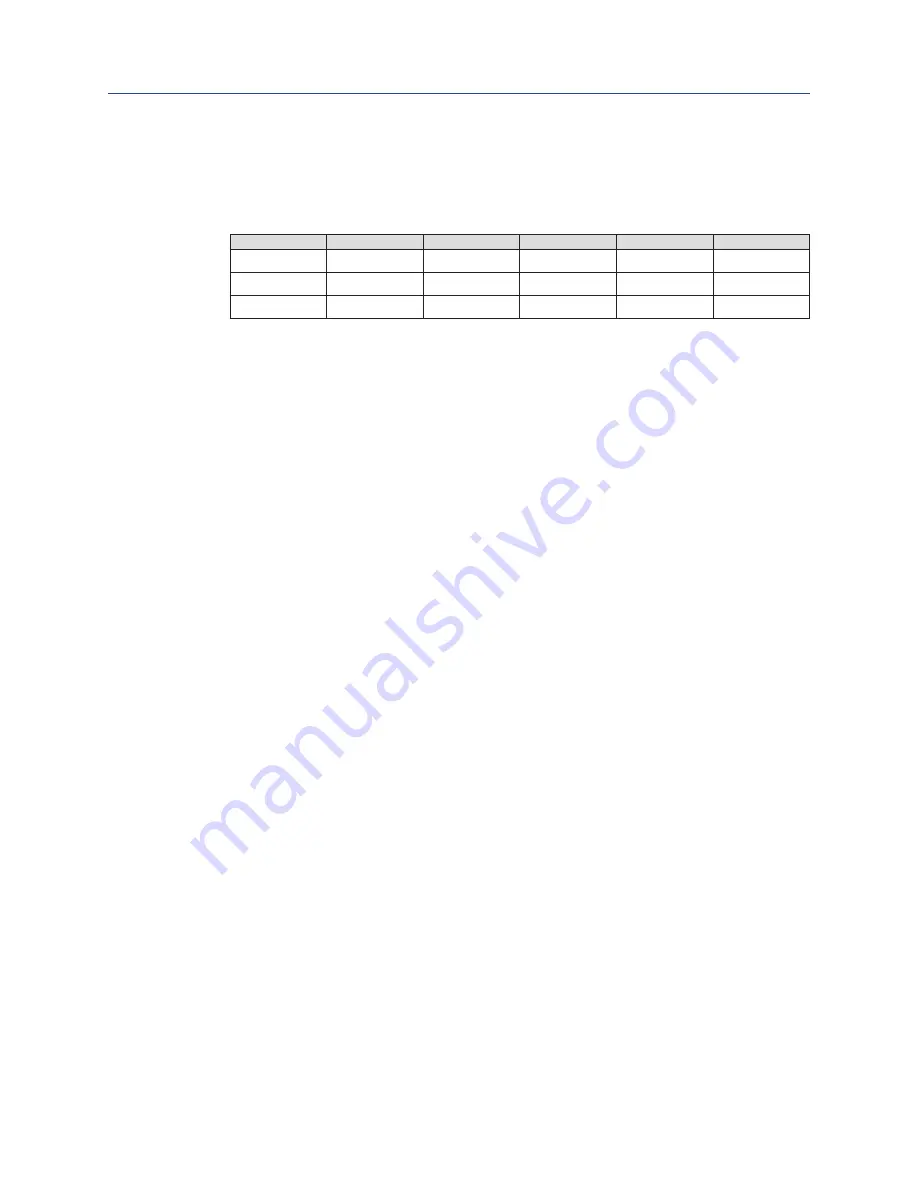
Service Instructions
124843E Rev. C
August 2015
42
Section 9: Document Revision
Document Revision
Section 9: Document Revision
Table 17�
Revision Overview
ECN
DATE
REV
BY *
DATE
Released
Jan. 2002
A
B.Cornelius
Jan. 2002
19110
July 2006
B
UPDATED
C. Ross
July 2006
VAWCO2750
Aug. 2015
C
UPDATED
C. Rico
Aug. 2015
* Signatures on file Bettis, Houston, Texas