiply scfh by 0.0258.