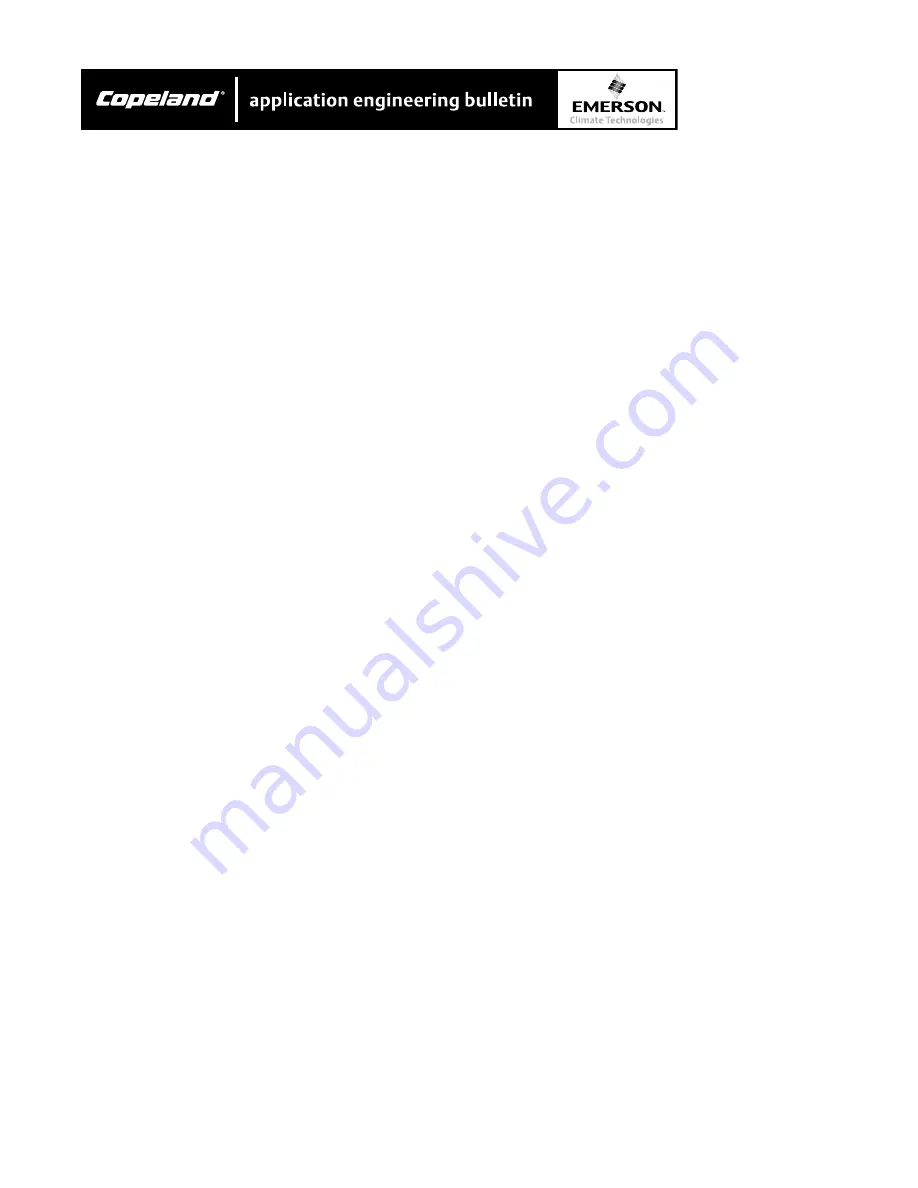
AE4-1322
© 2002 Copeland Corporation
Issued 4-2002
Printed in U.S.A.
9
Expansion valve and evaporator
Expansion valve and evaporator
Expansion valve and evaporator
Expansion valve and evaporator
Expansion valve and evaporator
Expansion valve and evaporator have to be adjusted
using utmost care. This is especially important for
those systems that cover a large control range, e.g.
100% to 25%. In each case, sufficient suction gas
superheat and stable operating conditions must be
assured in full load as well as part load modes.
Depending on the evaporator’s design and performance
range several circuits may be necessary each with
separate expansion and solenoid valves.
3.3 Guidelines for special system variations
3.3 Guidelines for special system variations
3.3 Guidelines for special system variations
3.3 Guidelines for special system variations
3.3 Guidelines for special system variations
Pump down circuit
Pump down circuit
Pump down circuit
Pump down circuit
Pump down circuit
If the evaporator and / or the suction line can become
warmer than the compressor during shutdown, a “pump
down” cycle must be incorporated in addition to the oil
heater.
Additional check valve in the discharge line and
Additional check valve in the discharge line and
Additional check valve in the discharge line and
Additional check valve in the discharge line and
Additional check valve in the discharge line and
automatic sequence control
automatic sequence control
automatic sequence control
automatic sequence control
automatic sequence control
For systems with multi-circuit condensers and / or
evaporators, an increased danger exists when indi-
vidual circuits are shut off. During this period liquid
refrigerant can migrate into the evaporator (no tempera-
ture and pressure equalization possible). In these
cases an additional check valve must be installed in
the discharge line. In addition the compressors should
be operated with an automatic sequence control.
The same is also valid for individual systems without
temperature and pressure equalization during longer
shutdown. In extreme cases a suction accumulator or
“pump down” cycle can also become necessary.
Additional oil level control
Additional oil level control
Additional oil level control
Additional oil level control
Additional oil level control
The above guidelines also apply to systems with long
pipelines (suchas a remote evaporator and / or con-
denser). In addition the compressor must be equipped
with an oil level switch (accessory). For electrical
connection see Section 6.4.
Systems with reverse cycling and hot gas defrost
Systems with reverse cycling and hot gas defrost
Systems with reverse cycling and hot gas defrost
Systems with reverse cycling and hot gas defrost
Systems with reverse cycling and hot gas defrost
These system layouts require individually system
design review to protect the compressor against liquid
slugging and increased oil carry-over. A suction
accumulator is recommended to protect against liquid
slugging. To effectively avoid increased oil carry-over
(such as due to a rapid decrease of pressure in the oil
separator), the oil temperature must remain at least
54° F above the condensing temperature during charge
over. In addition, it may be necessary to install a
pressure regulator immediately after the oil separator
to limit pressure drop. Under certain conditions it is
also possible to turn off the compressor shortly before
the change over procedure and to restart after pressure
equalization. It must however be assured that the
compressor is operating with the required minimum
pressure differential no longer than 30 seconds (see
application ranges Section 9).
3.4 Additional cooling by means of direct liquid
3.4 Additional cooling by means of direct liquid
3.4 Additional cooling by means of direct liquid
3.4 Additional cooling by means of direct liquid
3.4 Additional cooling by means of direct liquid
injection
injection
injection
injection
injection
Additional cooling is required in areas of high condens-
ing and / or low evaporating temperatures. A relatively
simple method is direct liquid inject at the economizer
connection.
The following criteria must be followed to ensure
reliable operation and to avoid excessive dilution of the
oil.
Liquid inject valve
Liquid inject valve
Liquid inject valve
Liquid inject valve
Liquid inject valve
Specially designed expansion valves are only suitable
for liquid injection. They must control the discharge
temperature to setting of 190°F (e.g. Danfoss TEAT20,
also series 935-101-B, Sporian Y1037).
The valve bulb must be mounted on the discharge line:
•
Clean the tubes surface carefully to bright metal.
Distance from discharge shut-off valve approx. 8 to
10 inches.
•
Apply heat transfer paste to the contact surface.
•
Fix the bulb firmly with adequate pipe clips. Mind
heat expansion!
•
Insulate the bulb and the section of discharge line