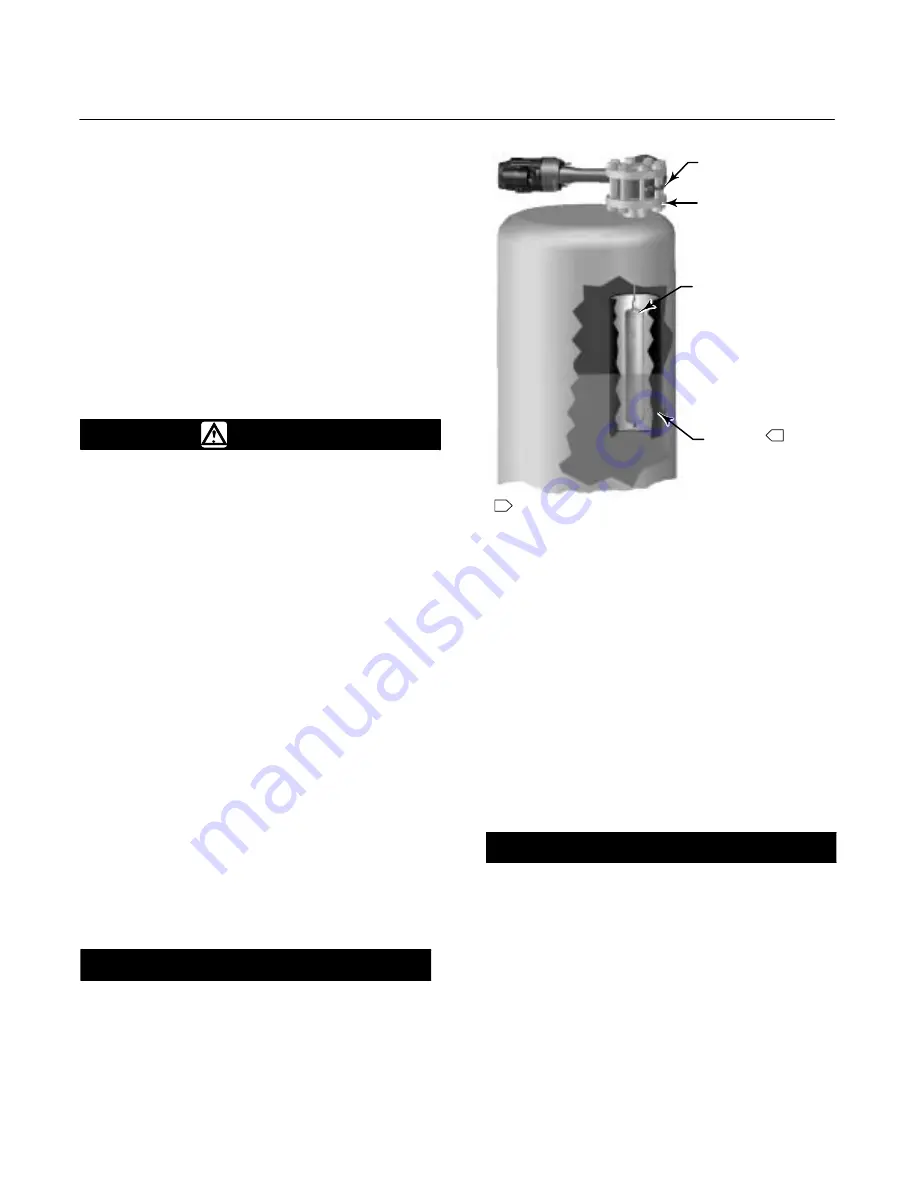
249W Level Sensor
Instruction Manual
Form 5729
March 2005
3
Type Number Description
D
Type 249W—3- or 4-inch, ANSI Class 150,
300, 600 steel cageless sensor.
The Parts List section shows some Type 249W
constructions, standard displacer lengths, and
standard materials. However, Type 249W parts are
available in a wide variety of materials of
construction, part dimensions, and other
specifications. Contact your Fisher sales office for
assistance in selection of specific materials,
dimensions, and specifications.
Installation
WARNING
To avoid personal injury or property
damage resulting from the sudden
release of pressure:
D
Always wear protective clothing
and eyewear when performing any
installation operations to avoid
personal injury.
D
Check with your process or safety
engineer for any additional measures
that must be taken to protect against
process media.
D
If installing into an existing
application, also refer to the WARNING
at the beginning of the Maintenance
section of this instruction manual.
The Type 249W sensor can be installed directly on
the vessel as shown in figure 4. It also can be
installed in a user fabricated cage mounted on the
side of the vessel as shown in figure 5. The sensor
mounts on the top of the vessel or in the displacer
cage using a 3-inch raised face flange with the
3-inch 249W wafer body, or a 4-inch raised-face
flange with the 4-inch 249W wafer body.
Installation on Top of Vessel
CAUTION
If a stillwell is used, install it plumb so
that the displacer does not touch the
wall of the stillwell. If the displacer
touches the wall, the unit will transmit
an erroneous output signal.
Figure 4. Type 249W Sensor Top Mounted on Vessel
TYPE 249W WAFER BODY
3- OR 4 - INCH
RF FLANGE
DISPLACER
STILLWELL
1
1
NOTE:
STILLWELL REQUIRED AROUND DISPLACER IF THE FLUID
IS IN A STATE OF CONTINUOUS AGITATION
W8266 / IL
Because the displacer hangs inside the vessel,
provide a stillwell around the displacer if the fluid is
in a state of continuous agitation to avoid excessive
turbulence around the displacer.
To attach the sensor body to the vessel requires a
flanged connection on the vessel as shown in figure
4. For interface or fluid level applications, install a
gauge glass on the vessel.
Installation with Displacer Cage on
Side of Vessel
CAUTION
Install the cage so that it is plumb; the
displacer must not touch the cage
wall. If the displacer touches the cage
wall, the unit will transmit an
erroneous output signal.
Figure 5 shows the Type 249W sensor mounted on
the side of a vessel using a displacer cage. Figures
6, 7, 8, and 9 provide the Type 249W dimensions
required to fabricate a cage. Figure 10 provides
overall envelope dimensions for Type 249W sensor
and DLC3010 controller.