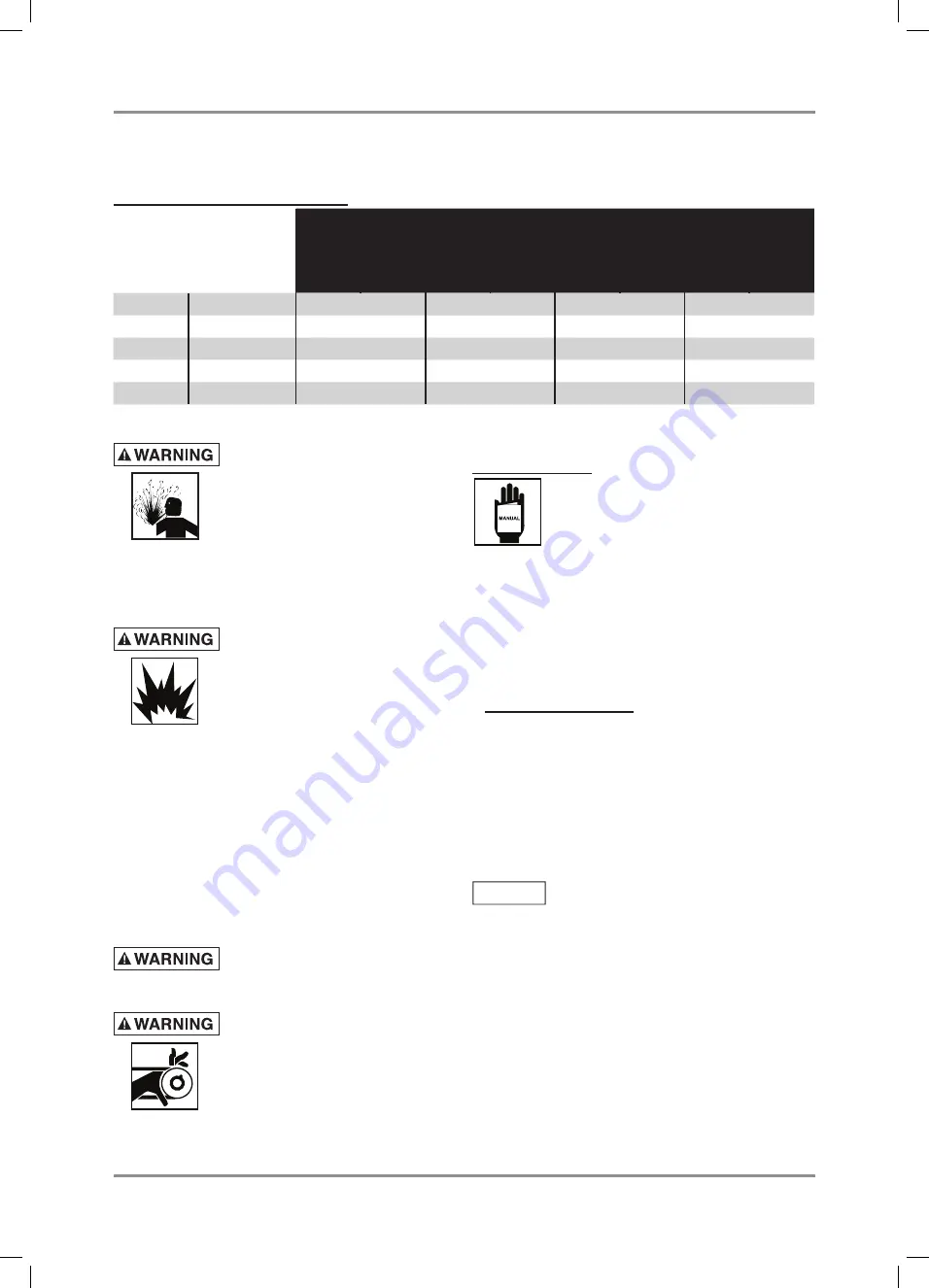
23
EGES14020T man v.190417
Operating Instructions
6.
INSTALL APPROPRIATE ASME-CODE
SAFETY VALVES
and make sure piping system
is equipped with adequate condensate drains.
Piping / Tank Installation
Never install a shut-off valve
such as a globe or gate valve,
between the pump discharge
and the air tank unless a safety
valve is installed in the line
between valve and pump.
7.
MAKE SURE
any tube, pipe or hose connected
to the unit can withstand operating temperatures
and retain pressure.
Never use plastic (PVC) pipe
for compressed air.
Serious injury or death could
result.
8.
NEVER USE REDUCERS IN DISCHARGE
PIPING.
Keep all piping and fittings the same
size in the piping system.
9.
FOR PERMANENT INSTALLATIONS OF
COMPRESSED AIR SYSTEMS, DETERMINE
TOTAL LENGTH OF SYSTEM AND SELECT
CORRECT PIPE SIZE.
Make sure underground
lines are buried below frost line and avoid areas
where condensation could build up and freeze.
10.
TEST THE ENTIRE PIPING SYSTEM
before
any underground lines are buried. Be sure to find
and repair all leaks before using compressor.
Never exceed recommended
pressure or speed while
operating compressor.
Re-install the beltguard on
unit after pump installation is
complete.
Minimum Pipe Size
for Compressed Air
Lines
Length of Piping System
Standard air volume
25 ft.
7.6 m
50 ft.
15.2 m
100 ft.
30.5 m
2
50 ft.
76.2 m
20 CFM
566.34 L/min
3/4 in.
3/4 in.
3/4 in.
1 in.
40 CFM 1132.67 L/min
3/4 in.
1 in.
1 in.
1 in.
60 CFM 1699.01 L/min
3/4 in.
1 in.
1 in.
1 in.
100 CFM 2831.68 L/min
1 in.
1 in.
1 in.
1-1/4 in.
125 CFM 3539.61 L/min
1-1/4 in.
1-1/4 in.
1-1/4 in.
1-1/2 in.
Lubrication
Be sure the engine is supplied with the
correct lubricating oils in the correct
places as mentioned in the engine
manual:
1. Engine crankcase lubricant: 10W-30 high quality
detergent oil is a good most-cases choice. Check
the maintenance section of the Kohler engine
service manual for details. Be sure the crankcase
is filled to the appropriate mark on the oil dipstick,
not overfilled. It should be changed out after the
engine break-in period, i.e. after the first five
hours.
Low-oil shutdown
The low-oil shut-down feature on this piece of
machinery applies only to the gas engine. It is
intended to prevent accidental running of the engine
when the oil is insufficient to lubricate it properly
and cause it to over-heat. However, this does not
mean the operator should not always keep watch
on the engine oil level. Do not rely on Oil Sentry™
to shut the engine down. In addition, there is also a
continuing need to monitor and maintain oil levels in
the reduction gearing and in the compressor pump.
The low-oIl switch is designed to
prevent engine from starting in a
low oil or no oil condition. Oil Sentry™ may
not shut down a running engine before
damage occurs.
2. Oil-bath air cleaner: Check oil level in oil reservoir
cup; add oil if below oil level mark; do not overfill.
Use the same oil as for the engine crankcase.
Be sure the compressor pump is lubricated correctly.
This unit is shipped with compressor pump break-in
oil and should be ready to operate.
3. Check the oil level. It should show in center of the
compressor pump oil sight glass
. Refer to JF, fig.6
and fig.8, below.
NOTICE