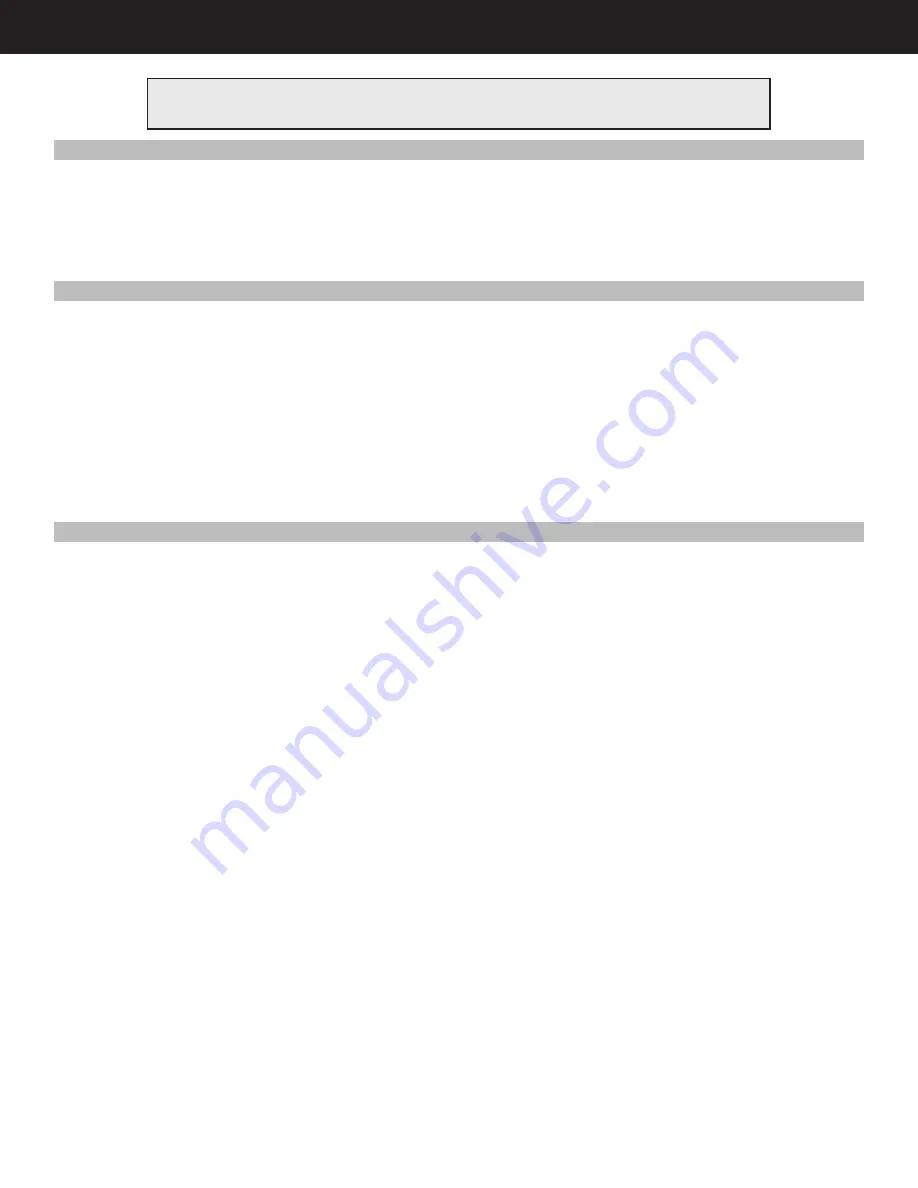
I
N S T A L L A T I O N
& O
P E R A T I O N
Page 5
Installation Instructions
1. Visually inspect machine for hidden shipping damage.
2. As part of the receiving inspection, check for broken ball
bearings on the bearing carrier assembly. This is the assem-
bly that the saw swivels on for miter cuts. CHECK ALL SIX
BEARINGS. Two are located in the groove under the
degree plate.
See illustration on page 4.
Vertical Sawing Position
NOTE: Model 1800 only – before raising the head on the
Model 1800, remove the head weight adjustment hand-
wheel and install the 6021 T-Nut. Attach the threaded
vertical support bar (6022) tightly to the rear of the drive
housing. See the chart on page 8. Adjust, if needed, to
square blade with the vertical table.
1. Pull hydraulic pin at bottom of hydraulic. Disengage com-
pensating spring assembly. Head is now free to raise to ver-
tical position. Raise head up and over center. Hold head
and gently let it move up to vertical position. DON’T LET
THE HEAD DROP!
See illustration on page 8, or video.
2. Slide the vertical saw table into the blade and against the
back of the horizontal table. Secure with the screwless vise
or C-clamps. Adjust the drive end of the blade guide assem-
bly, if necessary, to provide support for that end of the ver-
tical table.
3. Attach the vertical blade guard on the moveable guide arm
and secure with wing nut supplied.
4. Position moveable arm as close to work as possible.
Removing and Replacing Blade
Call 1-800-383-5547 for experienced help in selecting the
proper saw blades for your application.
1. Disconnect power supply cord from power source.
2. Raise saw head assembly until blade clears the back of the
table. Close hydraulic valve to lock in position.
3. Open the covers of the idler and drive wheels.
4. Pivot the chip brush to horizontal position and lock in place.
5. Loosen blade tension T-handle sufficient to release the blade
around the wheels. Pull blade out of the blade guide bearings.
6. Brush chips from blade guide bearings and housings. Wipe
bearing surfaces clean. Check that all bearings are running free.
7. Check that the guide bearings are set correctly for the new
blade thickness. Use a feeler gauge that is one thousandth of
an inch thicker than the blade. This is the best method because
it does not rely on judgement.
A saw blade can also be used as a gauge, but it must be new.
After the blade has been installed and under proper tension,
check for proper spacing. Twist the blade at the idler and drive
wheel side of the respective guide bearing housings. There
should not be any noticeable motion of the blade on the other
side of the guide bearings. Reset the gap to correct fit.
8. Place the new blade over the idler and drive wheels with the
teeth facing toward you. The blade should run under the
guides. The teeth should point out toward you and the tips of
the teeth should point toward the motor end of the saw.
A fast check is to compare the blade (as you place it over the
idler wheel) with the decal on the top of the saw head. Check
to make sure the blade is on both orange wheels.
9. By turning the T-Handle, apply tension to the blade until all
slack is removed from the blade or the blade is pulled in a
straight line across the top of the saw from wheel to wheel.
Grasp the blade on each side of the guides and twist the
blade. Push down on the teeth with your thumbs and roll the
back of the blade between the guide bearings. Proper tension
is 1-1/2 to 2 full turns (360) of the T-Handle.
10. Proper blade tension is reached by grasping the T-Handle and
applying one full turn (360) on the tension handle. You can
use the casting number on the handle as a reference point.
Reconnect the power supply. Turn the saw on for a couple of
revolutions to square the blade on the wheels. Turn the saw
off. Now put the second full turn of tension on the T-Handle.
Turn the saw on again for a few revolutions. Turn the saw
off. Check the tracking of the blade on the wheels. On saws
with a 9" wheel the blade runs centered on the wheels. On
saws with 12" and 14" wheels the teeth of the blade should
be sticking out past the edge of the wheel. The teeth should
not be on the rubber of the idler or drive wheels. If the blade
is not tracking properly then the idle wheel needs to be
adjusted. If you think the idle wheel needs to be adjusted, call
the factory at 1-800-383-5547 for assistance.
11. Check the blade tension by setting the guide housings about
8" apart then grasp the blade between the fingers and thumb
halfway between the guide housings. With a rotating or
twisting motion of the hand the blade should deflect no more
than 1/8".
A video is available showing the proper procedure for
removing and replacing blades, saw adjustments, trou-
bleshooting and maintenance. If you did not receive a
video with this machine or would like another copy, call
the factory.
CAUTION:
Disconnect power supply cord from power source before
changing the blade or making any other repair or adjustment to the saw.
IMPORTANT
Model 2000, 3000 and 4000 owners note: The shut off rail was removed
for shipping. You must mount the rail on the machine table before using the saw.