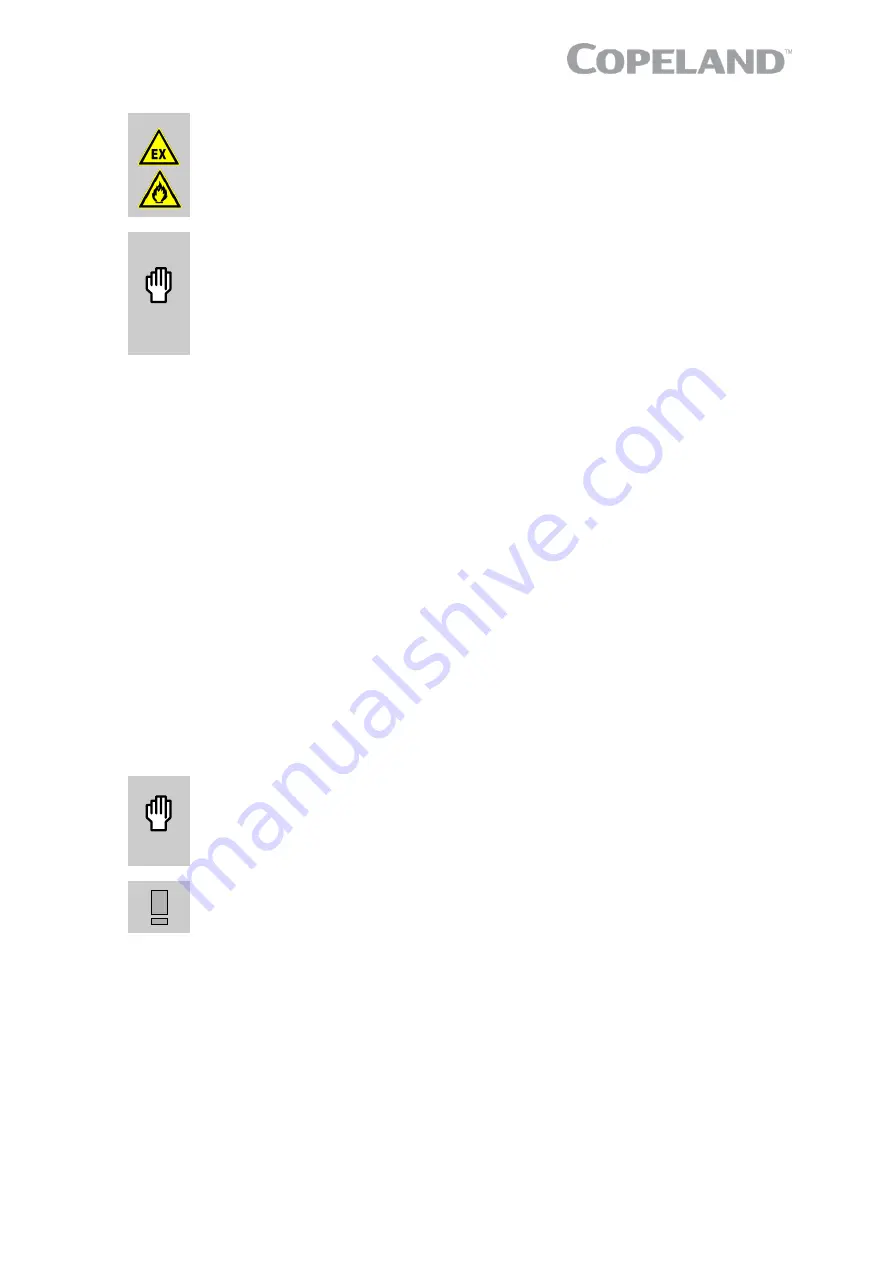
AGL_AC_ST_YRH_EN_Rev01
21
5.5 Charging procedure
WARNING
Air/A2L or A3 refrigerant mixture in a potentially flammable or explosive
atmosphere! Fire and explosion hazard!
Only use filling equipment
designed and approved for use and operation with A2L or A3 refrigerants.
Make sure all connections are tight to avoid leakage. Make sure to fill with
pure A2L or A3 refrigerant.
CAUTION
Low suction pressure operation! Compressor damage!
Do not operate
with a restricted suction. Do not operate with the low-pressure limiter bridged.
Do not operate compressor at pressures that are not allowed by the operating
envelope. Allowing the suction pressure to drop below the envelope limit for
more than a few seconds may overheat scrolls and cause early drive bearing
and moving parts damage.
Prior to charging or re-charging, the refrigerant system must be leak- and pressure-tested with
appropriate purging gas.
Ensure that the system is grounded prior to charging with refrigerant.
The system shall be liquid-charged through the liquid-receiver shut-off valve or through a valve in
the liquid line. The use of a filter dryer in the charging line is highly recommended. Systems shall be
liquid-charged on both the high and low sides simultaneously to ensure a positive refrigerant
pressure is present in the compressor before it runs. The majority of the charge shall be placed in
the high side of the system to prevent bearing washout during first-time start on the assembly line.
Extreme care shall be taken not to overfill the system with refrigerant.
NOTE: The system manufacturer/installer must respect the charge limitations according to
valid standards such as EN 378.
5.6 Run-in time
Scroll compressors exhibit a slight decrease in input power during the initial running period.
Published performance ratings are based on calorimeter testing which is carried out after run-in.
Therefore, users should be aware that before the performance specified by EN 12900 is achieved
the compressor needs to be run in. Recommended run-in times for YRH(V)*KTE/KTG compressors
to attain the published performance are 16 hours at the standard conditions.
5.7 Initial start-up
CAUTION
High discharge pressure operation! Compressor damage!
Do not use
compressor to test opening setpoint of high-pressure cut-out. Internal parts
are susceptible to damage before they have had several hours of normal
running in.
IMPORTANT
Oil dilution! Bearing malfunction!
It is important to ensure that new
compressors are not subject to liquid abuse.
Liquid and high-pressure loads could be detrimental to new bearings. It is therefore important to
ensure that new compressors are not subject to liquid abuse and high-pressure run tests. It is not
good practice to use the compressor to test the high-pressure switch function on the production line.
Switch function can be tested with nitrogen prior to installation and wiring can be checked by
disconnecting the high-pressure switch during the run test.
5.8 Starting behaviour
Due to the design of the Copeland scroll compressors, the internal compression components always
start unloaded even if system pressures are not balanced. In addition, since internal compressor
pressures are always balanced at start-up, low voltage starting characteristics are excellent for
Copeland scroll compressors.