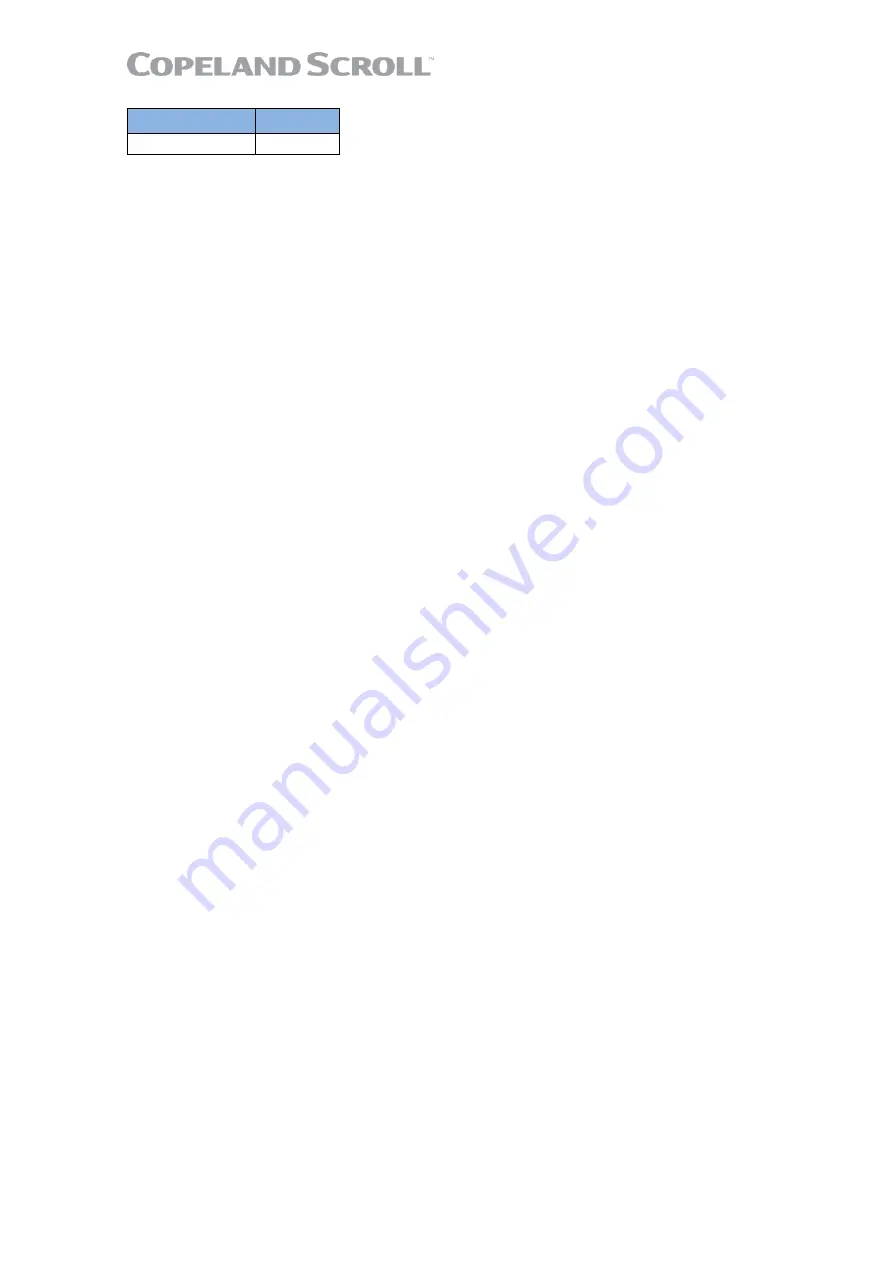
24
AGL_HP_ST_YHK1E_E_Rev02
50 Hz
Code
380-420 V / 3 ph
M
Table 9: Electrical code for YH*K1E models
5.16 Oil level
There is no oil sight glass on YH*K1E compressors.
During the system development phase, adequate oil return from the system to the compressor should
be evaluated and qualified. For this purpose, a sample compressor for lab testing, equipped with an
external oil sight tube, is available from Emerson.
The BOM GCG version contains a stub tube connection 7/8" (22.2 mm) for paralleling on the
compressor housing at oil level height.
If an oil regulator is used the oil level should be set within the top half of the oil regulator sight glass.
Содержание Copeland Scroll YH16K1E
Страница 1: ...Copeland Scroll Compressors for Heat Pump Applications YH04K1E to YH16K1E Application Guidelines ...
Страница 4: ...AGL_HP_ST_YHK1E_E_Rev02 9 References 33 DISCLAIMER 33 ...
Страница 5: ......
Страница 39: ...34 AGL_HP_ST_YHK1E_E_Rev02 ...