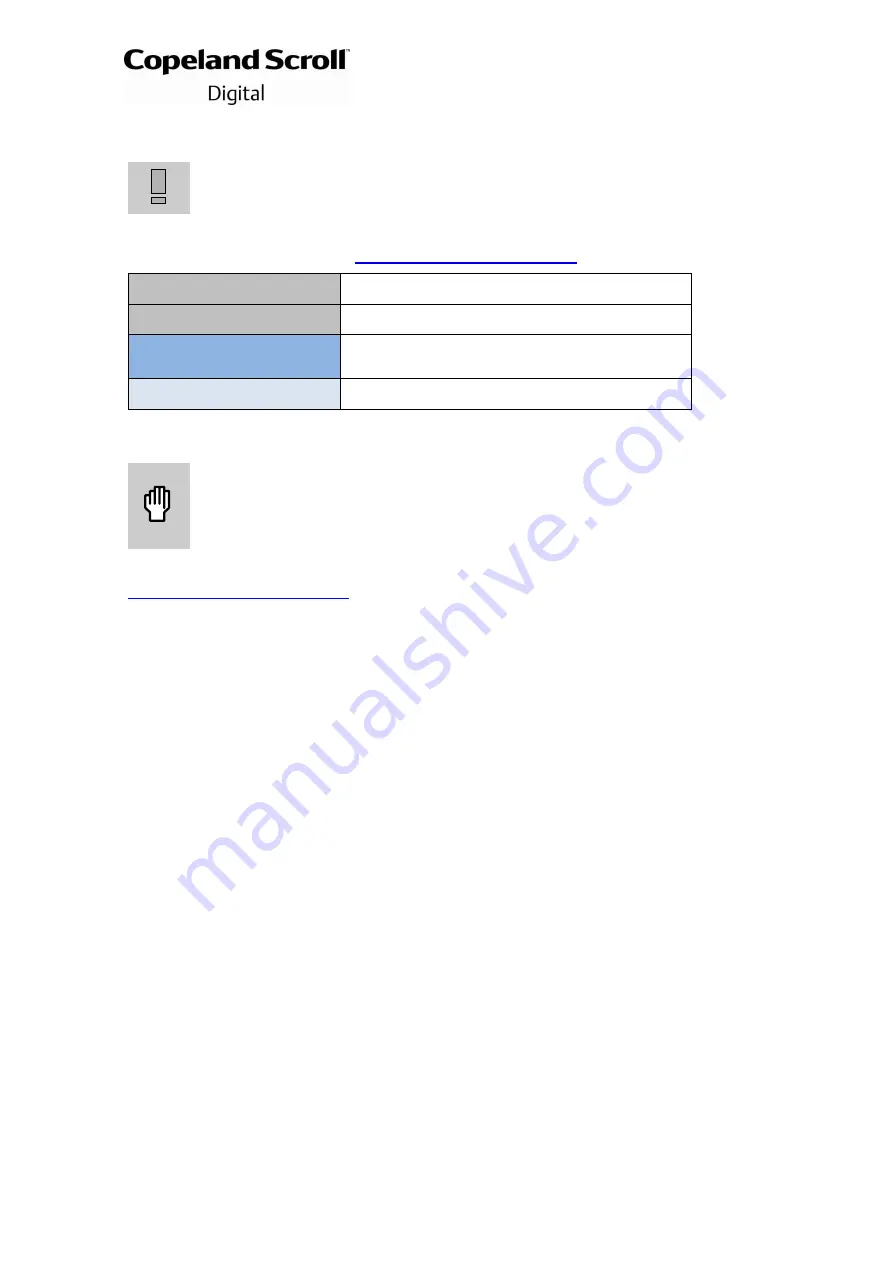
6
C6.2.44/0219/E
2.5 Application range
2.5.1 Qualified refrigerants and oils
IMPORTANT
It is essential that the glide of refrigerant blends (primarily R450A) be carefully
considered when adjusting pressure and superheat controls.
Oil recharge values can be taken from Copeland Scroll compressors brochures or Copeland
™
brand products Select software at
Compressor
ZRD*KRE
Qualified refrigerants
R450A, R513A
Copeland™ brand products
standard oil
Emkarate RL 32 3MAF
Servicing oils
Emkarate RL 32 3MAF, Mobil EAL Arctic 22 CC
Table 3: Qualified refrigerants and oils
2.5.2 Application limits and operating envelopes
CAUTION
Inadequate lubrication! Compressor breakdown!
The superheat at the
compressor suction inlet must always be sufficient to ensure that no refrigerant
droplets enter the compressor. For a typical evaporator-expansion valve
configuration a minimum stable superheat of at least 5K is required.
Application envelopes for the various refrigerants can be found in Select software, available at
.