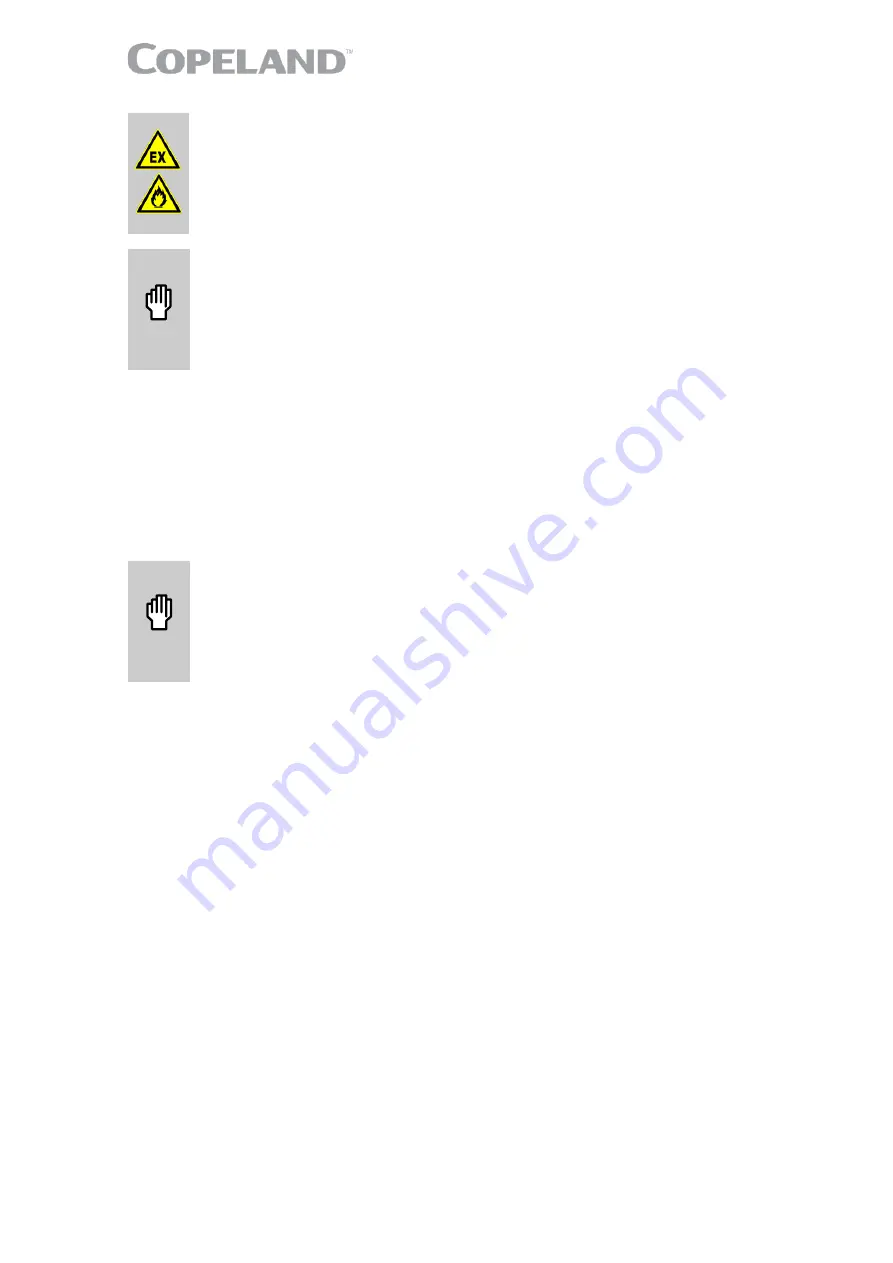
26
AGL_AC_ST_YRH_EN_Rev01
6.4 Exchanging the refrigerant
WARNING
Air/flammable refrigerant mixture in a potentially flammable or explosive
atmosphere! Fire and explosion hazard!
In any case avoid air/A2L or A3
mixture in the refrigeration system. Make sure that the system is filled with
pure A2L or A3 refrigerant. In the event that the refrigerant needs replacing,
the charge should be recovered using A2L- or A3-qualified refrigerant
recovery unit and recycling bottles.
CAUTION
Low suction pressure operation! Compressor damage!
Do not operate
with a restricted suction. Do not operate with the low-pressure limiter bridged.
Do not operate compressor at pressures that are not allowed by the operating
envelope. Allowing the suction pressure to drop below the envelope limit for
more than a few seconds may overheat scrolls and cause early drive bearing
and moving parts damage.
For qualified refrigerants and oils, see
section 2.5.1 "Qualified refrigerants and oils"
.
It is not necessary to replace the refrigerant unless contamination, for example due to an error such
as topping up the system with a non-condensable gas or incorrect refrigerant, is suspected. To verify
correct refrigerant composition, a sample can be taken for chemical analysis. A check can be made
during shutdown by comparing the refrigerant temperature and pressure using precision
measurements at a location in the system where liquid and vapour phases are present and when the
temperatures have stabilised.
6.5 Replacing a compressor
CAUTION
Inadequate lubrication! Bearing destruction!
For systems with a refrigerant
accumulator, exchange the accumulator after replacing a compressor with a
burned-out motor. The accumulator oil return orifice or screen may be plugged
with debris or may become plugged. This will result in starvation of oil to the
new compressor and a second failure.
Remove refrigerant and oil completely from the replaced compressor.
6.5.1 Compressor replacement
If an A2L- or A3-refrigerant compressor is to be replaced, the oil has to be drained out of the
compressor and the compressor should be flushed with dry nitrogen. DO NOT close the stubs with
plugs.
In case of motor burnout, the majority of the contaminated oil will be removed with the compressor.
The rest of the oil is cleaned through the use of suction and liquid line filter-dryers. A 100 % activated
alumina suction line filter-dryer is recommended but must be removed after 72 hours. When a
compressor is exchanged in the field, a major portion of the oil may still be present in the system.
While this will not affect the reliability of the replacement compressor, the extra oil will add to rotor
drag and increase power usage.
6.5.2 Start-up of a new or replacement compressor
Rapid charging only on the suction side of a scroll-equipped system can occasionally result in a
temporary no-start condition for the compressor. The reason for this is that, if the flanks of the scrolls
happen to be in a sealed position, rapid pressurisation of the low side without opposing high-side
pressure can cause the scrolls to seal axially. As a result, until the pressures eventually equalise,
the scrolls can be held tightly together preventing rotation. The best way to avoid this situation is to
charge on both the high and low sides simultaneously at a rate which does not result in axial loading
of the scrolls.
A minimum suction pressure specified in the published operating envelope must be maintained
during charging. Allowing the suction pressure to drop below that value may overheat the scrolls and
cause early drive bearing and moving parts damage. Never install a system in the field and leave it
unattended when it has no charge, a holding charge, or with the service valves closed without
securely electrically locking out the system. This will prevent unauthorised personnel from
accidentally operating the system and potentially ruining the compressor by operating with no
refrigerant.
Do not start the compressor while the system is in a deep vacuum.
Internal arcing