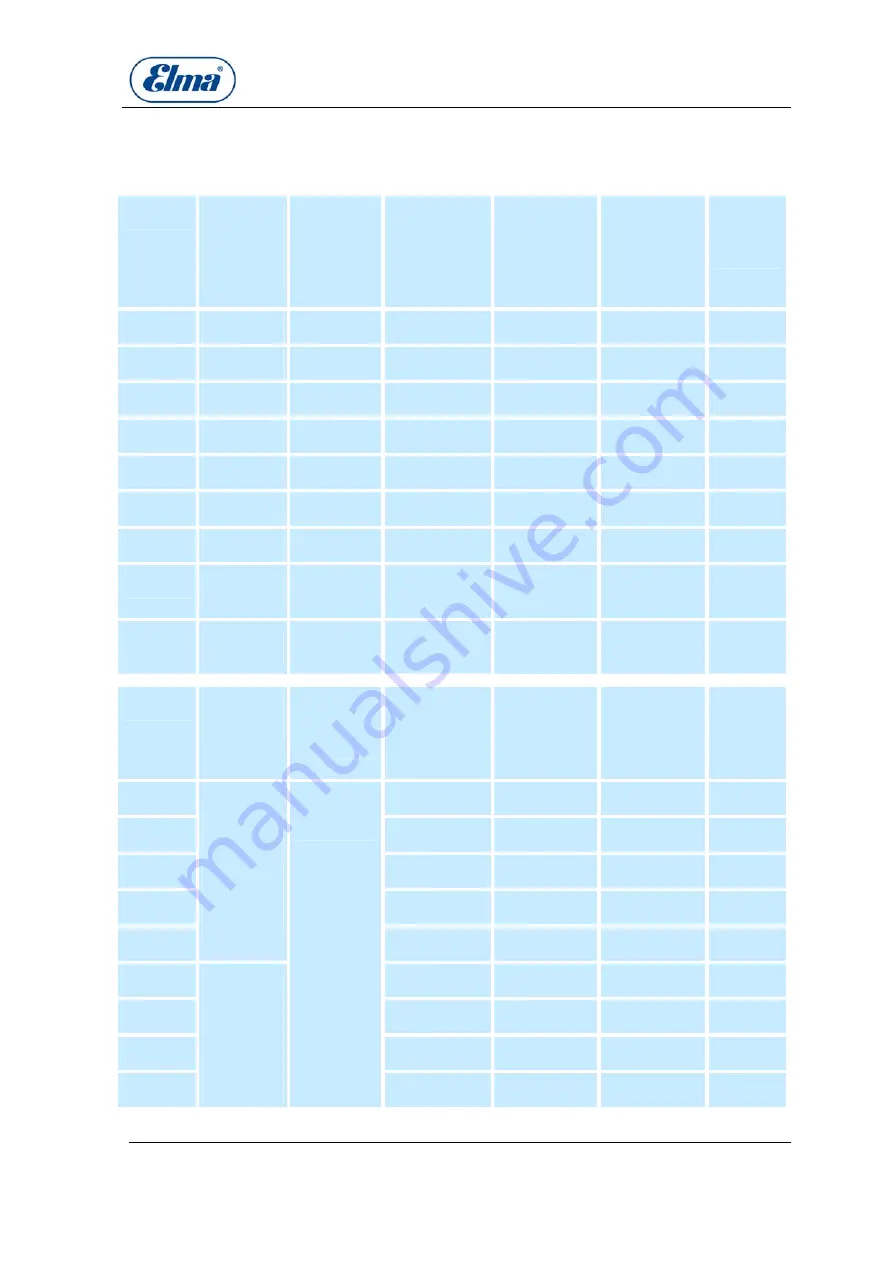
Product description
© Elma GmbH & Co KG
BA/ Transsonic TI-H_GB_0306
7
4.6 Technical
details
Max. tank
volume
(approx.
liter)
Tank
service
volume
(approx.
liter)
Tank inner
dimensions
W x D x H
(approx. mm)
Unit outer
dimensions
W x D x H
(approx. mm)
Basket inner
dimensions
W x D x H
(approx. mm)
Weight
(approx.
kg)
TI-H 5
4.7
3.5
240x130x150
340x300x370
200x100x90
10,5
TI-H 10
10.8
8.6
300x240x150
400x415x370
260x210x85
14,8
TI-H 15
14.4
12.2
300x240x200
400x415x420
260x210x130
16
TI-H 20
19.8
16.8
330x300x200
430x470x420
290x270x130
20
TI-H 25
25.5
19.8
330x300x230
615x690x570
290x270x140
32
TI-H 55
57.8
45
500x300x350
620x850x570
255x460x210
35
TI-H 80
82.5
67.5
500x300x500
620x850x720
255x460x290
60
TI-H 115
115.5
90
600x500x350
840x1000x
570
450x545205
100
TI-H 160
160
135
600x500x500
840x1000x
720
440x540x350
140
Mains
connections
Ultrasonic
frequency
(kHz)
Power
consumption
total
(W)
Ultrasonic
power
effective
(W)
Ultrasonic
peak max
*
(W)
Heating
power (W)
TI-H 5
500
100
400
400
TI-H 10
1000
200
800
800
TI-H 15
1200
200
800
1000
TI-H 20
1650
250
1000
1400
TI-H 25
100-120V
or
200-240V
1 phase
1 N
1 PE
earthing
contact
1300
300
1200
1000
TI-H 55
3600
600
2400
3000
TI-H 80
4900
900
3600
4000
TI-H 115
7400
1400
5600
6000
TI-H 160
200-208V
or
380-400V
3 phasen
1 N
1 PE
earthing
contact
SF1 35 kHz
or
MF2
25/45 kHz
or
MF3
35/130 kHz
7600
1600
6400
6000
*
Due to the form of the signal the value of the ultrasonic peak maximum is four times higher