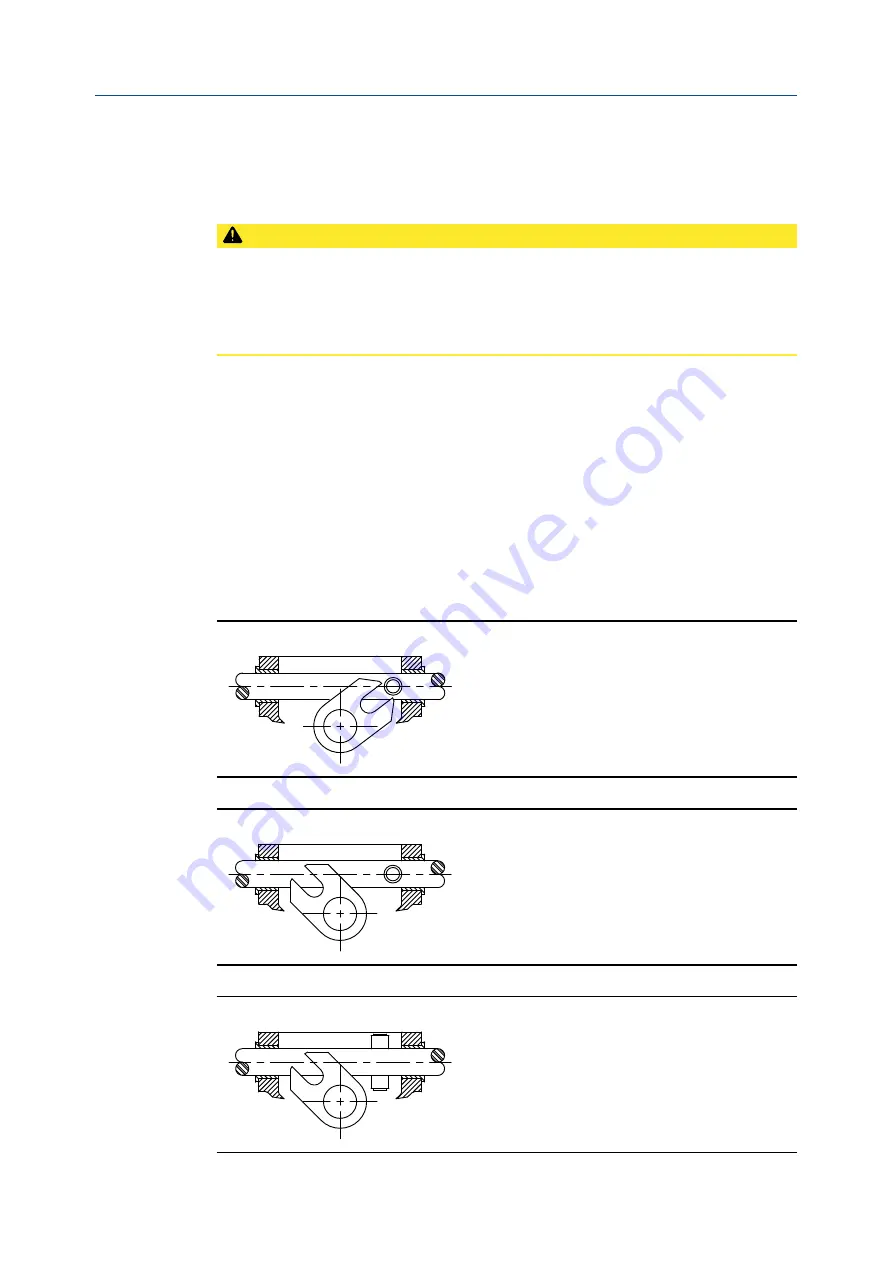
Installation, Operation and Maintenance Manual
MAN-02-01-39-0704-EN Rev. 0
July 2019
Removal of Actuator from Valve
Section 8: Removal of Actuator from Valve
CAUTION
Do not attempt to remove mounting bolts between actuator and valve until supply pres
-
sure has been disconnected and vented. If spring return, be sure that valve is completely
in failed position. If valve is frozen in a position causing the spring to be cocked, removal of
bracket bolts would allow spring to stroke, resulting in the actuator rotating over bracket
causing possible injury or damage.
A.
Loosen bracket to actuator bolts to hand tight position.
B.
Physically shift actuator back and forth to be sure there is no strain (or shear
stress) on the bracket bolts. Once it has been determined that there is no pressure
or spring coil remaining in the actuator, remove bolts and remove actuator and
coupling from valve.
C.
In the event the valve is frozen or locked in place, resulting in spring energy
remaining in the actuator, replace adjusting screw (37) on end of actuator
opposite spring end with length of ‘all thread’ rod of sufficient length and turn
clockwise until it contacts the piston. This procedure will safely secure the piston
and spring assembly and allow actuator removal. Be sure to remove "all thread" rod
prior to actuator disassembly.
Figure 5
Figure 6
Figure 7
13
Section 8: Removal of Actuator from Valve
Содержание Bettis M Series
Страница 29: ......