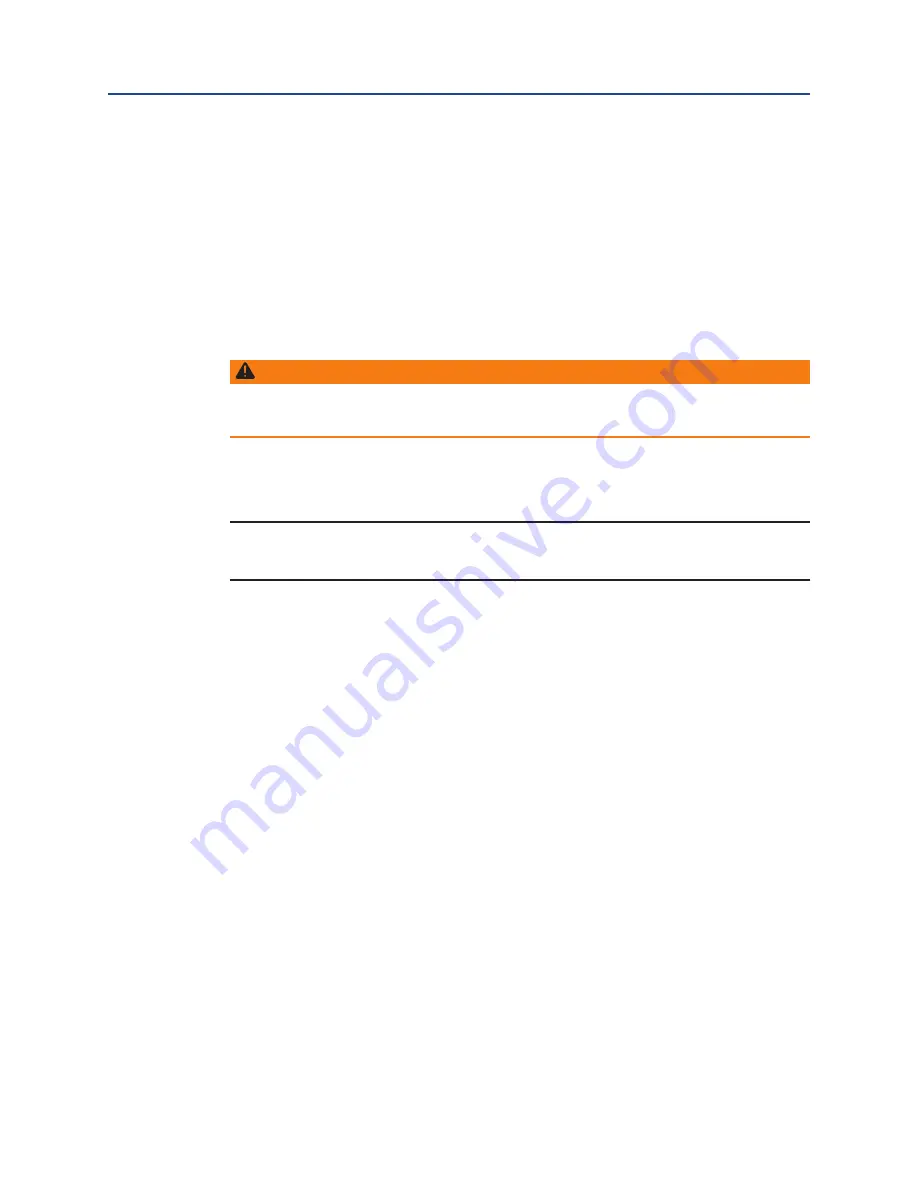
October 2015
Service Instructions
VA001-196-30 Rev. 1
20
Section 4: Actuator Testing
Actuator Testing
Section 4: Actuator Testing
4�1
Actuator Testing
4�1�1
Leak Test: A small amount of leakage may be tolerated. Generally, a small bubble
which breaks about three seconds after starting to form is considered acceptable.
4�1�2
All areas, where leakage may occur, are to be checked using a commercial leak
testing solution.
WARNING: DO NOT EXCEED RATED PRESSURE
Pressure is not to exceed the maximum operating pressure rating listed on the serial
number tag (20).
4�1�3
All leak testing will use the customer normal operating pressure or the actuator
name tag normal operating pressure (NOP).
NOTE:
When testing the actuator use a proper adjusted regulator to apply pressure to the actuator.
4�1�4
Before testing for leaks, apply and release the pressure listed in step 4.1.3 to both
sides of the piston. Repeat this cycle approximately five times. This will allow the
new seals to seek their service condition.
4�1�5
Apply the pressure listed in step 4.1.3 to the housing side of the piston and allow
the actuator to stabilize.
4�1�6
Apply a leak testing solution to the following areas:
4�1�6�1
Cylinder to housing joint on CBB315, 420, and 525 or cylinder to cylinder
adapter to housing joints on CBB520 and 725 actuators.
4�1�6�2
On the outboard end of housing (1-10) at the center bar hex nut. Check
the center bar to housing O-ring seal (5-20).
4�1�6�3
Housing stop screw / ES / M3 jackscrew O-ring seal (2-30).
4�1�6�4
Torque shaft (1-30) to housing (1-10) interface. Check O-ring seals (2-25)
and (2-20).
4�1�6�5
End cap (4-20) port “hole”. Checks the piston to cylinder seal (5-40) and
piston to center bar seal (5-20).
4�1�7
Apply the pressure listed in step 4.1.3 to the end cap inlet port and allow the
actuator to stabilize.
4�1�8
Apply a leak testing solution to the following areas:
4�1�8�1
Cylinder to end cap joint. Check O-ring seal (5-10) on CBB315, 420, and
525 or check O-ring seal (5-15) on CBB520 and 725 actuators.
4�1�8�2
Housing (4-10) inlet port hole. Checks the piston to cylinder seal (5-40)
and piston to center bar seal (5-20).
4�1�8�3
End cap stop screw or M3 jackscrew O-ring seal.
4�1�8�4
Remove pressure from pressure inlet port in the end cap (4-20).