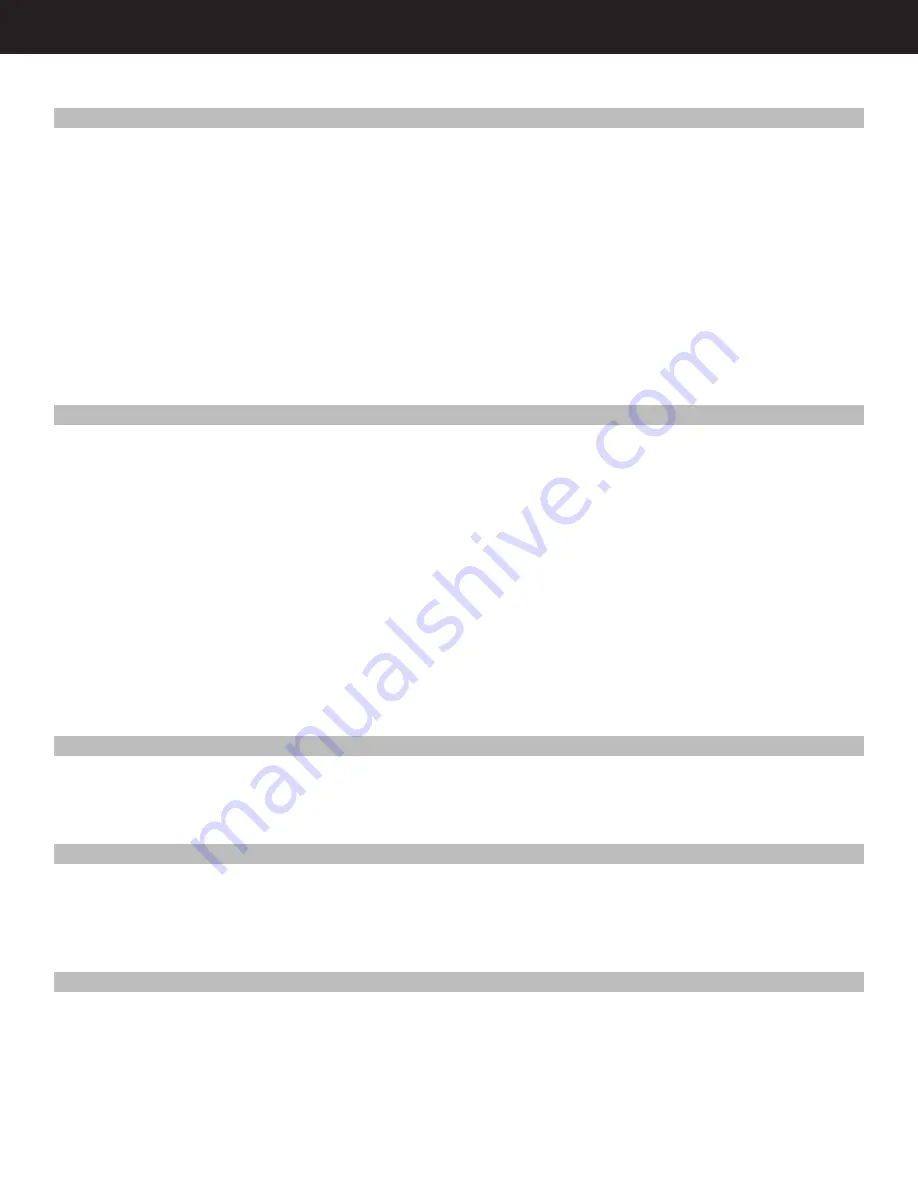
I
N S T A L L A T I O N
& O
P E R A T I O N
Page 6
Troubleshooting Crooked Cuts
1. Check blade for worn or broken teeth and replace if needed.
2. Check to make sure that the number of teeth per inch on the
blade fit the application. As a rule, only 6 to 12 teeth should
be in contact with the workpiece.
3. Check the head pressure on the saw. The compensating
spring tension should be 8 pounds with the blade 1" above
the table, coming down with the hydraulic valve open.
4. Check the blade tension. Review the proper blade tension
procedure under “Removing and Replacing Blade” on page
5, item 10.
5. Check the space between bearings of both guide bearing
assemblies. It should be only .001" over the thickness of a
new blade. As an example, a .033" feeler gauge would be
used to set the guides for a .032" thick blade.
6. Check the blade tracking on the idler and drive wheels.
9" solid wheels:
blade in center of wheels
12" spoked wheels:
3/4" wide blade should have teeth
protruding from the side of the wheel about 1/8", and
the 1" wide blade about 1/4".
14" spoked wheels:
1" and 1-1/4" wide blades should
have teeth protruding 1/4" to 5/16" from side of wheel.
7. Check to make sure that the blade guide assemblies are not
too far apart. Set the idler blade guide closer to the work to
provide greater support for the blade.
Saw Adjustments
1. Squaring blade with back of saw table.
Raise the head up 1/8" and hold in place with the hydraulic
valve. Place a 6" square against the table back and move the
head until the blade is exactly 90 degrees from the table
back. Lock the head in position. Check that the POINTER
points to zero (0 degrees) on the degree plate. If the pointer
does not point to zero, bend the pointer so that it lines up to
0 degrees. The saw is now adjusted to cut from front to back
accurately at 90 degrees and at all angles.
2. Square blade with top of saw table.
Use a blade aligning tool of the “clip on” or magnetic type to
attach to the blade. Set a 6" square on the table top with the
blade vertical and touching the aligning tool. These test
measurements should be made with the tools kept as close as
possible to the guide bodies. If the blade is not square with
the table, the guide bearing plate needs to be adjusted to
bring the blade into alignment.
See illustration of Blade
Guide Assembly on page 2.
First the wing nut, Item 9 in the illustration, must be loos-
ened. Next, loosen nut, Item 13. The adjustment to the bear-
ing plate is set using the cap screw, Item 14. If the adjust-
ment requires that the cap screw be backed out, the adjust-
ment stud, Item 2, must be manually pushed so it is in con-
tact with the cap screw. When the blade is aligned parallel
with the square, tighten the wing nut to lock the bearing
plate in position. Hold the cap screw from turning and lock
nut, Item 13, against the guide clamping bolt.
Blade Speeds
The V-belt must be changed on the pulleys to change speeds.
For HIGH speed, place the belt in the largest pulley on the
motor shaft and the smallest on the reducer shaft.
For MEDIUM speed, the middle pulley is used on both shafts.
For LOW speed, the smallest pulley on the motor shaft is used
with the largest on the reducer.
Replacement of Hydraulic Oil
The hydraulic cylinder can be filled on the saw or in a bench
vise.
THE SHAFT MUST BE FULLY PUSHED IN BEFORE
STARTING TO FILL.
1. Remove pipe plug from near top of cylinder.
2. Fill with light weight hydraulic oil until oil flows back out of
hole. Replace pipe plug.
Maintenance
A good clean machine is easy to operate and promotes safety.
1. Keep areas clean by brushing chips from table grooves,
guide bodies, idler and drive wheels, pivot shaft hinge area
and turntable grooves.
2. Oilite bushings in pivot shaft should be oiled annually.
3. Check oil level in hydraulic. Proper level is at pipe plug hole.
4. Oil in wormgear should be checked every 90 days. FILL TO
PROPER LEVEL AT PLUG, BELOW THE BREATHER
VENT, using 80 to 140 weight gear oil.
(If above steps did not eliminate crooked cuts)