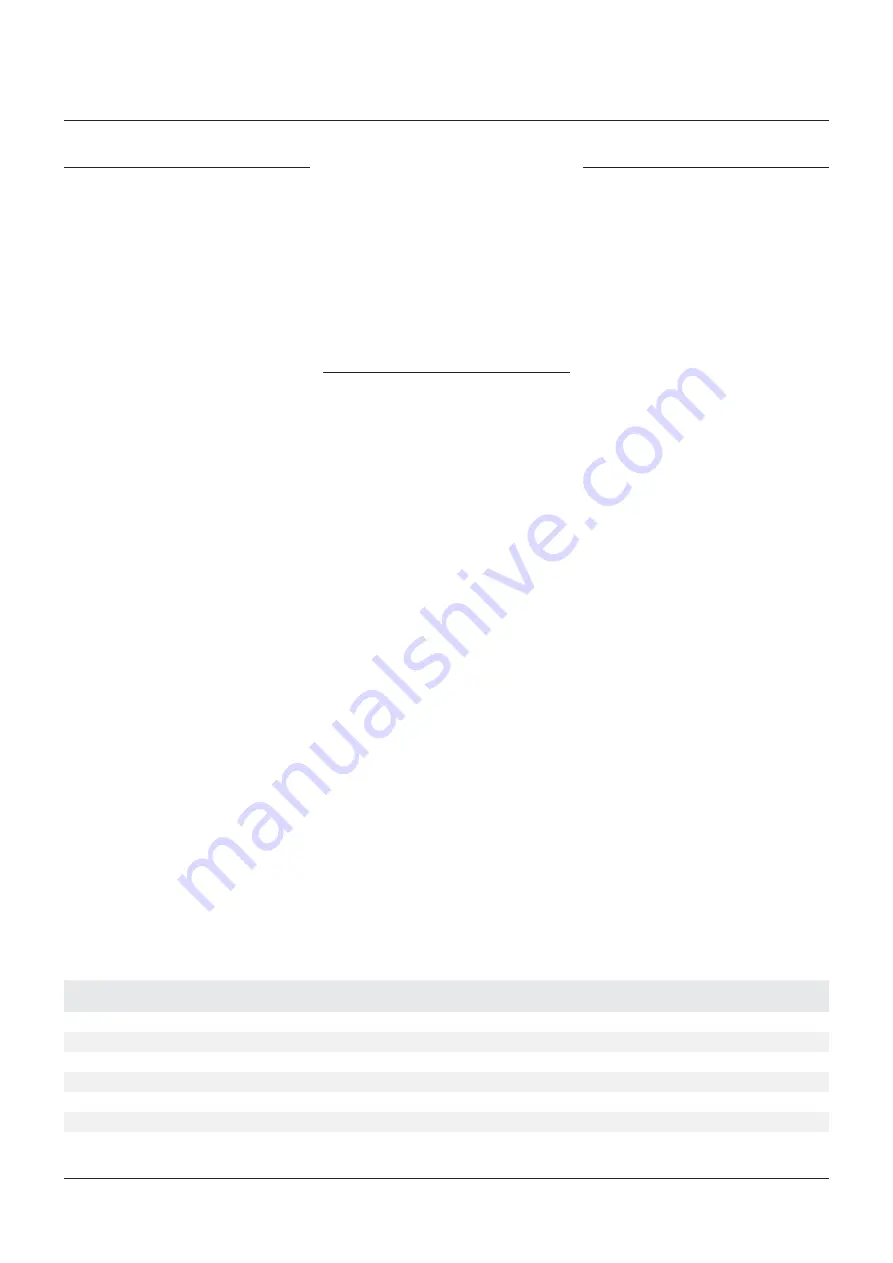
ANDERSON GREENWOOD
4020HP PRESSURE AND VACUUM RELIEF VALVE
INSTALLATION, OPERATION AND MAINTENANCE INSTRUCTIONS
5.0 INSTALLATION
1. Ensure that the mating connection to the
tank is flat machined horizontal flange.
2. Thoroughly clean the mating connection to
remove all foreign matter which could lead
to valve leakage if trapped between the valve
seat and the pallet.
3. Ensure that the bore diameter of the tank
connection nozzle is at least equal to the
inlet bore of the valve connection.
4. For correct valve operation, there should be
no external loads applied to the valve body.
5. Fit an inlet gasket to the mating flange
ensuring it does not obstruct the flow path.
6. Install the valve. Ensure that the main axis of
the valve is perpendicular.
7. Tighten the flange bolting uniformly to
ensure a good seal.
NOTE
The valve connection flange will have a
combination of plain through holes, tapped
through holes and blind tapped holes. The thread
form of the tapped holes can be found from
Table 1.
For valves of aluminium construction,
appropriate flat face flanges should be used
and a full-face gasket fitted.
6.0 MAINTENANCE
Regular inspection should be carried out
to ensure that the pressure and vacuum
ports are free from debris and that nothing
preventing the correct operation of the valve is
present. Maintenance should be performed at
regular intervals and should be carried out by
suitably qualified personnel in an appropriately
equipped workshop. Alternatively, the valve
should be returned to the manufacturer or
suitably authorized agent for service/repair.
During transport to the workshop the valve
should be kept vertical to prevent damage to
the internals.
WARNING
The relief valve must be isolated from tank
pressure before servicing or removing. All gas/
vapour must be blocked and pressure safely
vented. Wear appropriate protective clothing and
breathing apparatus if hazardous gas/vapours
are present.
NOTE
Storage tank inlet piping configurations should
conform to recognized standards. Different
configurations will develop different inlet pressure
losses when the valve is flowing. This should be
taken into consideration when sizing the valve for
the application.
It is recommended that the external surfaces
of carbon steel valves are painted immediately
after installation.
TABLE 1 - INLET FLANGE THREAD FORMS
Size,
In. (mm)
Imperial
ANSI 125, 150
Metric
PN10
Metric
PN16
7.0 VALVE DISASSEMBLY (SEE FIGURE 1)
Before the valve is disassembled it should be
thoroughly cleaned to remove potential hazards
from process contamination.
IMPORTANT
During disassembly, it is important to identify
the pressure and vacuum pallets so that on
reassembly they are returned to the correct seat.
7.1 Pressure Side
1. Remove cap [P19] and release locknut [P18].
2. Remove all load from spring by removing
adjusting screw [P16] complete
with locknut.
3. Remove nuts [P9], washers [P8] and
casing [P2].
4. Remove upper spring plate [P15]. For values
6" (150 mm) and above, recover skid ring
[P17] which is lifted between the adjusting
screw and upper spring plate.
5. Remove spring [P14] and stem [P13]
complete with lower spring plate [P12].
6. Remove weather hood [P1], bird screen [P5]
and remove ball [P11]. Lift out pressure
pallet assembly [P10].
7. Remove seat [P3] complete with guide posts
[P4] by removing cap screws [P6].
8. Remove O-ring [P7]. Identify pallet assembly
and seat pressure side parts.
5
2 (50)
5
/
8
– 11 UNC
M16 x 2
M16 x 2
3 (75)
5
/
8
– 11 UNC
M16 x 2
M16 x 2
4 (100)
5
/
8
– 11 UNC
M16 x 2
M16 x 2
6 (150)
3
/
4
– 10 UNC
M20 x 2.5
M20 x 2.5
8 (200)
3
/
4
– 10 UNC
M20 x 2.5
M20 x 2.5
10 (250)
7
/
8
– 9 UNC
M20 x 2.5
M24 x 3
12 (300)
7
/
8
– 9 UNC
M20 x 2.5
M24 x 3