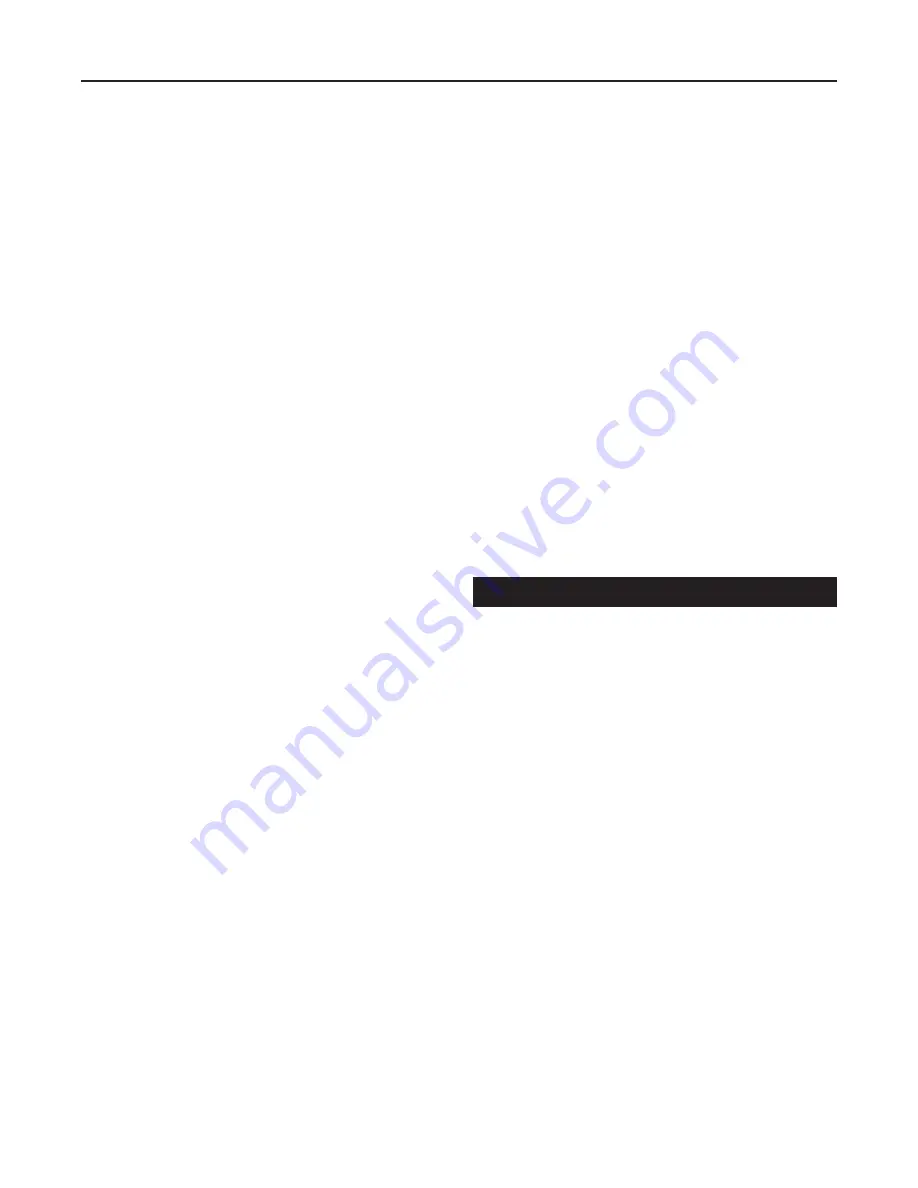
11
EN-DFA Series
North America
Only
2. Carefully remove the element assembly from the
arrestor. Place the element assembly on a soft
surface such as plywood and push the flame cells
from the housing. It might be necessary to tilt the
housing to facilitate removal of the flame cells.
3.
Note the order in which the flame cells were
removed. For Group IIA units, there are four 2 in. /
51 mm thick flame cells. For Group IIB3 units, the
outer two flame cells are 2 in. / 51 mm thick and
the two inner flame cells are 1 in. / 25 mm thick. A
screen of expanded metal is located between each
adjacent set of flame cells.
4.
Inspect the flame cells and the screens visually
for any signs of corrosion or other damage and
inspect the flame cells with a calibrated pin gauge
to ensure maximum crimp size openings do not
exceed the following values for their respective
gas group:
• Explosion Group IIA – 0.051 in. / 1.295 mm
• Explosion Group IIB3 – 0.0216 in. / 0.549 mm
5. If any damage is noted or crimp openings exceed
maximum size allowable, the flame cells and/or
the screens must be replaced.
Note
Under no circumstance shall any other
screens not provided by Emerson be used
in this assembly. Failure to use the correct
screens may lead to arrestor failure.
6. It is important to keep the element openings clean
to prevent loss of efficiency in absorbing heat. The
element assembly should be removed and the
elements cleaned to prevent the openings from
becoming clogged with particulate matter or other
contaminants. Clean the element with a suitable
cleaning media (solvent, soap, water or steam)
then blow dry using compressed air. Special care
should be taken not to damage or dent the cell
openings as this would hamper the effectiveness
of the unit. Arrestor elements shall not be cleaned
by rodding with wire or other hard objects to
remove blockages, as this practice could damage
the elements and seriously impair the arrestor’s
performance. If the arrestor element cannot be
cleaned satisfactorily, it must be replaced.
7. For best cleaning results, a high pressure sprayer
with spray wand should be used (1500 to 3000 psig /
103 to 207 bar) to clean the entire element surface.
The spray nozzle should be held perpendicular to
the surface being cleaned to maximize spray media
penetration into the element. Alternately spray each
side of the element surface until clean.
8. The cleaning interval should be governed by the
amount and type of particulate in the system to
which it is installed and must be determined by
the user. To determine the maintenance interval
the user should check the element in the first few
months of operation to find how quickly particulate
accumulates in the cells.
9.
Thoroughly clean the gasket sealing faces being
careful not to damage the sealing surface. For
reassembly a new gasket must be used and
placed in the machined recess of each interior
flange on the two conical sections.
10.
Replace the flame element assembly with a new
assembly or properly cleaned and inspected
existing unit.
11.
Locate the flame cell assembly such that it seats
onto the gaskets.
12. Replace all tensioning studs and tighten the outer
nuts hand tight only.
13.
Torque the bolts in sequence as shown in the
following instructions.
Torquing Instructions
△
CAUTION
Excessive or uneven torque can cause
permanent damage to gaskets
and housing.
Tools/Supplies Required
•
Hand operated conventional torque wrench or
power assisted torque wrench appropriate for the
specified torque.
•
Socket wrenches of the proper size to fit the hex
nuts being tightened.
• Lubricant for fasteners, as appropriate.
• Brush suitable for applying lubricant to the studs.
•
Wiping rags necessary for the clean up of
excessive lubricant.
Procedure
1. Use studs and nuts that are free of visible
contamination and corrosion.
2. Apply lubricant to the threads of the stud protruding
outboard of the interior flanges and to the face of the
hex nuts which will contact the flange for stainless
steel fasteners. Alloy steel fasteners have a polymer
coating and do not require additional lubrication.