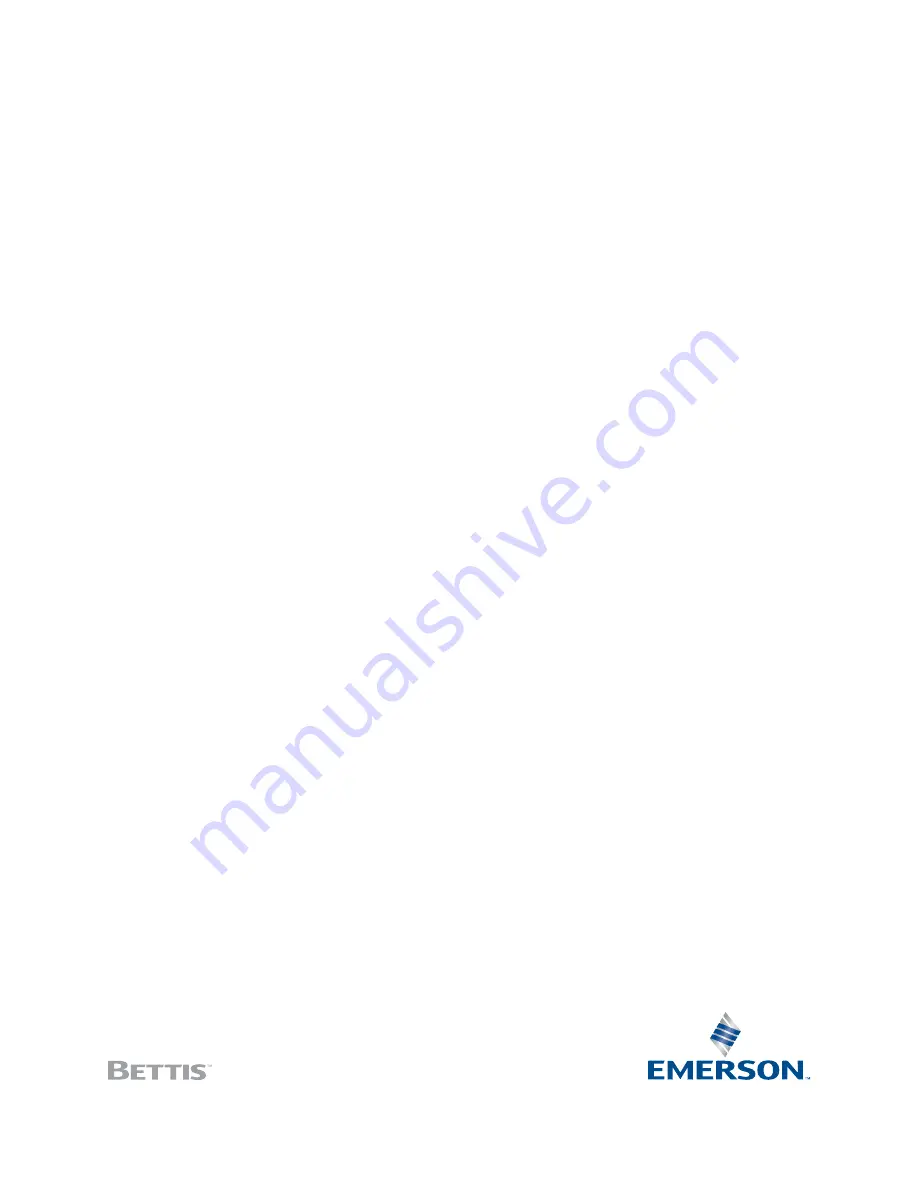
World Area Configuration Centers (WACC) offer sales support, service,
inventory and commissioning to our global customers.
Choose the WACC or sales office nearest you:
www.emerson.com/bettis
VCIOM-15296-EN ©2020 Emerson. All rights reserved.
The Emerson logo is a trademark and service mark of Emerson Electric Co.
Bettis
TM
is a mark of one of the Emerson family of companies.
All other marks are property of their respective owners.
The contents of this publication are presented for information purposes
only, and while effort has been made to ensure their accuracy, they are not
to be construed as warranties or guarantees, express or implied, regarding
the products or services described herein or their use or applicability.
All sales are governed by our terms and conditions, which are available
on request. We reserve the right to modify or improve the designs or
specifications of our products at any time without notice.
For complete list of sales and manufacturing sites, please visit
www.emerson.com/actuationtechnologieslocations
or contact us at
NORTH & SOUTH AMERICA
19200 Northwest Freeway
Houston TX 77065
USA
T +1 281 477 4100
Av. Hollingsworth
325 Iporanga Sorocaba
SP 18087-105
Brazil
T +55 15 3413 8888
ASIA PACIFIC
No. 9 Gul Road
#01-02 Singapore 629361
T +65 6777 8211
No. 1 Lai Yuan Road
Wuqing Development Area
Tianjin 301700
P. R. China
T +86 22 8212 3300
MIDDLE EAST & AFRICA
P. O. Box 17033
Jebel Ali Free Zone
Dubai
T +971 4 811 8100
P. O. Box 10305
Jubail 31961
Saudi Arabia
T +966 3 340 8650
24 Angus Crescent
Longmeadow Business Estate East
P.O. Box 6908 Greenstone
1616 Modderfontein Extension 5
South Africa
T +27 11 451 3700
EUROPE
Holland Fasor 6
Székesfehérvár 8000
Hungary
T +36 22 53 09 50
Strada Biffi 165
29017 Fiorenzuola d’Arda (PC)
Italy
T +39 0523 944 411