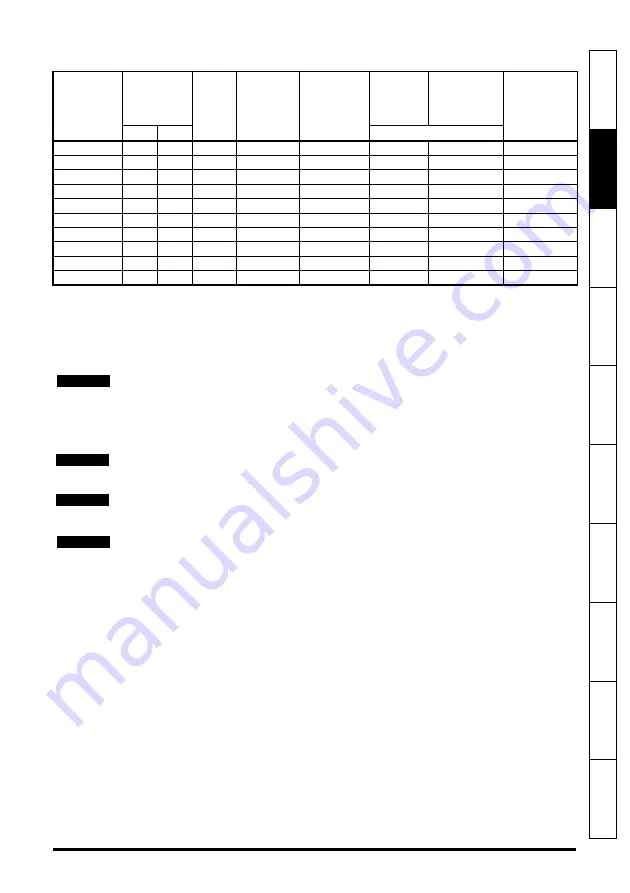
Commander SK Getting Started Guide
9
Issue Number: 9
www.controltechniques.com
S
M
El
K
P
Q
D
O
U
Table 2-4 Commander SK, 3 phase, 380 to 480Vac ±10%, 48 to 62Hz units
Output frequency
0 to 1500Hz
Output voltage
110V drives:
3 phase, 0 to 240Vac (240 Vac maximum set by Pr
08
).
200V and 400V drives:
3 phase, 0 to drive rating (240 or 480Vac maximum set by Pr
08
).
Model
Number
Nominal
motor power
Input
fuse
rating
Typical full
load input
current
Maximum
continuous
input current
100% RMS
output
current
A
150% overload
current for 60s
A
Minimum
braking
resistor value
kW
hp
A
A
A
Heavy Duty
Ω
SKB3400037 0.37
0.5
6
1.7
2.5
1.3
1.95
100
SKB3400055 0.55
0.75
6
2.5
3.1
1.7
2.55
100
SKB3400075 0.75
1.0
6
3.1
3.75
2.1
3.15
100
SKB3400110
1.1
1.5
6
4.0
4.6
2.8
4.2
100
SKB3400150
1.5
2.0
10
5.2
5.9
3.8
5.7
100
SKC3400220
2.2
3.0
16
7.3
9.6
5.1
7.65
100
SKC3400300
3.0
3.0
16
9.5
11.2
7.2
10.8
55
SKC3400400
4.0
5.0
16
11.9
13.4
9.0
13.5
55
SKD3400550
5.5
7.5
16
12.4
14.3
13.0
19.5
53
SKD3400750
7.5
10.0
20
15.6
16.9
16.5
24.75
53
110V drives contain a voltage doubler circuit on the AC input.
NOTE
The output voltage can be increased by 20% during deceleration. See Pr
NOTE
The output frequency can be increased by 20% during deceleration. See Pr
NOTE
The maximum continuous current inputs are used to calculate input cable and fuse
sizing. Where no maximum continuous input currents are indicated, use the typical full
load input current values. See
Commander SK Technical Data Guide
for cable and fuse
data.
NOTE
Содержание Commander SK
Страница 53: ......